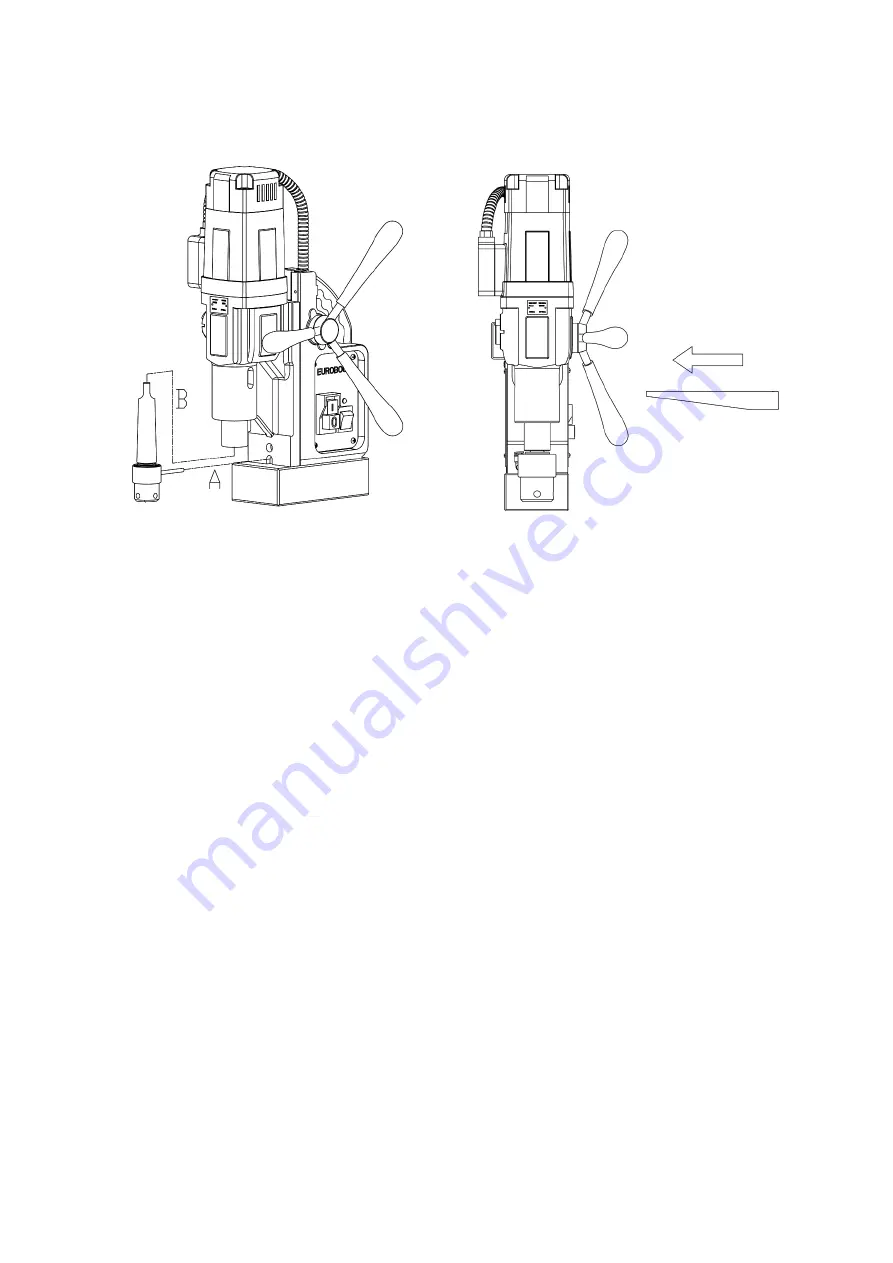
15
4.2 Morse taper spindle
[image 2-3]
[image 2-4]
1.
Make sure the inside of the output shaft and the Morse Taper spindle are clean and free of
grease
2.
Align the coolant ring rotation limiter with the recess in the gearbox (A)
3.
Firmly slide the Morse Taper spindle into the output shaft by hand (B). Make sure the spindle
is properly positioned. You should not be able to pull it out by hand.
4.
To remove the Morse Taper spindle
-
Switch of the motor
-
Rotate the mechanical gear switch to neutral (see chapter Gearbox)
-
Rotate the output shaft until the slots on the shaft align with the slots on the gearbox
-
Gently tap the supplied drift into the slots to push the Morse Taper arbor out