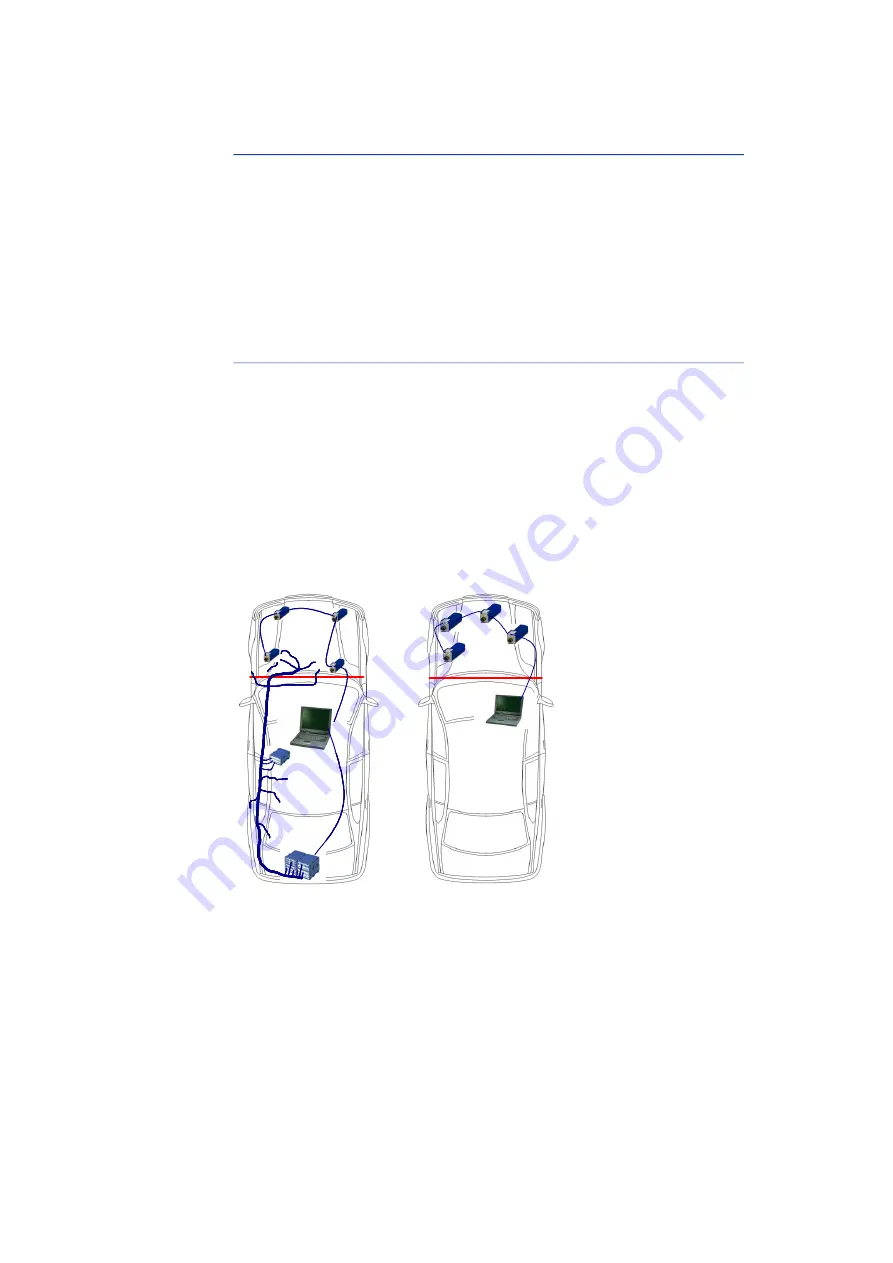
ETAS
ES400 Product Family
ES441.1 - User Guide
14
3
ES400 Product Family
This chapter contains information on the following topics:
• “Wiring Concepts in Test Vehicles” on page 14
• “Features of the ES400 Line” on page 15
• “Housing” on page 16
• “Ports” on page 17
• “LED” on page 18
3.1
Wiring Concepts in Test Vehicles
For the test phase, several hundred sensors must be installed in a test vehicle
in various areas, e.g. in the engine compartment and in the floor area. The sen
-
sors, which are positioned all over the vehicle, then have to be connected to the
measuring instruments of the test setup.
Today’s standard solutions with their central setup of measuring instruments
inside the vehicle require complex cabling to connect the widely distributed
sensors with the measuring instruments. Numerous, usually long connection
cables between the sensors and the measuring instruments, bundled together
to form several fat wiring harnesses, require a highly modified splash wall of
the test vehicle. This involves long setting-up times as well as high costs.
Fig. 3
-
1
Central and Decentral Sensor Cabling
With the ES400 modules, ETAS provides a decentral solution which consider
-
ably simplifies the test setup of the sensors.
The basic idea of this concept is to install the modules of the ES400 family as
close as possible to the sensors, to concatenate the modules with each other
and to connect just the first module of this chain with the laptop in the vehicle.
Sensor 1
Sensor 2
Sensor 3
Sensor n
Sensor 1
Sensor 2
Sensor 3
Sensor n
Sensor 1
Sensor 2
Sensor 3
Sensor n
Sensor 1
Sensor 2
Sensor 3
Sensor n
Sensor 1
Sensor 2
Sensor 3
Sensor n