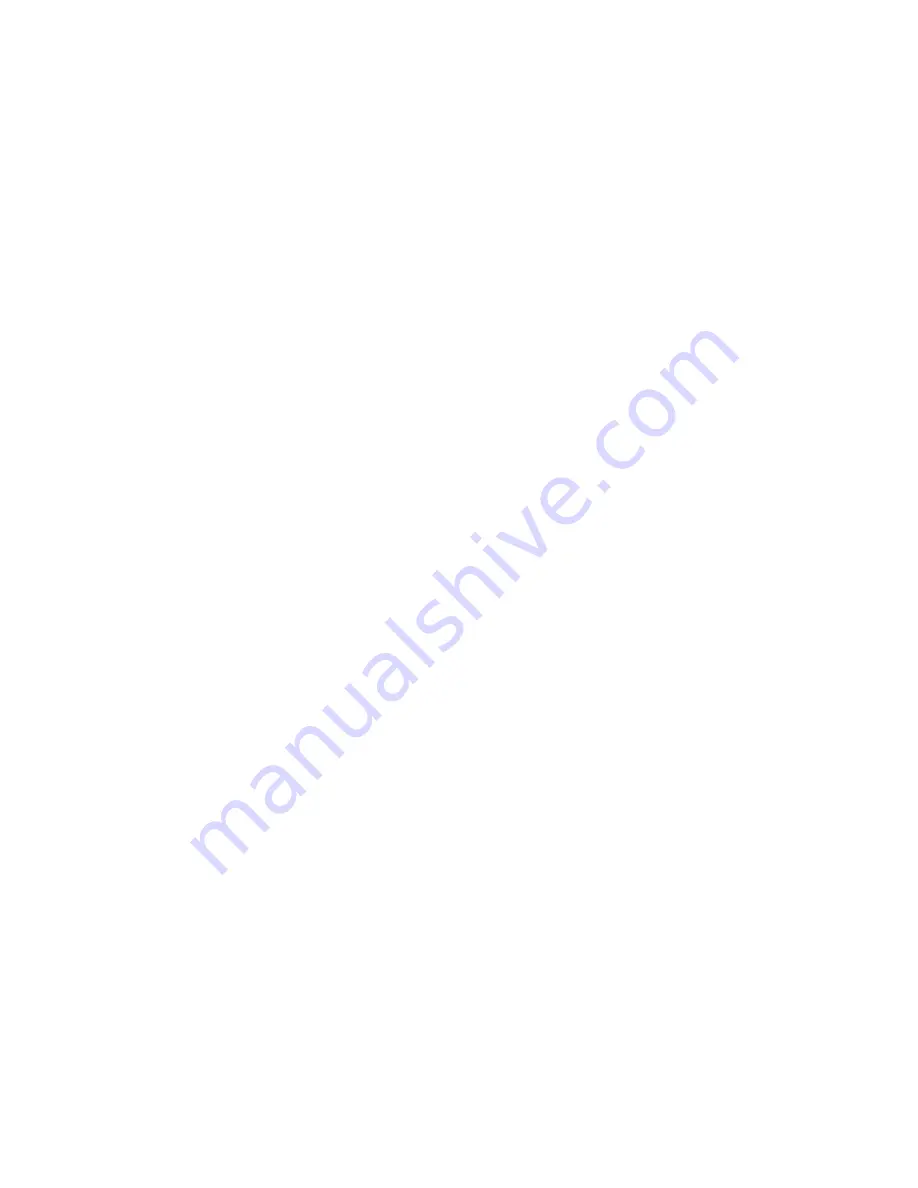
Model 1400 Shaft Drive service manual, SM1400KD3-AA Page 6
Eskridge, Inc. Olathe, Ks. 913-782-1238 www.eskridgeinc.com
4)
A gear puller may be used to remove the outer bearing cone
(20A)
from the shaft
(2)
. If reusing old bearing cone, do not pull
on or damage roller cage.
Note: Press bearing cone onto output shaft by pressing on in-
ner race only. DO NOT press on roller cage, as it may damage
the bearing assembly.
5)
Inspect inner and outer bearing cups
(20D & 20B)
. If cups are
damaged they must be replaced, drive them out using a brass
drift and utilizing the bearing knock-out notches in the base
(1)
Base Reassembly
1)
Clean all foreign material from magnetic oil plugs located In
base
(1)
.
2)
Place base exterior side up on work table.
3)
Apply a layer of lithium or general purpose bearing grease to
the roller contact surface of outer bearing cup
(20B)
.
4)
Press outer bearing cone
(20A)
onto the shaft until it seats
against the shoulder.
5)
Place the shaft
(2)
with the outer bearing cone into the base.
6)
Flip
shaft/base
assembly,
and
apply
lithium
or
general
purpose
bearing
grease
to
roller
con-
tact surface of the inner cup
(20D)
, then press
inner bearing cone
(20C)
onto shaft until it seats against inner
bearing cup.
7)
Prior to installation of the shaft seal the pre-
load may result in a rolling torque which varies be-
tween 200 to 300 in-lb. The bearing preload should be
tailored to your application; a low-speed application may re-
quire a high pre-load, while high-speed applications usually
benefit from low pre-load. Adding shims
(35A)
will increase the
pre-load on the bearing set. Determine your pre-load require-
ment and install shims to obtain this pre-load.
Install the support ring
(35B)
over the shims. Next, install the
retaining ring
(35C)
into the shaft groove.
8)
Lubricate shaft seal and reinstall seal carrier.
All subassembly service or repairs should be complete at
this time. Continue to Unit Assembly to complete buildup
of unit.
Unit Reassembly
1)
Install the Stage III carrier assembly onto the output shaft; align
the splines of the carrier
(5A)
with the output shaft splines and
slide the carrier onto the output shaft
(2)
.
2)
Install carrier retaining plate
(5L)
& secure using provided 3/8-
24 Flathead capscrews
(25A).
If using retaining compound to
assist in screw retention, apply only a small amount to internal
threads. Use of excess thread retaining compound may cause
screws to be irremovable once the compound has cured.
3)
Lubricate o-rings
(16C)
and install on the ring gear
(12B Stg II/,
12A Stg III)
pilots.
Caution: Use lifting device to prevent injury when handling ring
gears and other heavy components.
4)
Align gear teeth of Stage III ring gear
(12A)
with planet
gears
(5B)
and place on base, then align mounting holes
of ring gear with holes in base. Use the scribed line made
during disassembly for reference.
5)
Install Stage II ring gear
(12B)
with lubricated o-
ring in place. Align mounting holes of ring gear
with holes in base, using the scribed line made
during disassembly for reference.
6)
Install Stage III sun gear
(6),
then Stage II carrier assembly
(7)
,aligning gear teeth of ring gear with those of the planet
gears and carrier splines aligned with those on the Stage
III sun gear
(6)
.
7)
Install Stage II sun gear
(4)
, and stage II carrier thrust-
washers
(14A, 14B)
.
8)
Install o-ring (
16C
) to ring adapter cover
(3)
and install
adapter cover to Stage II ring gear, aligning mounting holes
of cover with those in ring gears. Use the scribed line made
during disassembly for reference.
9)
Install, and torque the twenty 3/4-10 capscrews
(25C)
to
retain adapter cover.
10) Install o-ring on Stage I ring gear
(62)
and install ring gear
to adapter cover, aligning mounting holes of ring with
those in the adapter cover. Use the scribed line made
during disassembly for reference.
11) Install the Stage I carrier assembly with adapter shaft
(52)
into the Stage I ring gear
(62)
.
12) Install the input gear
(54)
.and thrust bearing set
(64A,
64B)
Refer to exploded view for details..
13) Noting the scribed line made during disassembly, (with
lubricated o-ring in place) align and install the top cover
(53)
.
14) Install
and
torque
the
twenty
5/8-11
hex-
head
cap-screws
(75B)
with
lockwash-
ers, retaining the top cover. The torque for the
cap-screws: 220 ft-lb dry, 170 ft-lb if the fasteners are lu-
bricated.
15) Install and torque the twenty 3/4-10 capscrews
(25C)
w/
lockwashers
(26D)
. The torque for the capscrews is 380
ft.-lbs. dry or 280 ft.-lbs. lubricated
16) Using a splined shaft to drive the input gear
(54)
ensure
that the unit spins freely.
17) Fill the unit to the proper level, as specified, with recom-
mended gear oil (refer to chart, page 3) after unit is sealed
with brake and/or motor.
The gear drive is now ready to use.