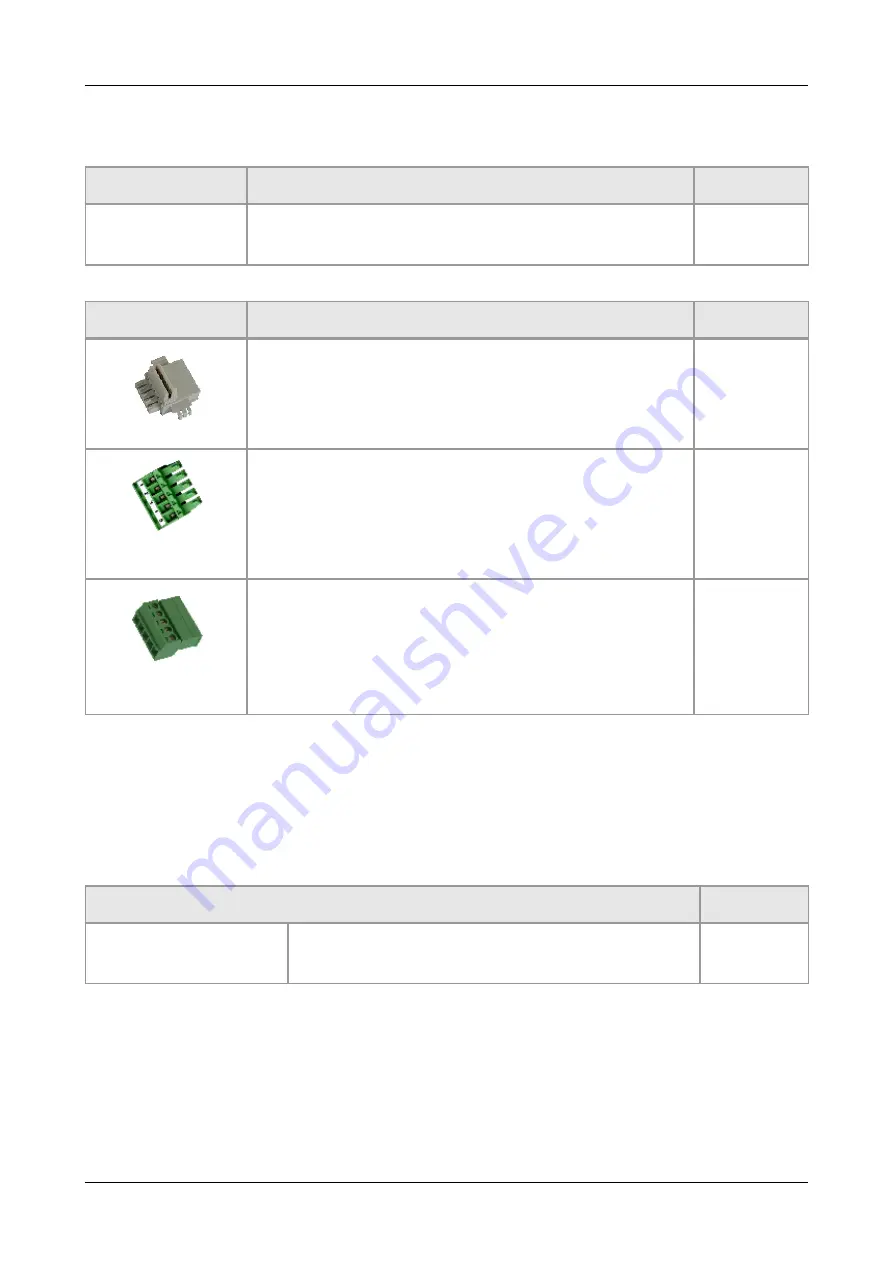
Order Information
10. Order Information
Type
Properties
Order No.
CAN-PN
PROFINET IO / CAN Gateway,
CAN 2.0A/B (11/29-Bit CAN-ID), GSD file
C.2920.02
Accessories
Order No.
CAN-CBX-TBUS
Mounting-rail bus connector of the CBX-InRailBus for CAN-
CBX modules
C.3000.01
CAN-CBX-TBUS-
Connector
Terminal plug of the CBX-InRailBus for the connection of
the +24V power supply voltage and the CAN interface
Female type
C.3000.02
CAN-CBX-TBUS-
Connection adapter
Terninal plug of the CBX-InRailBus for the connection of the
+24V power supply voltage and the CAN-Interface
Male type
C.3000.03
Table 9:
Order information
PDF Manuals
Manuals are available in English and usually in German as well. For availability of English manuals
see table below.
Please download the manuals as PDF documents from our esd website
Manuals
Order No.
CAN-PN-ME
CAN-PN Manual in English
(Hardware and Software Manual)
C.2920.21
Table 10:
Available manuals
Printed Manuals
If you need a printout of the manual additionally, please contact our sales team:
a quotation. Printed manuals may be ordered for a fee.
Page 38 of 38
Hardware Manual • Doc. No.: C.2920.21 / Rev. 1.4
CAN-PN