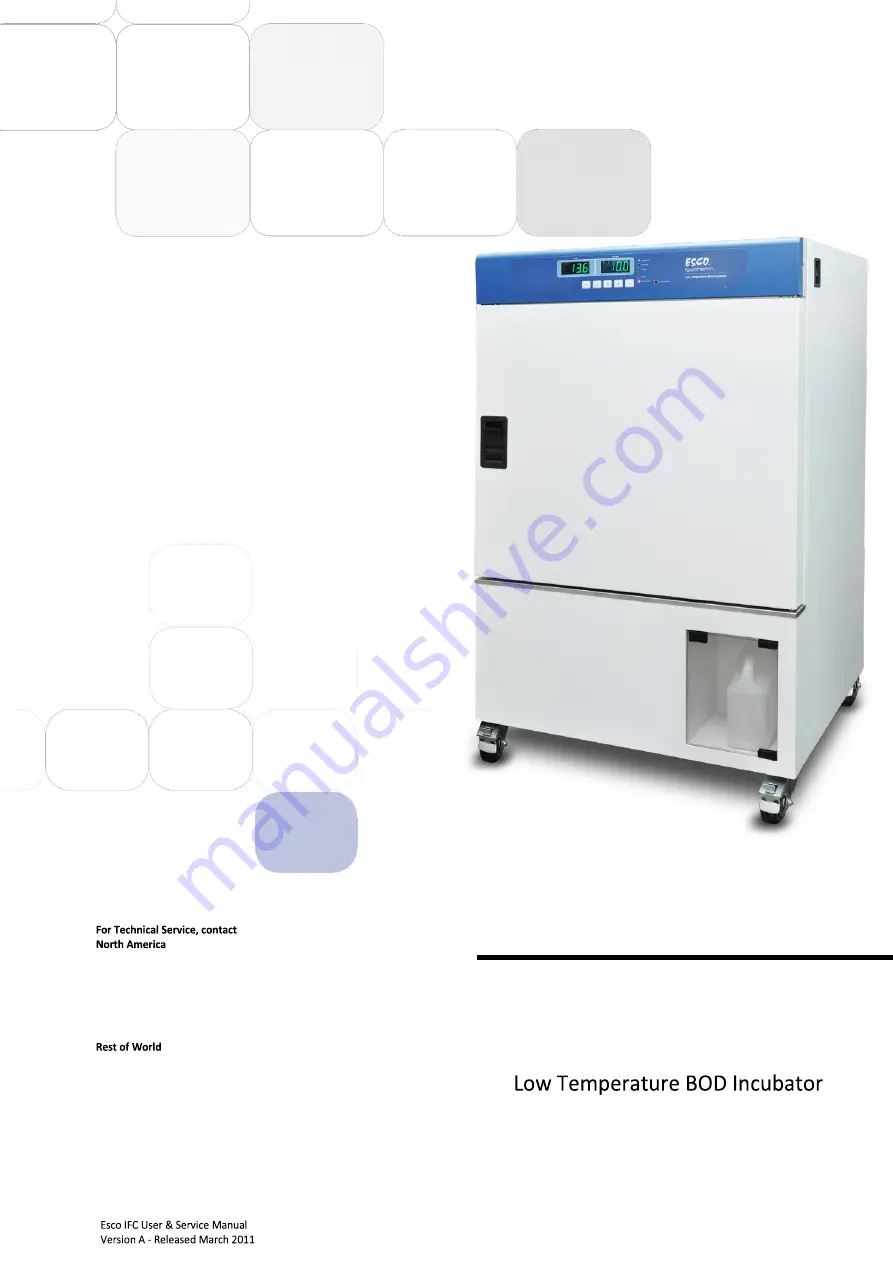
Isotherm
User
Manual
Thank you for purchasing this Esco Low Temperature BOD
Incubator. Please read this manual thoroughly to familiarize
yourself with the many unique features and exciting
innovations we have built into your new equipment. Esco
provides many other resources at our website,
www.escoglobal.com, to complement this manual and help you
enjoy many years of productive and safe use of your Esco
products.
Esco Technologies, Inc.
2940 Turnpike Drive, Units 15-16 • Hatboro, PA 19040, USA
Toll-Free USA and Canada 888-375-ESCO
Tel 215-441-9661 • Fax 215-441-9660
us.escoglobal.com • [email protected]
Esco Micro Pte. Ltd.
21 Changi South Street 1 • Singapore 486 777
Tel +65 6542 0833 • Fax +65 6542 6920
www.escoglobal.com • [email protected]
Summary of Contents for Isotherm IFC-110-8
Page 8: ...vi Isotherm ...
Page 10: ...viii Isotherm ...
Page 14: ...4 Isotherm ...
Page 26: ...16 Isotherm ...
Page 29: ...APPENDIX ...
Page 30: ......
Page 32: ......