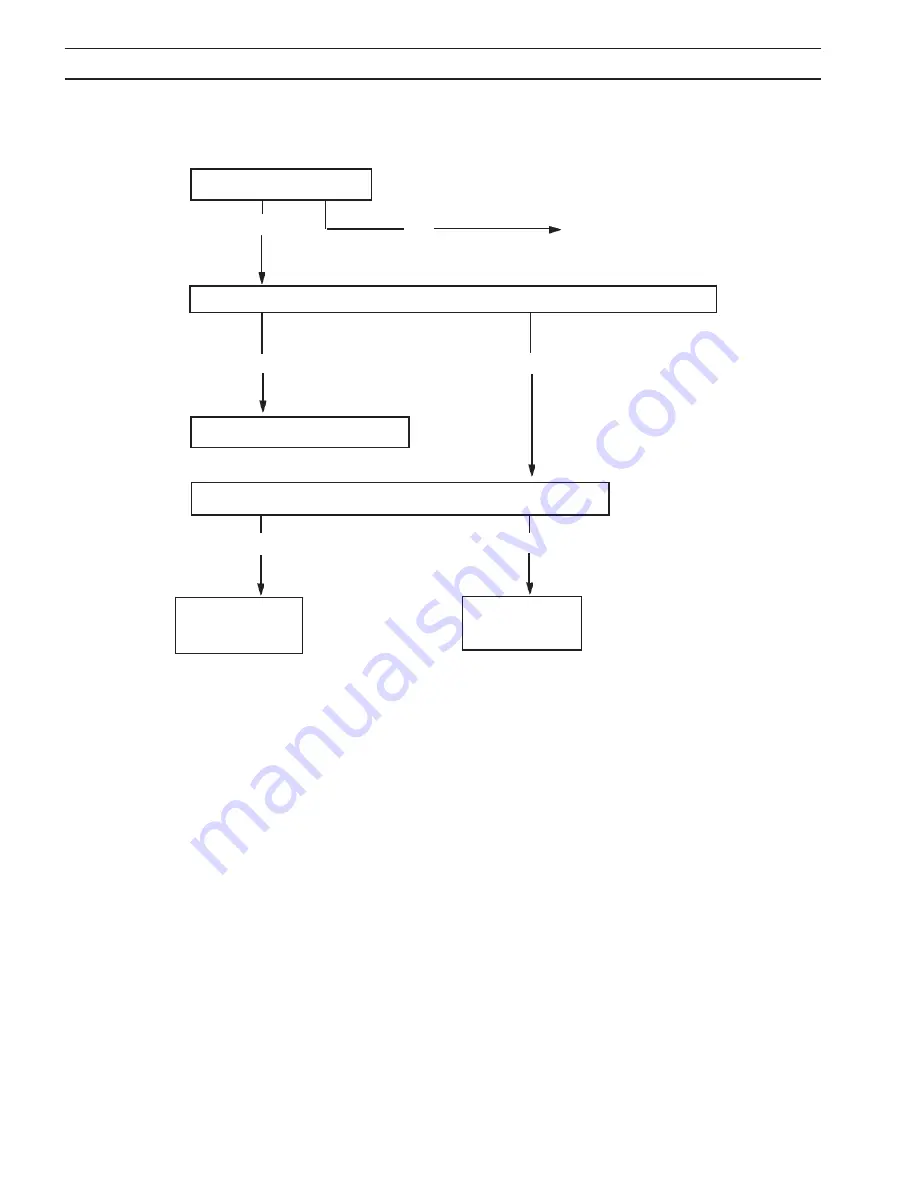
24
c. air does not shut off
Is air check switch OFF?
Yes
No
Turn switch OFF
Does arc start when nozzle contacts work without depressing torch switch?
Yes
No
Check for short in torch switch
Does air flow even when Powercut 650 power switch is OFF?
Yes
No
Replace
Repair power
solenoid valve
source
figure 5-3. sequence of operations
section 5
maintenance
Summary of Contents for Powercut 650
Page 4: ...4 table of contents...
Page 14: ...14 section 3 installation...
Page 20: ...20 section 4 operation...
Page 32: ...32 section 6 replacement parts...
Page 33: ...33 section 6 replacement parts...
Page 34: ...34 section 6 replacement parts...
Page 35: ...35 section 6 replacement parts...
Page 36: ...36 section 6 replacement parts...
Page 37: ...37 section 6 replacement parts...
Page 38: ...Q1 section 6 replacement parts...
Page 39: ...39 section 6 replacement parts...
Page 40: ...40 section 6 replacement parts...
Page 41: ...41 section 6 replacement parts...
Page 42: ...42 notes...
Page 45: ......
Page 46: ......
Page 47: ......
Page 48: ......
Page 49: ......
Page 50: ......
Page 51: ......
Page 52: ......
Page 53: ......
Page 54: ......
Page 55: ......
Page 56: ......