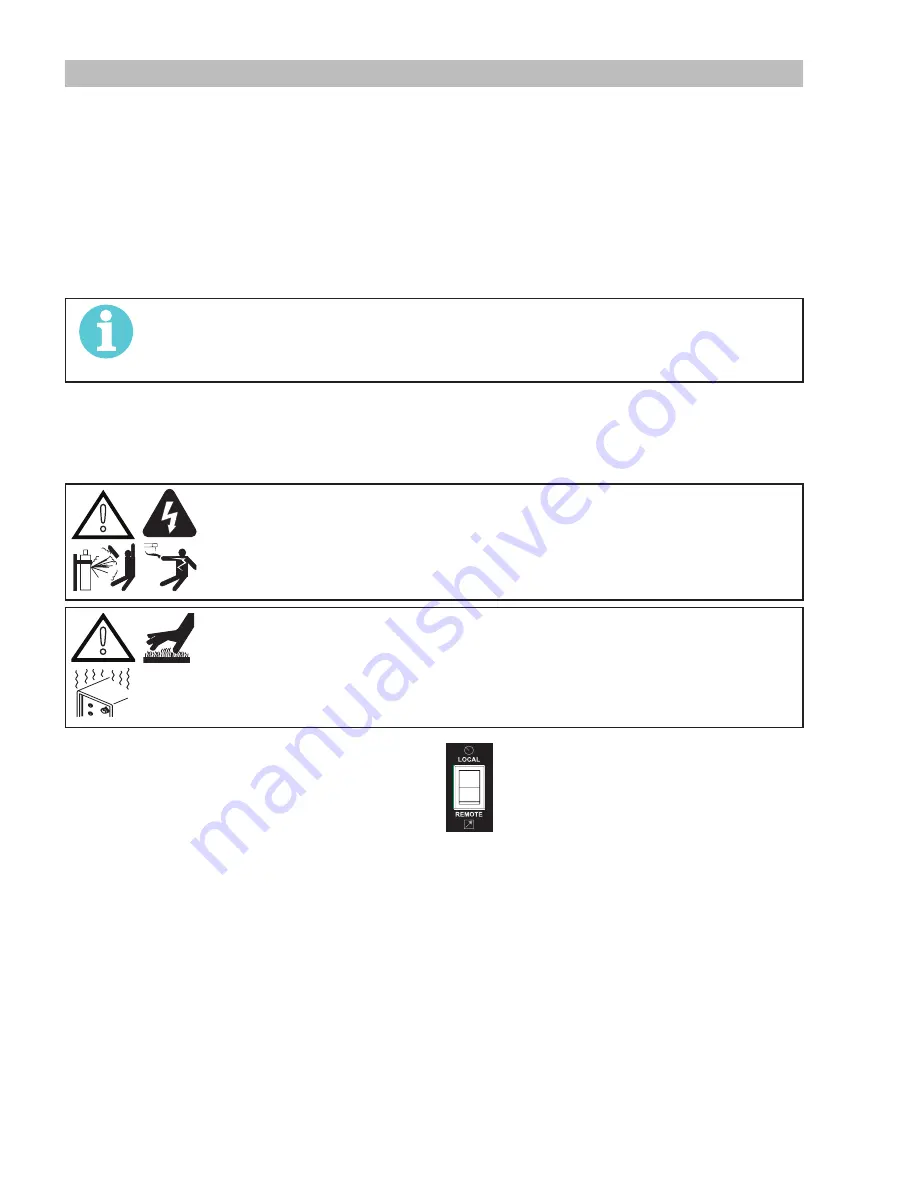
ESAB FABRICATOR 211i
INSTALLATION/SETUP 4-18 Manual 0-5450
4.13 Setup For LIFT TIG (GTAW) Welding
A. Select LIFT TIG mode with the process selection control (refer to Section 4.01.13 for further information).
B. Connect the TIG Torch to the negative welding terminal (-). Welding current flows from the power source via heavy duty
bayonet type terminals. It is essential, however, that the male plug is inserted and turned securely to achieve a sound elec-
trical connection.
C. Connect the work lead to the positive welding terminal (+). Welding current flows from the Power Source via heavy duty
bayonet type terminals. It is essential, however, that the male plug is inserted and turned securely to achieve a sound elec-
trical connection.
D. Connect the TIG torch trigger switch via the 8 pin socket located on the front of the power source as shown below. The TIG
torch will require a trigger switch to operate in LIFT TIG Mode.
NOTE!
A ESAB 26V TIG torch with an 8 pin plug must be used to turn the weld current on/off via the TIG torch
trigger switch to TIG weld OR a ESAB Foot Control with an 8 pin plug must be used to turn the weld cur-
rent on/off as well as providing remote control of the weld current.
E. Fit the welding grade shielding gas regulator/flowmeter to the shielding gas cylinder (refer to Section 3.08) then connect
the shielding gas hose from the TIG torch to the regulator/flowmeter outlet. Note that the TIG torch shielding gas hose is
connected directly to the regulator/flowmeter. The power source is not fitted with a shielding gas solenoid to control the
gas flow in LIFT TIG mode therefore the TIG torch will require a gas valve.
!
WARNING
Before connecting the work clamp to the work and inserting the electrode in the TIG Torch
make sure the Electricity Supply is switched off.
Secure the welding grade shielding gas cylinder in an upright position by chaining it to a sta-
tionary support to prevent falling or tipping.
!
CAUTION
Remove any packaging material prior to use. Do not block the air vents at the front or rear of
the Welding Power Source.
Loose welding terminal connections can cause overheating and result in the male plug being
fused in the terminal.
F. Switch the LOCAL/REMOTE switch inside the
wire feed compartment to LOCAL to use the
Power Sources Amperage control or REMOTE
for remote amperage using a Foot Control.