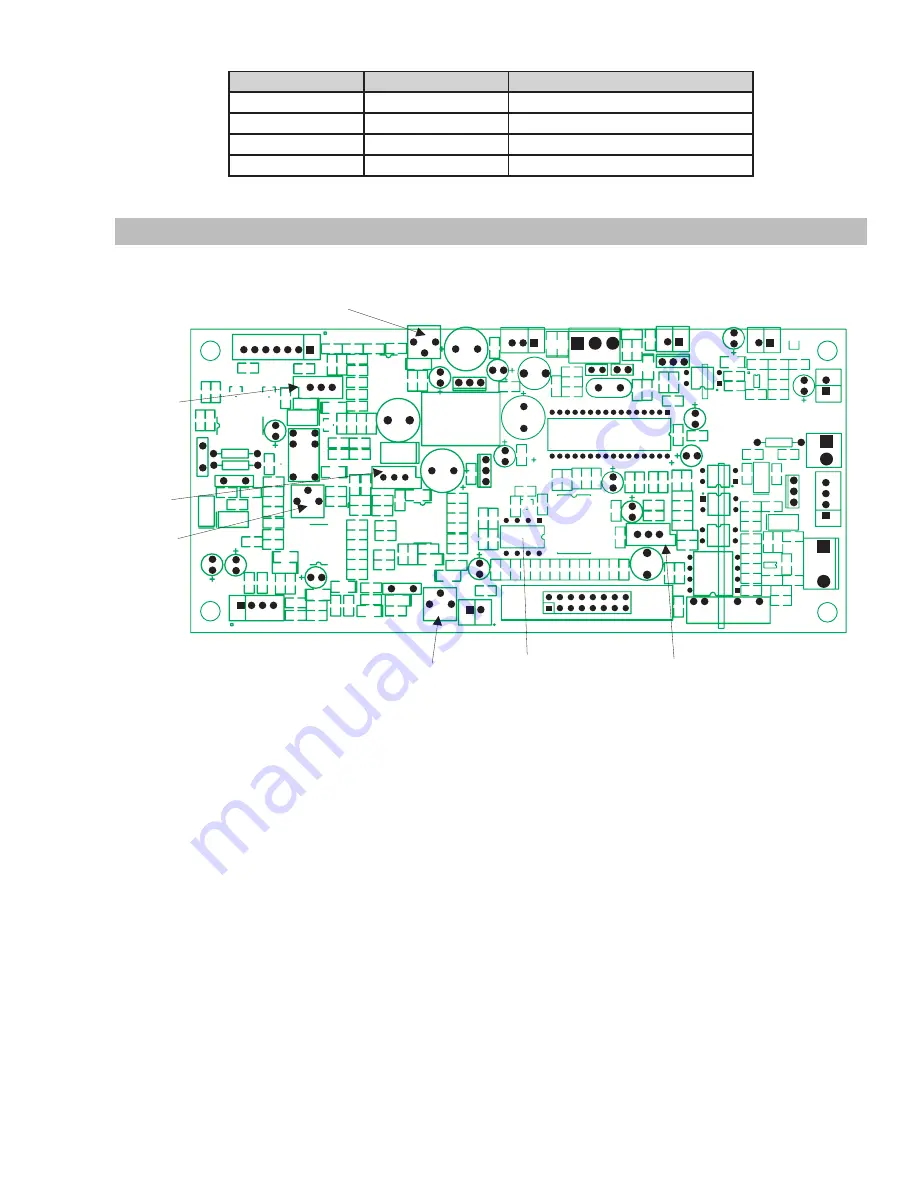
ESAB FABRICATOR 181i
Manual 0-5449 6-15 TROUBLESHOOTING
SW0 position
Normal
Calibration
1
OFF
Set to ON for Fabricator 181i
2
OFF
Set to ON for Fabricator 181i
3
OFF
Set to ON for Fabricator 181i
4
OFF
OFF
Table 6-36 SW0 Dip Switch functions
6.14 Calibration
1 Calibration
Imin
Vmin
Imax
W2
WVF
A
SW0
A-09994
Set SW0-1 to ON, SW0-1 to ON, SW0-3 to ON, SW0-4 to OFF to allow calibration of output volts & amps, and calibration of wire feed
speed.
2
Output Current Calibration
Select STICK mode on the front panel.
Measure no load output welding voltage and adjust WVF potentiometer so Volts display reads within 0.2V of the measured value.
Connect a load to the output terminals. The load should be of a resistance to give 25V at 250A.
Set front panel AMPS potentiometer to minimum.
Adjust Imin trimpot until output amps is 10A +/- 0.2A
Set front panel AMPS potentiometer to maximum.
Adjust Imin trimpot until output amps is 175A +/- 1A
Recheck settings
Set front panel AMPS potentiometer to maximum.
Adjust A potentiometer so Amps display reads within 0.5A of the measured value.
3
Output Voltage Calibration
Select MIG mode on the front panel.
Remove the load from the output terminals.
Set front panel VOLTS potentiometer to minimum.
Adjust Vmin trimpot until output volts is 14.0V +/- 0.2V
Set front panel VOLTS potentiometer to maximum.
Adjust W2 trimpot until output volts is 25V +/- 0.2V
Recheck settings
Summary of Contents for Fabricator 181i
Page 18: ...ESAB FABRICATOR 181i SAFETY AND INSTALLATION 3 8 Manual 0 5449 This Page Intentionally Blank...
Page 40: ...ESAB FABRICATOR 181i THEORY OF OPERATION 5 2 Manual 0 5449 This Page Intentionally Blank...
Page 64: ...ESAB FABRICATOR 181i DISASSEMBLY PROCEDURES 7 4 Manual 0 5449 A 09965_AB...
Page 71: ...ESAB FABRICATOR 181i Manual 0 5449 8 3 ASSEMBLY PROCEDURES 8 7 A 10011 9 A 10114...
Page 73: ...ESAB FABRICATOR 181i Manual 0 5449 8 5 ASSEMBLY PROCEDURES A 09965_AB...
Page 76: ...ESAB FABRICATOR 181i ASSEMBLY PROCEDURES 8 8 Manual 0 5449 This Page Intentionally Blank...
Page 82: ...REVISION HISTORY Date Rev Description 09 18 2015 AA Manual release...
Page 83: ......