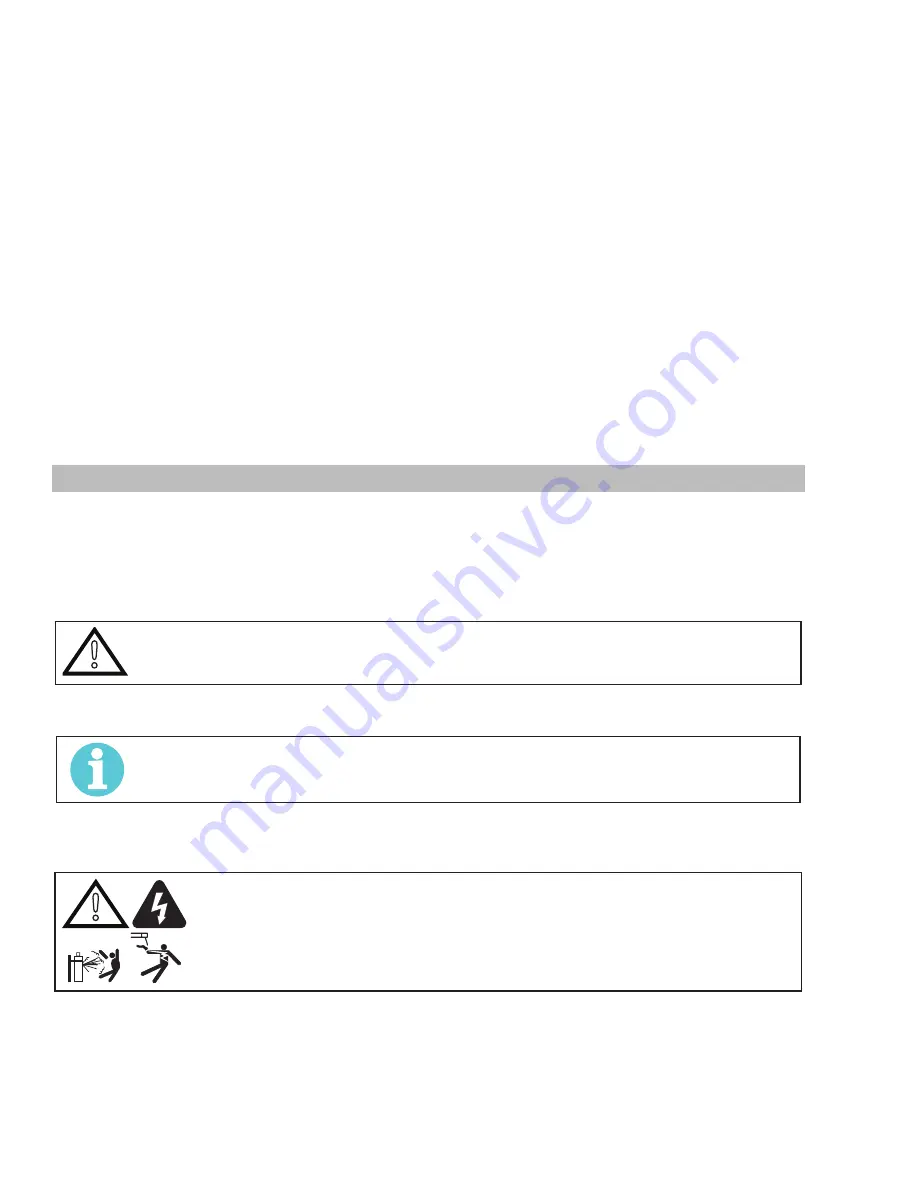
ET 220I AC/DC
INSTALLATION, OPERATION AND SETUP
Manual 0-5346
3-10
48. Crater Current time indicator light
This light will illuminate when the Crater Current Time Welding Parameter is selected.
49. Electrode Diameter Out-of-Range indicator light
This light will illuminate when the set welding current is outside the normal operating range for the selected Electrode Diameter.
50. Post Flow indicator light
This light will illuminate when the Post Flow Welding Parameter is selected.
51. Gas Purge Button
Press the button once to active that gas valve and then press it again to turn it off, also if you press and release this button the gas
will purge for 30 seconds and then turn off.
52. Tip Tronic indicator light (Refer to Section 3.13)
This light will illuminate when an active TipTronic job is selected.
53. Save Tip Tronic Job Button
Press the SAVE button to save the current TipTronic Job settings in the selected memory location
Up to 100 jobs can be saved arranged as 10 banks of 10 jobs.
3.09 Setup for TIG (GTAW) Welding
A. Select a GTAW operation mode with the welding mode & welding type buttons (refer to Section 3.10 for further information).
B. Connect the TIG Torch to the Electrode welding terminal (top). Welding current flows from the power source via Dinse type
terminals. It is essential, however, that the male plug is inserted and turned securely to achieve a sound electrical connection.
C. Connect the work lead to the Worklead welding terminal (bottom). Welding current flows from the Power Source via Dinse type
terminals. It is essential, however, that the male plug is inserted and turned securely to achieve a sound electrical connection.
!
CAUTION
Loose welding terminal connections can cause overheating and result in the male plug being fused in the
Dinse terminal.
D. Connect the TIG torch trigger switch via the 8 pin socket located on the front of the power source as shown below. The TIG
torch will require a trigger switch to operate in Liftarc TIG or HF TIG Mode.
NOTE!
If the TIG torch has a remote TIG torch current control fitted then it will require to be connected to the 8 pin
socket. (Refer to section 3.08 Remote Control Socket for further information).
E. Fit the welding grade shielding gas regulator/flowmeter to the shielding gas cylinder (refer to Section 3.19) then connect the
shielding gas hose from the regulator/flowmeter outlet gas INLET on the rear of the Power Source. Connect the gas hose from
the TIG torch to the gas OUTLET on the front of the Power Source.
!
WARNING
Before connecting the work clamp to the work make sure the mains power supply is switched off.
Secure the welding grade shielding gas cylinder in an upright position by chaining it to a suitable
stationary support to prevent falling or tipping.