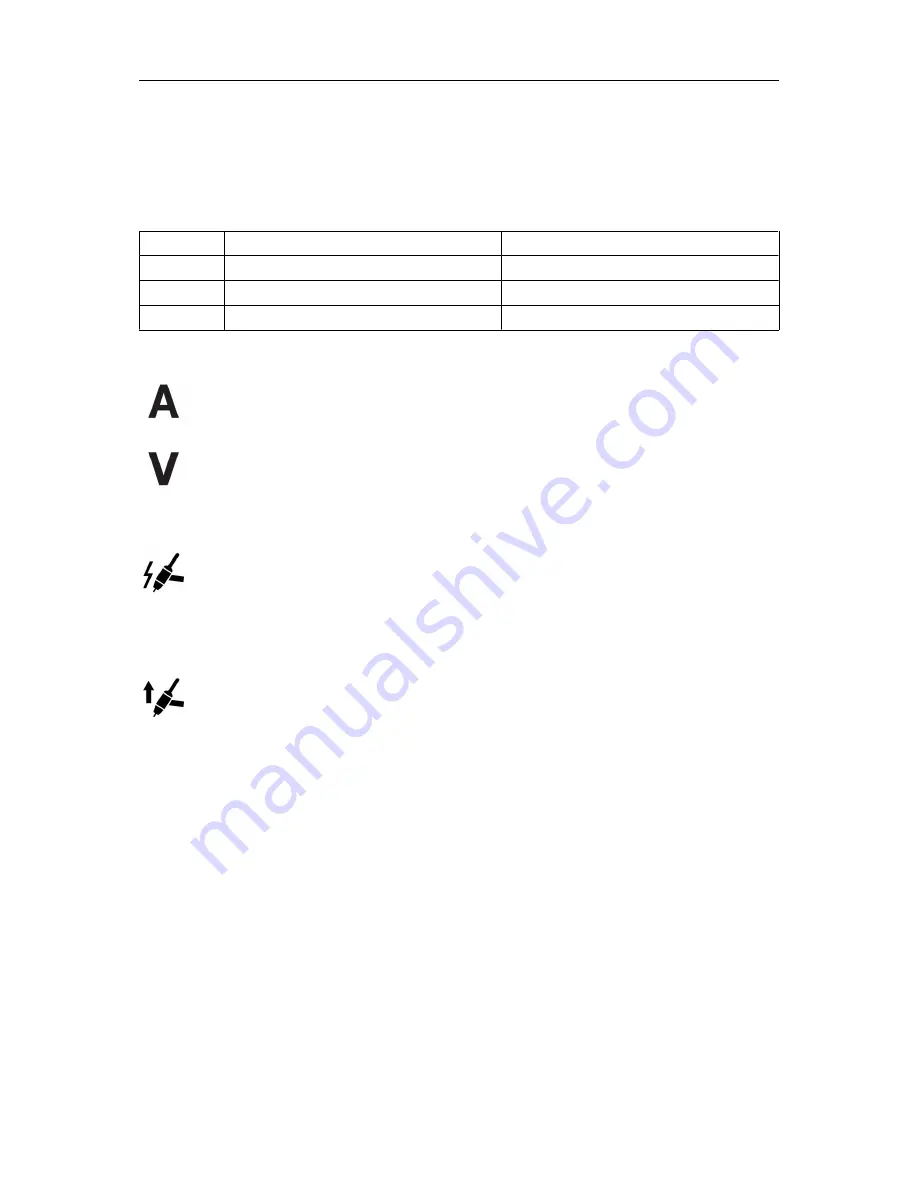
6 CONTROL PANEL
0463 416 001
- 26 -
© ESAB AB 2017
6.3.1
Hidden TIG functions
There are hidden functions in the control panel. To access the functions, press parameter
selection button for 3 seconds (see section SETTING PANEL for button placement). The
display shows a letter and a value. Select function by pressing the same button. The knob is
used to change the value of the selected function. To exit hidden functions, press the button
for 3 seconds again.
Letter
Function
Settings
A
Gas pre flow
0.0–9.9 s
b
Slope up
0.0–9.9 s
I
Remote min current
0–99%
6.3.2
Measured values
Measured current
Measured value in the display for welding current A is arithmetic average value.
Measured voltage
Measured value in the display for arc voltage V is arithmetic average value.
6.4
TIG functions explanation
HF start
The HF start function initiates the arc by using a high frequency voltage pilot arc.
This will reduce the risk of tungsten contamination in the starts. The high
frequency voltage might disturb other electrical equipment in the surrounding
area.
LiftArc™
The LiftArc™ function initiates the arc when the tungsten electrode is brought
into contact with the workpiece, the trigger switch is pressed, and the tungsten
electrode is lifted away from the workpiece. In order to minimize the risk of
tungsten contaminations the start current is very low and will slope up to the set
current (controlled by the slope up function).
Summary of Contents for ES 300i
Page 2: ......