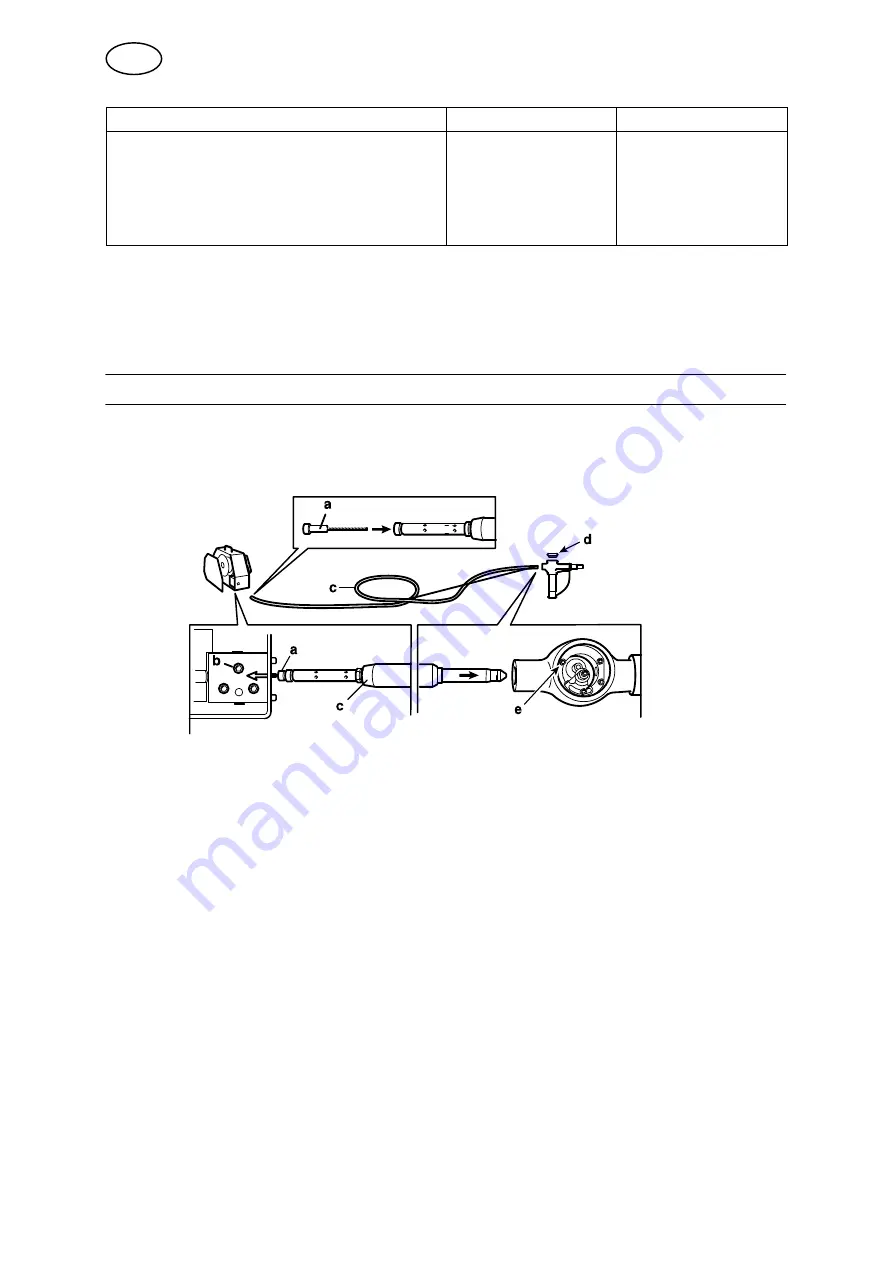
© ESAB AB 1999
- 6 -
bg03d1ea
Welding hose
A9-250
A9-400
Permissible load at 60% duty cycle
Length: 5 m, 10 m, 16 m
250 A
400 A
Electrode diameter
0.8-1.2 mm
0.8-1.6 mm
Working pressure
490 kPa (5 kp/cm
2
)
490 kPa (5 kp/cm
2
)
Max. testing pressure
735 kPa (5 kp/cm
2
)
735 kPa (5 kp/cm
2
)
NB.
Make sure the gun motor has the proper working pressure, 490 kPa (5 kp/cm
2
).
If the pressure is lower the motor will not get the right speed, resulting in too low wire
feed speed and welding current. If the pressure is higher the welding hose will be
exposed to harmful dynamic pressure.
4
INSTALLATION
The installation must be carried out by a professional.
4.1
Connecting the welding hose
S
Press the inlet nozzle (
a
), - selected according to the diameter of the wire - into
the welding hose.
S
Open the wire feed unit on the bobbin side.
S
Undo the locking screw (
b
) on the connecting plate.
S
Connect the welding hose (
c
) to the wire feed unit and tighten the locking screw
on the connecting plate.
S
Remove the plastic cover (
d
) from the gun housing.
S
Undo the locking screw (
e
) and press the other end of the hose into the gun.
S
Tighten the locking screw and fit the plastic cover.
GB