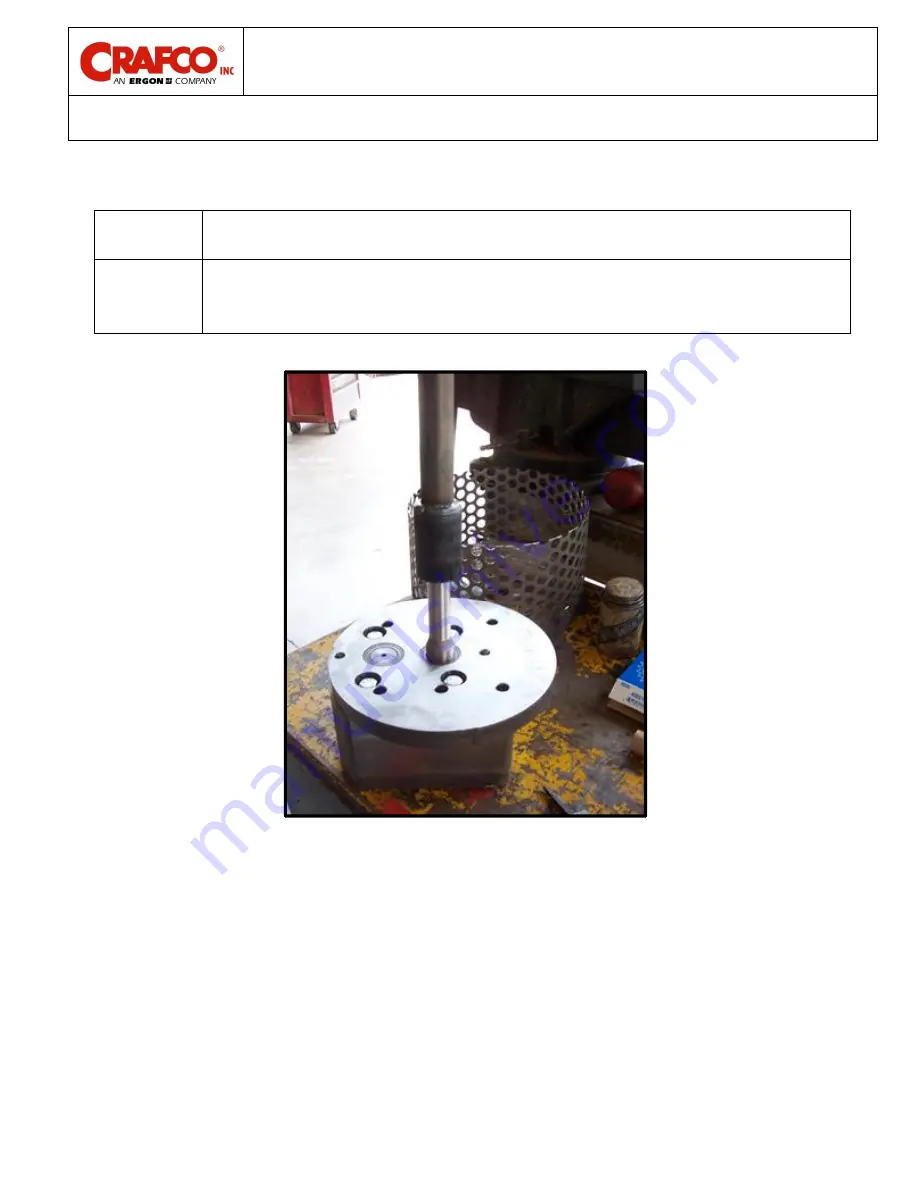
Super Shot 125 DC 70CFM EU Part Manual
Chapter 6 Maintenance Instructions
©2022 by Crafco, Inc. All Rights Reserved
………………..………………………………..….…Maintenance Instructions 6-15
Table 6-15 Material Pump Replacement (continued)
Step
Action
18
Make sure that the pump shaft coupling fits correctly onto the new material pump
before mounting the material pump inside the tank. Also make sure the pump spins
freely.
Fig. 6-8 Pump Drive Shaft Dry Fit to Material Pump
Summary of Contents for Crafco SUPER SHOT 125
Page 1: ...Parts Manual 26635N Revision E SUPER SHOT 125 DIESEL COMPRESSOR 70CFM EU MELTER...
Page 4: ...Super Shot 125 Diesel Compressor 70 CFM EU Melter PN 48300N...
Page 5: ......
Page 16: ......
Page 26: ......
Page 42: ......
Page 72: ......
Page 76: ......
Page 120: ......
Page 170: ......
Page 174: ......
Page 175: ......
Page 176: ...2022 Crafco Inc...