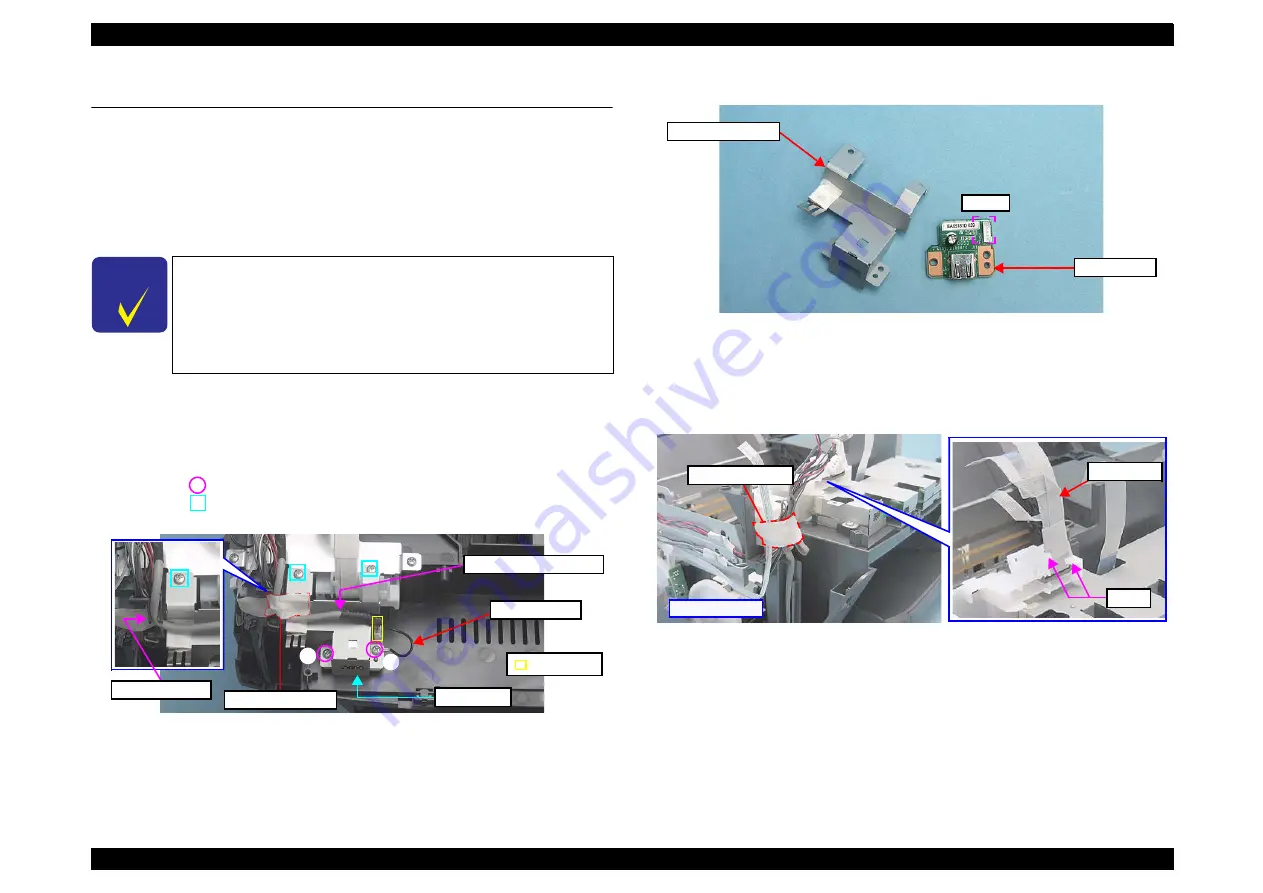
EPSON Stylus Photo R260/R265/R270, R360/R380/R390
Revision B
Disassembly/Assembly
Removing Control Boards
76
4.3 Removing Control Boards
4.3.1 Removing the USB Board (R260/R265/R270 only)
Parts/Components need to be removed in advance
All exterior parts/components
USB Board removal
1.
Remove the piece of acetate tape and remove the USB connector cable from
the cable retainer.
2.
Disconnect the USB cable from the connector.
3.
Remove the screw and remove the GND cable.
4.
Remove the three screws.
•
Screw
: C.B.P. M3x10 (tightening torque: 5-7 kgf.cm)
•
Screw
: C.B.S. M3x6 (tightening torque: 5-7 kgf.cm)
(The numbers shown in the figure indicate the order of tightening the screws.)
Figure 4-44. Removing the USB Board
5.
Remove the USB Shield Plate and the USB Board.
Figure 4-45. Disassembling the USB Board
FFC Holder removal
1.
Peel off the acetate tape, and disengage all the cables and Ferrite Core from
the FFC Holder.
2.
Release the Head FFC from the two tabs of the FFC Holder.
Figure 4-46. Removing the Cables
C H E C K
P O I N T
R260/R265/R270 are equipped with a USB Board. Remove the
USB Board before removing the Main Board. Refer to
R265/R270 & R360/R380/R390 Disassembly Flowchart(p.64)
Refer to the Orientation Definition below for the directions
indicated in the following procedures.
•
“4.1.6 Orientation Definition (p.61)”
1
3
4
USB Board
Acetate tape
2
2
Cable Retainer
GND Cable
USB Connector Cable
: Connector
CN1
USB Shield Plate
USB Board
[Left front side]
Acetate tape
Head FFC
Tab
Summary of Contents for R380 - Stylus Photo Color Inkjet Printer
Page 1: ...EPSONStylusPhotoR260 R265 R270 R360 R380 R390 Color Inkjet Printer SEIJ06001 SERVICE MANUAL ...
Page 7: ...C H A P T E R 1 PRODUCTDESCRIPTION ...
Page 22: ...C H A P T E R 2 OPERATINGPRINCIPLES ...
Page 30: ...C H A P T E R 3 TROUBLESHOOTING ...
Page 55: ...C H A P T E R 4 DISASSEMBLY ASSEMBLY ...
Page 111: ...C H A P T E R 5 ADJUSTMENT ...
Page 128: ...C H A P T E R 6 MAINTENANCE ...
Page 136: ...C H A P T E R 7 APPENDIX ...
Page 138: ...Model PM D870 Stylus Photo R360 R380 R390 Board C658 MAIN Sheet 1 4 ...
Page 139: ...Model PM D870 Stylus Photo R360 R380 R390 Board C658 MAIN Rev C Sheet 2 4 ...
Page 140: ...Model PM D870 Stylus Photo R360 R380 R390 Board C658 MAIN Rev B Sheet 3 4 ...
Page 141: ...Model PM D870 Stylus Photo R360 R380 R390 Board C658 MAIN Rev A Sheet 4 4 ...
Page 142: ...Model PM D870 Stylus Photo R360 R380 R390 Board C658 PNL Rev A Sheet 1 1 ...
Page 143: ...Model PM D870 Stylus Photo R360 R380 R390 Board C658 PNL B Rev A Sheet 1 1 ...
Page 144: ...Model PM D870 Stylus Photo R360 R380 R390 Board C658 STG Rev B Sheet 1 1 ...
Page 145: ...Model PM G850 Stylus Photo R260 R265 R270 Board C653 MAIN Rev C Sheet 1 1 ...
Page 146: ...Model PM G850 Stylus Photo R260 R265 R270 Board C653 PNL Rev A Sheet 1 1 ...
Page 147: ...Model PM G850 Stylus Photo R260 R265 R270 Board C653 I F Rev A Sheet 1 1 ...