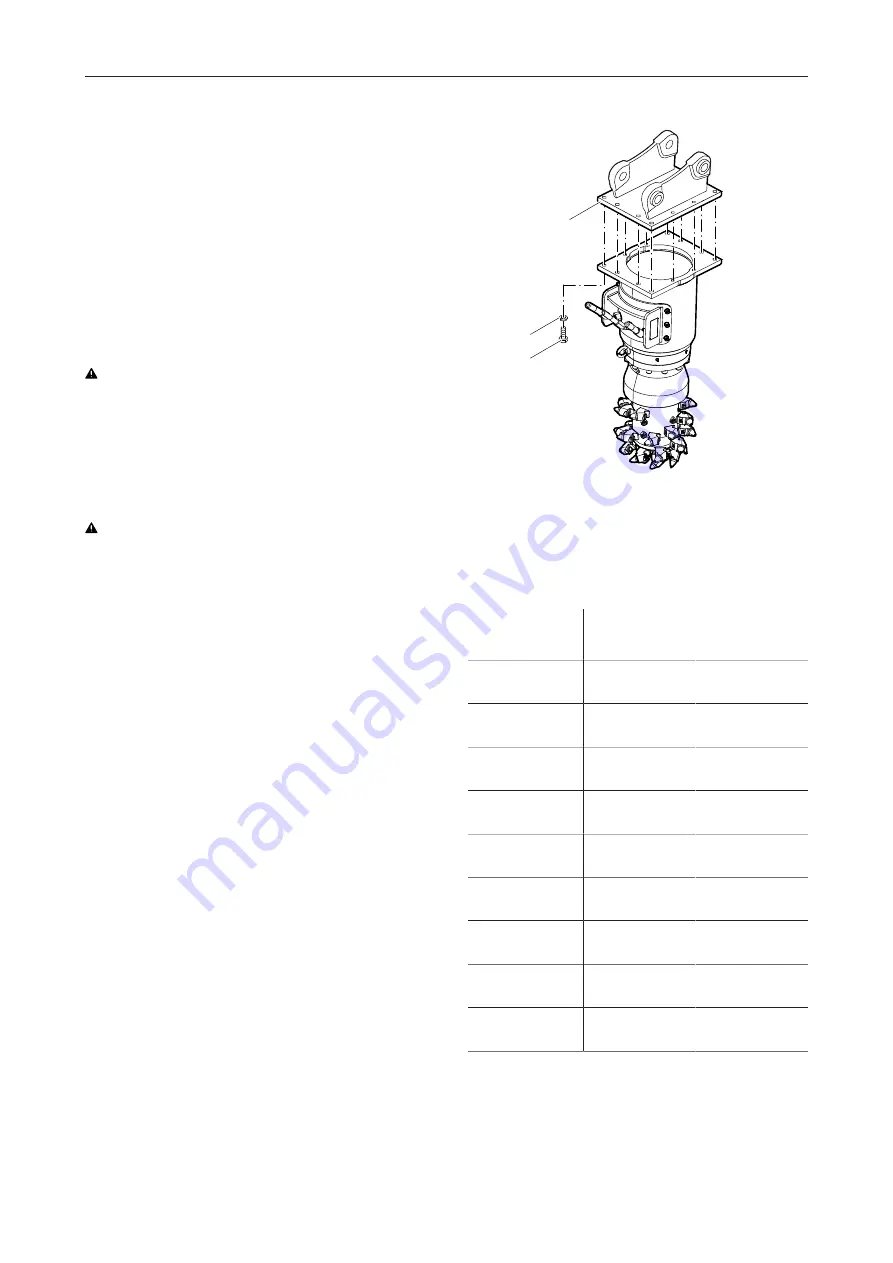
Safety and operating instructions
© Anbaufräsen PC GmbH | 3390 5221 01 | 2020-09-07
Original Instructions
27
5.4 Attaching the hydraulic
attachment to the carrier
5.4.1 Mechanical mounting aspects
You need an assistant to attach the hydraulic attachment
to the carrier.
n
Agree on hand signals with your assistant, to enable
him to help you placing the carrier in the proper posi-
tion to attach the hydraulic attachment.
WARNING
Injury by impacts
A sudden movement of the carrier may cause your as-
sistant to be hit and injured by the boom or the hydraulic
attachment.
u
Only move the boom very slowly and in a controlled
manner while an assistant is within the danger zone.
u
Always keep sight of your assistant.
WARNING
Hands and fingers being cut off or hurt
Bores and surfaces can act like a pair of scissors and
cut off or hurt parts of your body.
u
Never use your fingers to check bores or fitting sur-
faces.
NOTICE
The adapter plate can come loose
The adapter plate can come loose if the fastening
screws are not designed for local high loads.
u
Only use the Allen screws of strength category 8.8
and the pairs of lock washers included in the delivery
to attach the adapter plate or the base plate.
n
Place the drum cutter on the assembly stand within
the range of the carrier.
n
Apply Anti-Seize to the Allen screw threads (A) be-
fore inserting them.
The contact faces of the screw head and the lock
washers (B) must not be lubricated.
n
Align the adapter plate (C) with the drum cutter as
shown.
A
B
C
n
Fit a pair of lock washers (B) onto every screw.
n
Tighten the Allen screws (A) with an Allen key.
n
Tighten the Allen screws (A) with the required tight-
ening torque.
Type
Key size
Tightening
torque
ER 100 L
17 mm (0.67 in.)
390 Nm
(288 ft lbs)
ER 250 L
17 mm (0.67 in.)
390 Nm
(288 ft lbs)
ER 400 L
17 mm (0.67 in.)
390 Nm
(288 ft lbs)
ER 450 L
17 mm (0.67 in.)
390 Nm
(288 ft lbs)
ER 600 L
17 mm (0.67 in.)
390 Nm
(288 ft lbs)
ERL 700
19 mm (0.75 in.)
700 Nm
(516 ft lbs)
ERL 1100
19 mm (0.75 in.)
700 Nm
(516 ft lbs)
ER 1500 L
22 mm (0.89 in.)
1500 Nm
(1106 ft lbs)
ER 2000 L
22 mm (0.89 in.)
1500 Nm
(1106 ft lbs)
n
Lower the stick of the carrier into the holder provided
on the adapter plate.
Summary of Contents for ER 100 L
Page 2: ......
Page 7: ...Contents Anbaufräsen PC GmbH 3390 5221 01 2020 09 07 Original Instructions 7 ...
Page 95: ......