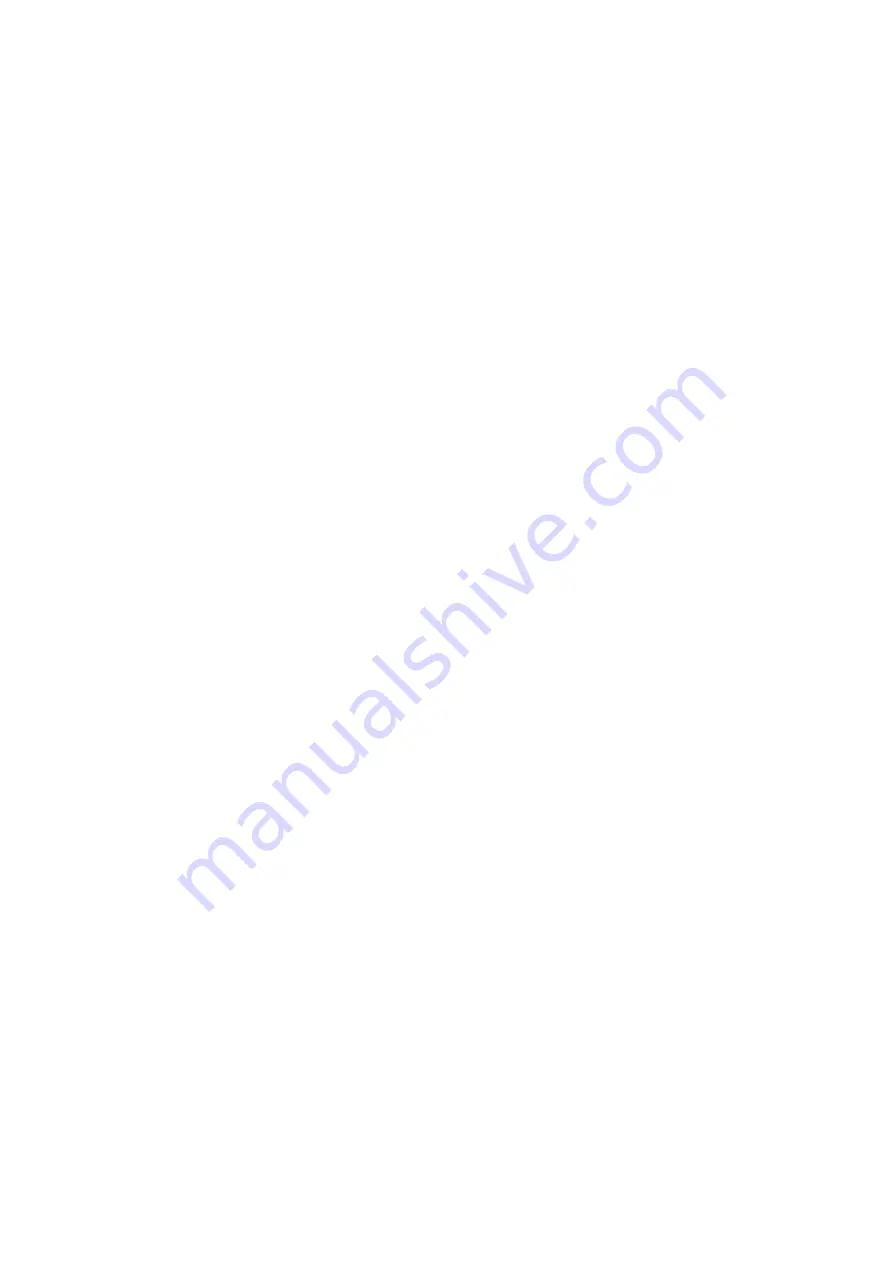
30
in accordance with the intervals indicated in the servicing checklists.
•
Any modification to the truck assemblies, in particular the safety mechanisms, is
prohibited. The operational speeds of the truck must not be changed under any
circumstances.
•
Only original spare parts have been certified by our quality assurance department.
To ensure safe and reliable operation of the truck, use only the manufacturer's spare
parts. Used parts, oils and fuels must be disposed of in accordance with the relevant
environmental protection regulations. For oil changes, contact the manufacturer
’
s
specialist department.
• Upon completion of inspection and servicing, carry out the activities listed in the
“
Recommissioning
”
section.
5.2Maintenance Safety Regulations
Maintenance personnel
trucks must only be serviced and maintained by
the manufacturer’s trained personnel.
The manufacturer’s service department has field technicians specially trained for
these tasks. We therefore recommend a maintenance contract with the
manufacturer’s local service centre.
Lifting and jacking up
When a truck is to be lifted, the lifting gear must only be secured to the points
specially provided for this purpose.
When jacking up the truck, take appropriate measures to prevent the truck from
slipping or tipping over (e.g. wedges, wooden blocks).
You may only work underneath a raised load handler if it is supported by a sufficiently
strong chain.
Cleaning
Do not use flammable liquids to clean the truck.
Prior to cleaning, all safety measures required to prevent sparking (e.g. through short
circuits) must be taken. For battery-operated trucks, the battery connector must be
removed. Only weak suction or compressed air and non-conductive antistatic brushes
may be used for cleaning electric or electronic assemblies.
If the truck is to be cleaned with a water jet or a high-pressure cleaner, all electrical
and electronic components must be carefully covered beforehand as moisture can
cause malfunctions.
Do not clean with pressurised water.
After cleaning the truck
, carry out the activities detailed in the “Recommissioning
” section.
Electrical System
Only suitably trained personnel may operate on the truck
’s electrical system.
Before working on the electrical system, take all precautionary measures to avoid
–
electric shocks.
Summary of Contents for CQD15S
Page 1: ...I ...
Page 17: ...10 ...
Page 18: ...11 1 4 Identification points and data plates ...
Page 23: ...16 3 2 Controls and Displays 3 2 1 Control panel controls and displays ...