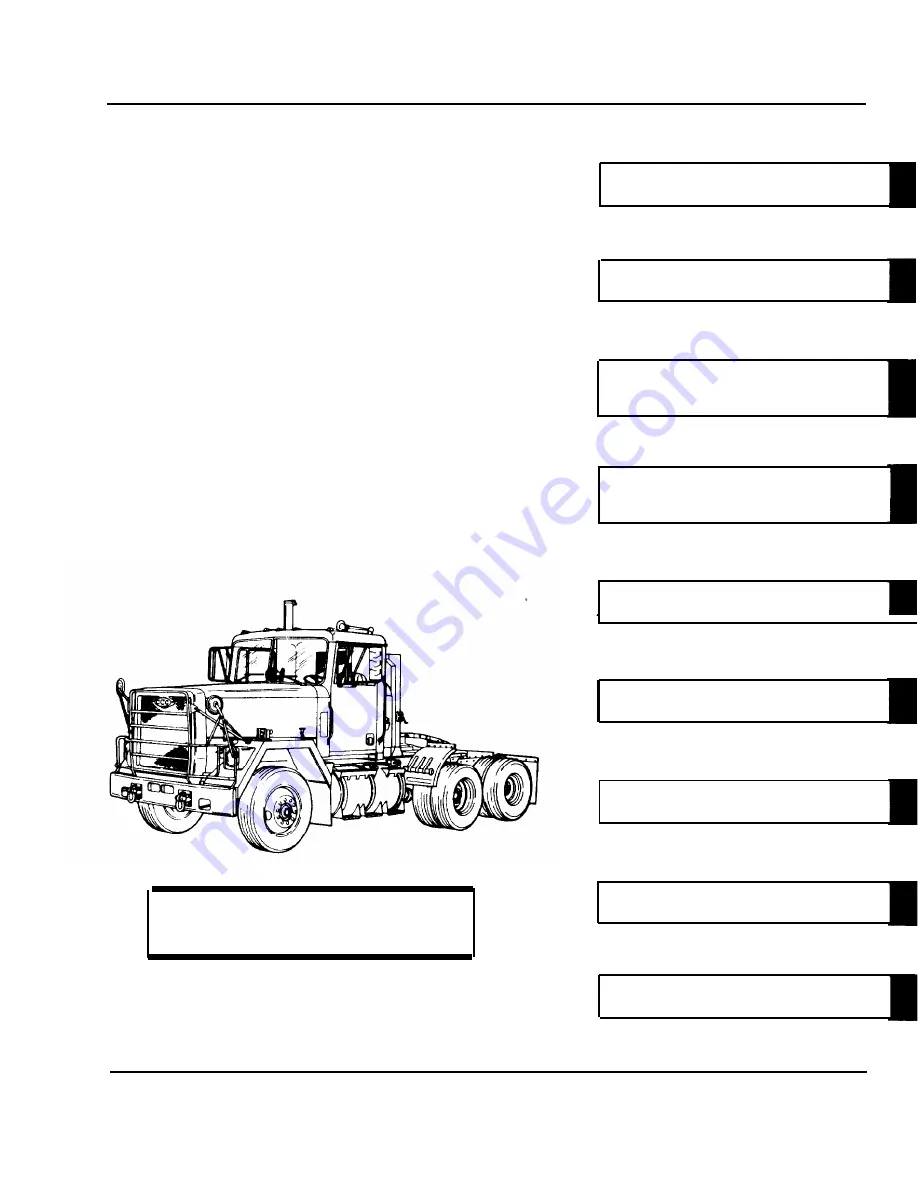
TM 9-2320-283-20-3
TECHNICAL MANUAL
ORGANIZATIONAL
MAINTENANCE
TRUCK TRACTOR, LINE HAUL,
50,000 GVWR, 6 x 4, M915A1
(NSN 2320-01-125-2640)
This copy is a reprint which includes current
pages from Change 1.
WHEELS
PAGE 3-1203
STEERING SYSTEM
PAGE 3-1245
FRAME AND TOWING
ATTACHMENTS
PAGE 3-1329
SPRINGS, SHOCK ABSORBERS,
AND TORQUE RODS
PAGE 3-1470
CAB AND BODY
PAGE 3-1492
ACCESSORY ITEMS
PAGE 3-1672
GAGES (NON-ELECTRICAL)
PAGE 3-1786
STE/ICE COMPONENTS
PAGE 3-1832
HEADQUARTERS,
DEPARTMENT
OF
THE ARMY
APPENDICES
PAGE A-1
DECEMBER 1983
Summary of Contents for M915A1
Page 10: ......
Page 17: ......
Page 59: ......
Page 130: ......
Page 155: ......
Page 378: ...TM 9 2320 283 20 3 CAB AND BODY 3 264 OUTSIDE FRONT HANDLE REPLACEMENT Continued 3 1551...
Page 622: ...TM 9 2320 283 20 3 GAGES NONELECTRICAL 3 309 TACHOGRAPH REPLACEMENT Continued TA 237846 3 1795...
Page 669: ......
Page 673: ......
Page 705: ......
Page 707: ......
Page 717: ......
Page 737: ......
Page 738: ......
Page 739: ......
Page 740: ......
Page 741: ......
Page 742: ......
Page 743: ......
Page 744: ......
Page 745: ......
Page 746: ......
Page 748: ......
Page 756: ...PIN 054576 000...