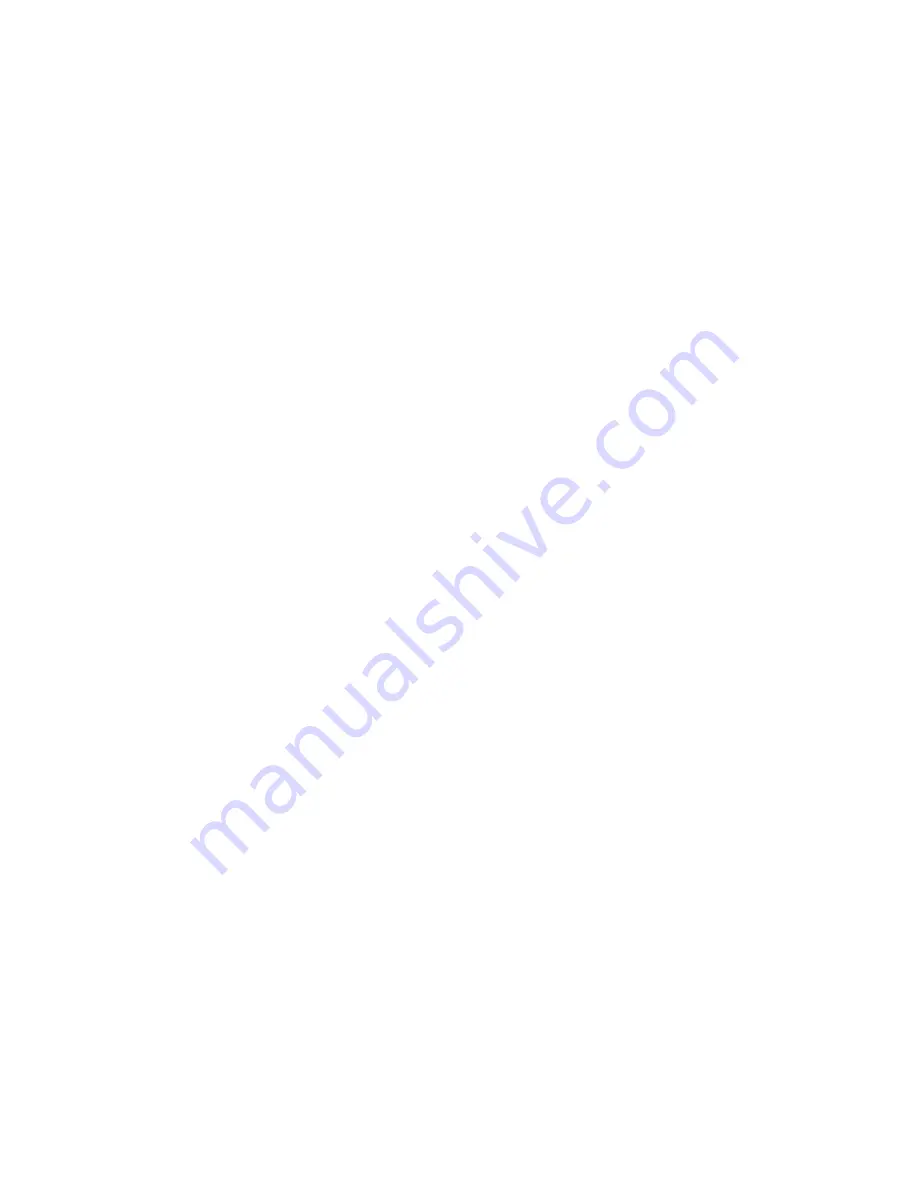
ENVIRO-TEC
7
FORM ET115.24-NOM4 (819)
TABLE OF CONTENTS (CONT'D)
SECTION 3 - NORMAL OPERATION & PERIODIC MAINTENANCE ................................................................... 42
General ......................................................................................................................................................... 42
Motor/Blower Assembly ................................................................................................................................ 42
Coil ................................................................................................................................................................. 42
Electric Resistance Heater Assembly ............................................................................................................. 42
Electrical Wiring & Controls .......................................................................................................................... 43
Valves & Piping ............................................................................................................................................. 43
Filters, Throwaway ....................................................................................................................................... 44
Drain ............................................................................................................................................................. 44
Optional Removable Drain Pan .................................................................................................................... 44
Replacement Parts ....................................................................................................................................... 44
SECTION 4 - INSPECTION, INSTALLATION & START-UP CHECKLIST ............................................................. 46
SECTION 5 - TROUBLESHOOTING ......................................................................................................................48
SECTION 6 - DIMENSIONAL DATA .......................................................................................................................51
Vertical Hi-Rise Tandem Units
VHA/VHB Installation Instructions .................................................................................................................. 75
Receipt & Initial Installation ................................................................................................................... 75
Temperature ................................................................................................................................................... 79
Summary of Contents for VHA
Page 10: ...ENVIRO TEC 10 FORM ET115 24 NOM4 819 THIS PAGE INTENTIONALLY LEFT BLANK ...
Page 41: ...ENVIRO TEC 41 SECTION 2 START UP FORM ET115 24 NOM4 819 THIS PAGE INTENTIONALLY LEFT BLANK ...
Page 54: ...ENVIRO TEC 54 FORM ET115 24 NOM4 819 SECTION 6 Dimensional Data 74 80083 ...
Page 78: ...ENVIRO TEC 78 FORM ET115 24 NOM4 819 SECTION 6 Dimensional Data NOTES ...