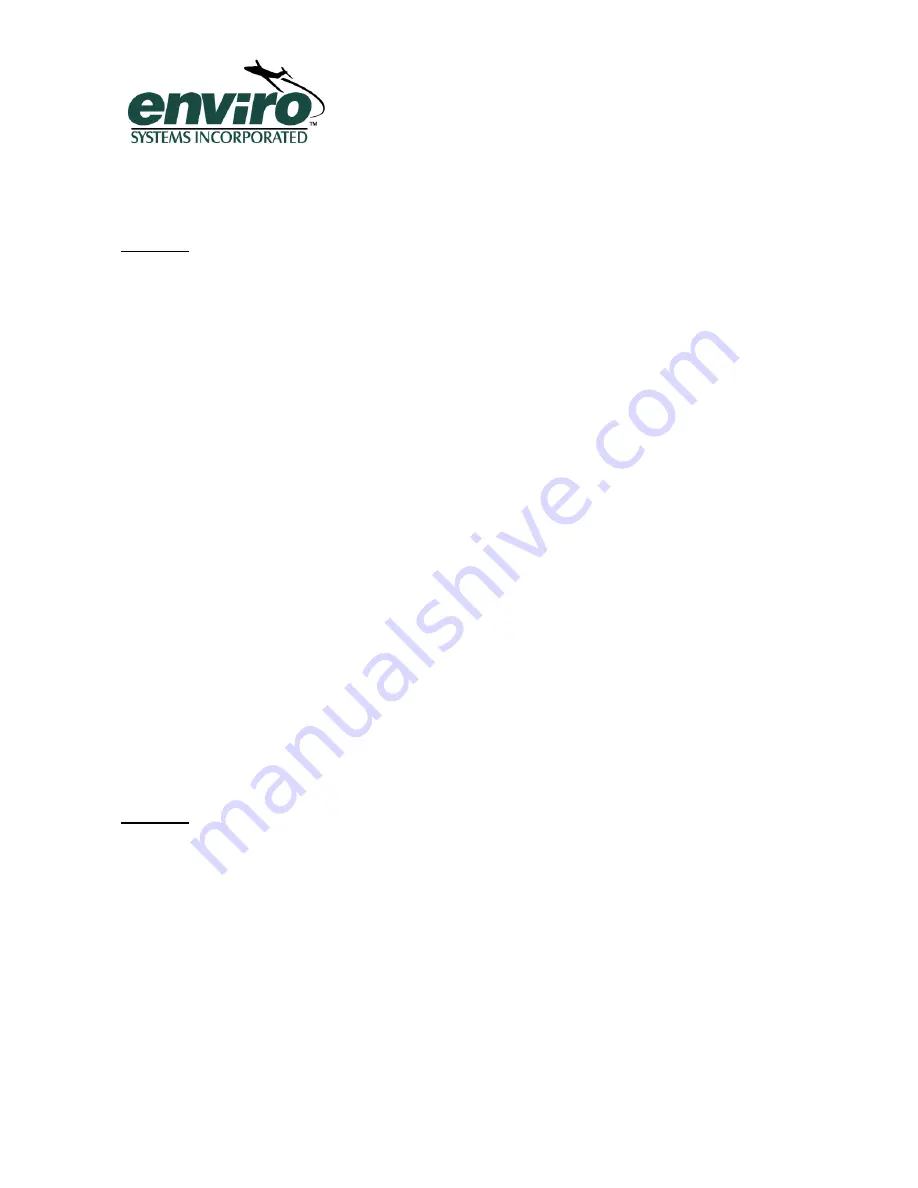
Component Maintenance Manual
12037 N Highway 99
Seminole, OK 74868
Phone (405) 382-0731
Fax (405) 382-0737
http://www.enviro-ok.com
Copyright © 2017
ATA 21-00-23
P a g e
|
58
Revision 10
June 1, 2017
9.2.1
Assembly of Drive Motor (10C)
CAUTION
: TAKE EXTREME CARE WHEN INSTALLING DRIVE MOTOR ONTO ASSEMBLY OR DAMAGE
TO COIL OR FAN SHROUD COULD OCCUR.
9.2.1.1
Set motor near unit and connect motor power wires to the relay and ground bolt.
9.2.1.2
Carefully slide drive motor into position.
9.2.1.3
Install 8 mounting bolts finger tight only. Install upper compressor mounting bracket at
this time as shown in IPL.
9.2.1.4
Tighten all motor mounting bolts except the 2 bolts used to secure the belt cover per
Table 1.
9.2.1.5
Connect electrical harness.
9.2.1.6
Install fan per 9.2.2.
9.2.1.7
Install compressor assembly per 9.2.3.
9.2.1.8
Install drive motor belt and pulley per 9.2.4.
9.2.1.9
Install belt cover per 9.2.5.
9.2.1.10 Install fan shroud, outlet shroud and condenser coil per 9.2.6, 9.2.7 and 9.2.8.
9.2.1.11 Install receiver dryer per 9.2.9
9.2.1.12 Safety wire screws in place.
9.2.2
Assembly of Fan
9.2.2.1
Slide fan assembly onto motor shaft against shoulder.
CAUTION
: APPLY THREAD SEALANT SPARINGLY TO THREADS OF SET SCREW(S) STAYING CLEAR
OF FIRST 2-3 THREADS.
9.2.2.2
Apply a drop of thread sealant to the set screw thread. Tighten fan assembly set
screw lightly insuring that the screw is located on flat part of motor shaft.
9.2.2.3
Install flat washer and retaining nut and tighten nut and torque per Table 1.
9.2.2.4
Tighten set screw per Table 1.
9.2.2.4.1 On 1134400-59 only – Install second set screw and fully tighten both fan set
screws.