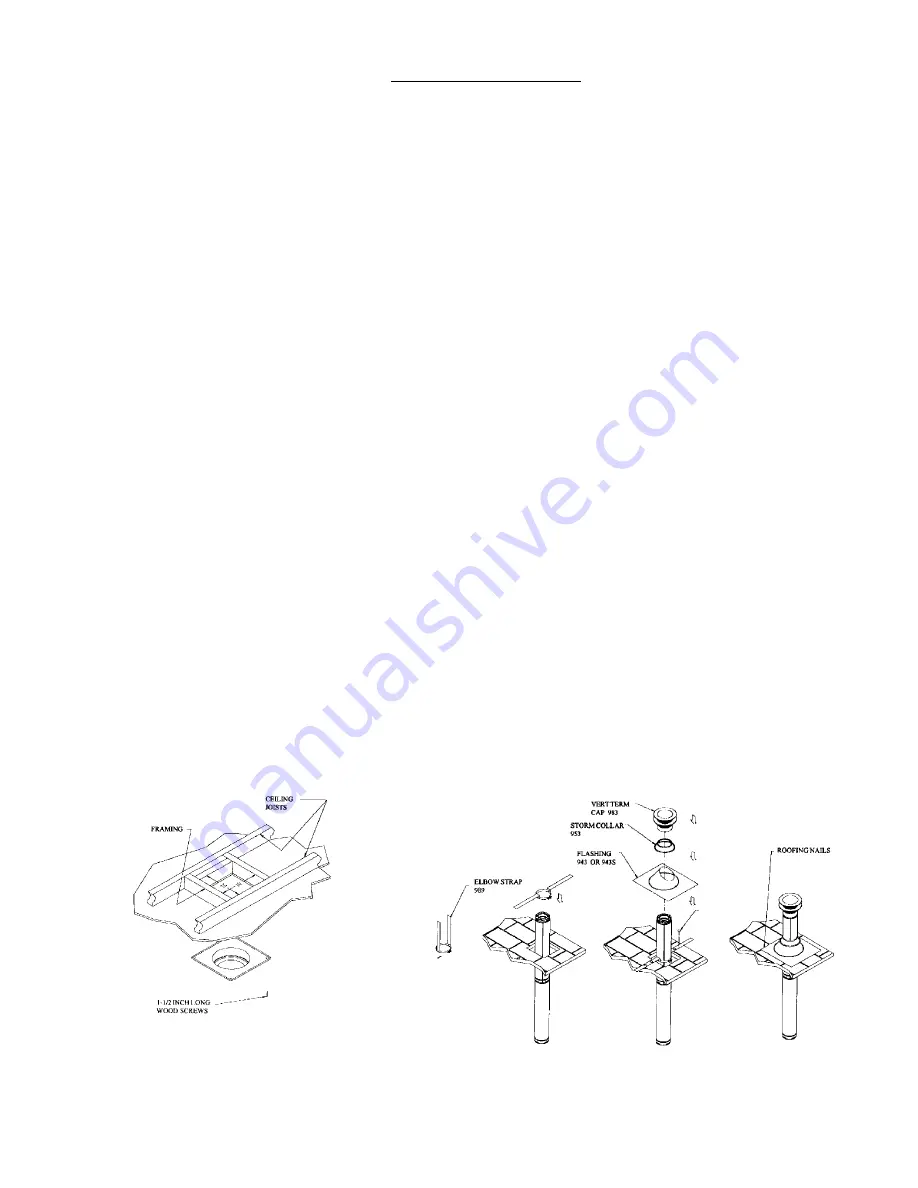
VERTICAL INSTALLATION
STEP 1. Check the instructions for required clearances (air spaces) to combustibles when passing through ceilings, walls,
roofs, enclosures, attic rafters, or other nearby combustible surfaces. Do not pack air spaces with insulation.
STEP 2. Set the gas appliance in the desired location. Drop a plumb bob down from the ceiling to the position of the appliance
flue exit, and mark the location where the vent will penetrate the ceiling. Drill a small hole at this point. Next, drop a
plumb bob from the roof to the hole previously drilled in the ceiling, mark the spot where the vent will penetrate the
roof. Determine if ceiling joists, roof rafters, or other framing will obstruct the venting system. You may wish to
relocate the appliance, or to offset, to avoid cutting load bearing members.
STEP 3. To install the Round Support Box/Wall Thimble in a flat ceiling, cut a 10- inch square hole in the ceiling, centered in
the hole drilled in Step 2. Frame the hole as shown in FIG-16.
STEP 4. Assemble the desired lengths of black pipe and elbows necessary to reach from the appliance adapter up through
the Round Support Box. Insure that all pipe and elbow connections are in their fully twist-locked position.
STEP 5. Cut hole in the roof centered on the small hole placed in the roof from Step 2. The hole should be of sufficient size to
meet minimum requirements for Clearance to Combustibles, as specified. Continue to assemble lengths of pipe and
elbows necessary to reach from the ceiling Support Box up through the roofline. Galvanized pipe and elbows may be
utilized in the attic, as well as above the roofline. The galvanized finish is desirable above the roofline, due to the
higher corrosion resistance.
STEP 6. Once the pipe sections have been joined, and run up through the hole in he roof, slip an elbow strap (Part-989) over
the exposed sections, bend the support straps outwards, and push the Elbow Strap down to the roof level, as shown
in FIG 17. Tighten the clamp around the Pipe section. Use a level to make sure the pipe is truly vertical. With roofing
nails, secure the support straps to the roof. Seal the nails holes heads with non-hardening mastic. Trim the excess
length of the support straps that extend out beyond the edge of the flashing.
STEP 7. Slip the flashing over the pipe section protruding through the roof. Secure the base of the flashing to the roof with
roofing nails. Use a non-hardening sealant between the uphill edge of the flashing and the roof. Insure the roofing
material overlaps the top edge of the flashing as shown in FIG 17. Verify that you have at least the minimum
clearance to combustibles at the roofline.
STEP 8. Continue to add pipe sections until the height of the vent cap meets the minimum code requirements. FIG 22. Note
that for steep roof pitches, the vent height must be increased. In high wind conditions, nearby trees, adjoining roof
lines, steep pitched roofs, and other similar factors can result in poor draft, or down drafting. In these cases,
increasing the vent height may solve the problem.
STEP 9. Slip the Storm Collar over the pipe, and push it down to the top of the roof flashing as shown in FIG 17. Use the non-
hardening sealant around the joint between the pipe and the Storm Collar.
STEP 10. Twist - lock the vent cap.
FIG-16
FIG-17
9