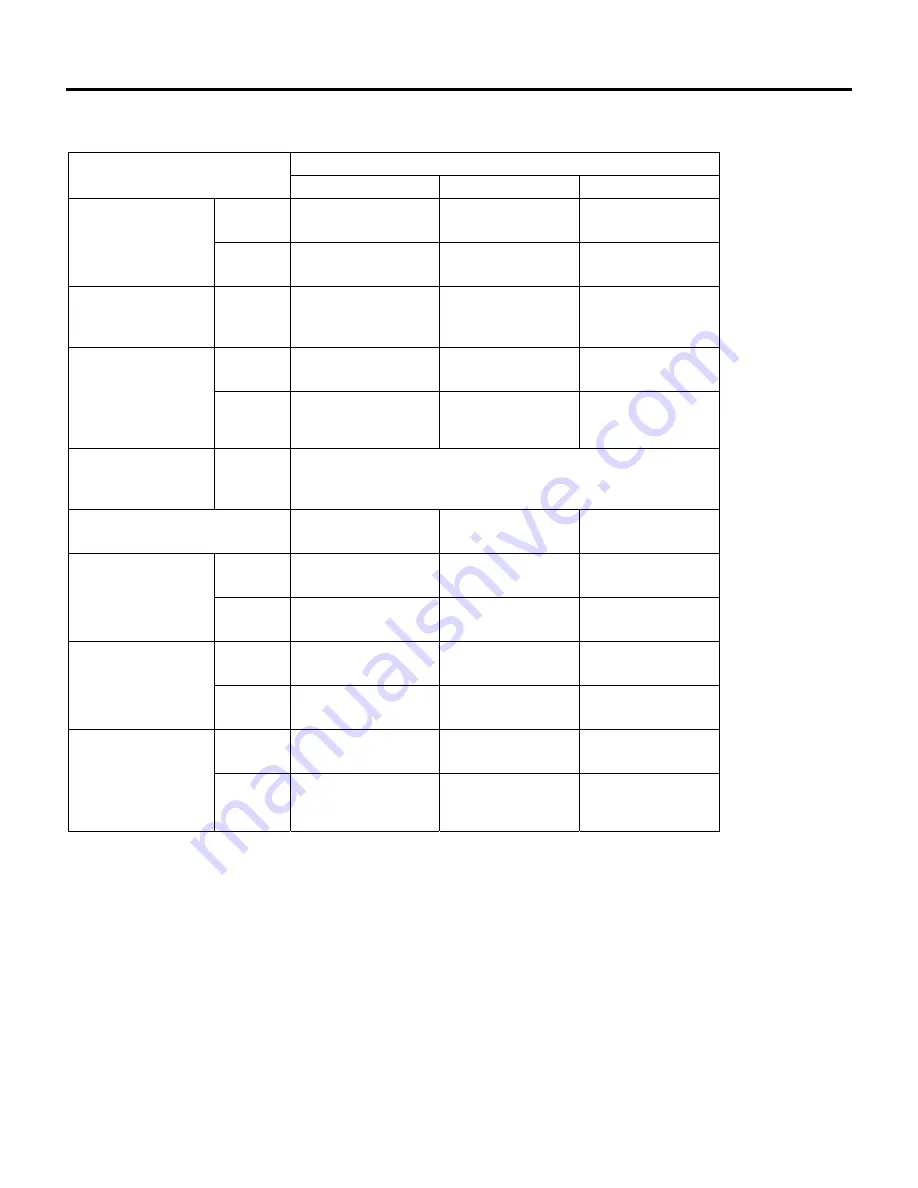
A
PD MANUAL
IOM-39
34 of 36
Aug 99 R1
Table 2
Refrigerant
R407C
R134a
R410A
Low
pressure
control
Cut
In
60
psig
(410
kPa)
30
psig
(210
kPa)
105
psig
(720
kPa)
Cut
Out
30
psig
(210
kPa)
10
psig
(70
kPa)
75
psig
(520
kPa)
High
pressure
control
NO
RECEIVER
Cut
Out
410
psig
(2830
kPa)
Manual
reset
275
psig
(1890
kPa)
Manual
reset
610
psig
(4200
kPa)
Manual
reset
High
pressure
control
for
UPW
(Water
cooled
condenser
–
auto
reset)
Cut
In
200
psig
(1380
kPa)
150
psig
(1030
kPa)
340
psig
(2340
kPa)
Cut
Out
325
psig
(2240
kPa)
250
psig
(1720
kPa)
460
psig
(3170
kPa)
High
pressure
control
/w
Receiver
Cut
Out
The
lower
of
that
noted
above
or
the
maximum
rated
working
pressure
of
the
receiver
or
90%
of
the
receiver
PRV.
Hot
gas
bypass
Start
to
open
pressure.
52
psig
(350
kPa)
30
psig
(210
kPa)
105
psig
(720
kPa)
CFC1
Cut
In
290
psig
(1990
kPa)
155
psig
(1060
kPa)
400
psig
(2750
kPa)
Cut
Out
220
psig
(1510
kPa)
105
psig
(720
kPa)
300
psig
(2070
kPa)
CFC2
Cut
In
310
psig
(2130
kPa)
170
psig
(1170
kPa)
470
psig
(3240
kPa)
Cut
Out
240
psig
(1650
kPa)
120
psig
(820
kPa)
350
psig
(2410
kPa)
Tandem
compressor
c/w
compressor
loading
control
(CLC)
Cut
In
98
psig
(675
kPa)
46
psig
(315
kPa)
150
psig
(1030
kPa)
Cut
Out
58
psig
(400
kPa)
33
psig
(230
kPa)
115
psig
(790
kPa)
Cylinder
Unloading
Controls
(CUC)
should
be
set
to
be
fully
unloaded
with
a
SST
no
less
than
34°F
(1°C)
and
with
enough
differential
to
prevent
short
cycling
(no
higher
than
50
‐
55°F
(10
‐
13°C)
SST).