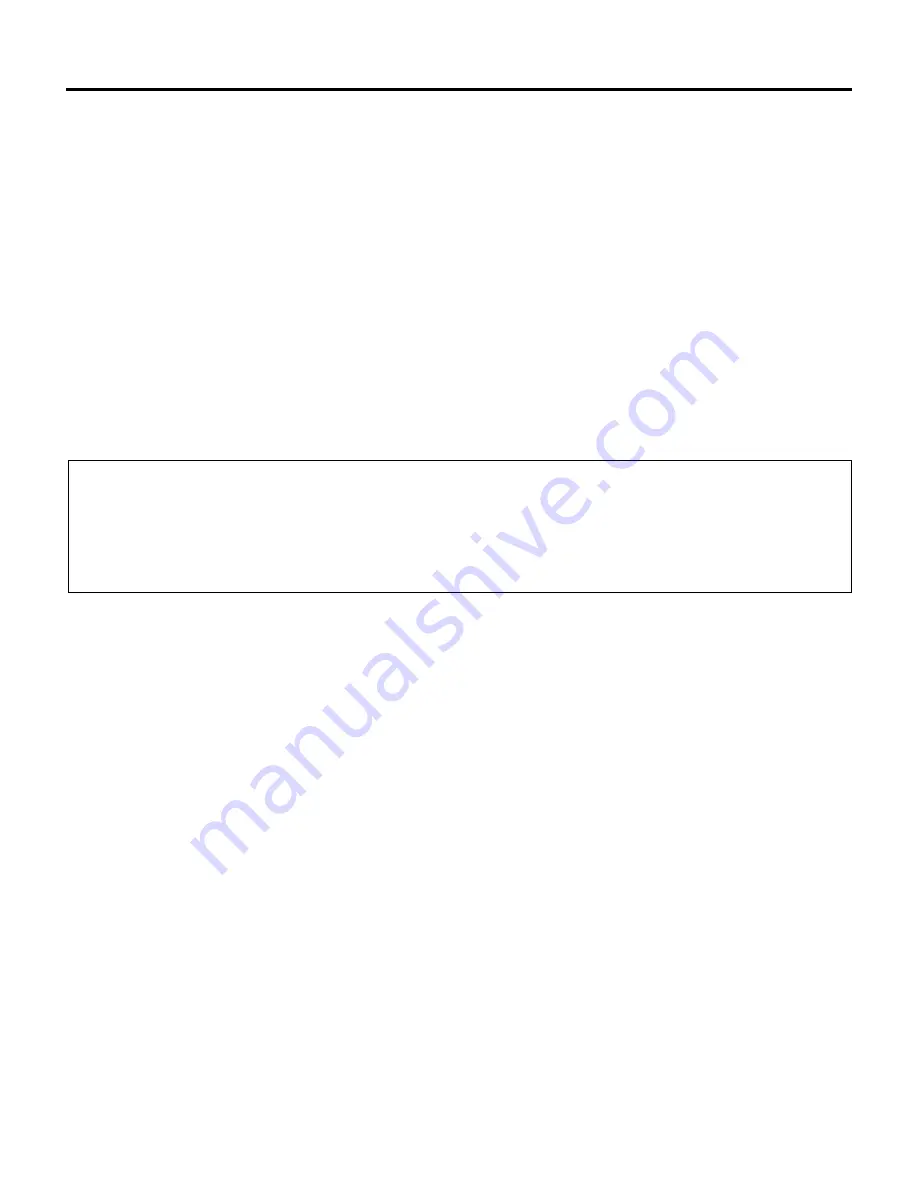
A
PD MANUAL
IOM-39
15 of 36
Aug 99 R1
Some
systems
may
use
CPVC
piping.
Do
not
use
propylene
glycol
with
CPVC.
POOL WATER PIPING
Some
systems
may
incorporate
a
heat
exchanger
to
reject
heat
to
the
pool
water.
The
pool
water
piping
should
be
considered
as
potable
water.
Use
proper
piping
materials
for
pool
water.
BEFORE
START
‐
UP
Remove
tie
‐
down
bolts,
straps
and
blocks
on
fan
and
compressor
vibration
isolators,
tilt
equipped
heat
pipes
and
enthalpy/desiccant
wheels
if
supplied.
Ensure
all
opening
covers
are
removed.
START
‐
UP
CHECK
LIST
Warning:
This
unit
is
connected
to
high
voltages.
Electrical
shock
or
death
could
occur
if
instructions
are
not
followed.
This
equipment
contains
moving
parts
that
can
start
unexpectedly.
Injury
or
death
could
occur
if
instructions
are
not
followed.
All
work
should
be
performed
by
a
qualified
technician.
Always
disconnect
and
lock
out
power
before
servicing.
DO
NOT
bypass
any
interlock
or
safety
switches
under
any
circumstances.
The
start
‐
up
and
operation
must
be
in
accordance
with
safe
practices.
Start
‐
up
must
be
performed
by
qualified
personnel.
Complete
attached
start
‐
up
record.
1.
Set
all
associated
electrical
switches,
controls,
thermostats
and
main
disconnect
switch
to
“OFF”
position.
2.
Close
all
manual
valves
and
field
piping
valves.
3.
Before
startup,
review
the
Unit
Function
(mounted
on
the
control
panel
door)
and
all
control
manuals
supplied
with
this
equipment.
On
units
with
heating
sections,
please
follow
the
start
‐
up
procedure
in
the
heating
manuals.
(Pack,
DJ,
DG,
RT,
HE,
LM
‐
K
etc.)
4.
Confirm
all
shipping
materials
has
been
removed.
On
units
with
semi
‐
hermetic
compressors,
remove
four
spring
isolator
spacers
and
back
off
the
top
nut
so
that
there
is
1/32"
(0.8mm)
to
1/16"
(1.6mm)
space
between
the
nut
and
neoprene
spacer.
5.
Check
all
bearings,
drive
and
fan
set
screws
for
tightness.
See
page
26.
6.
Check
drive
alignment
and
belt
tension.
Refer
to
Maintenance,
page
25.
7.
Ensure
that
refrigerant
lines
and
control
capillary
lines
do
not
rub
against
cabinet
or
other
lines.