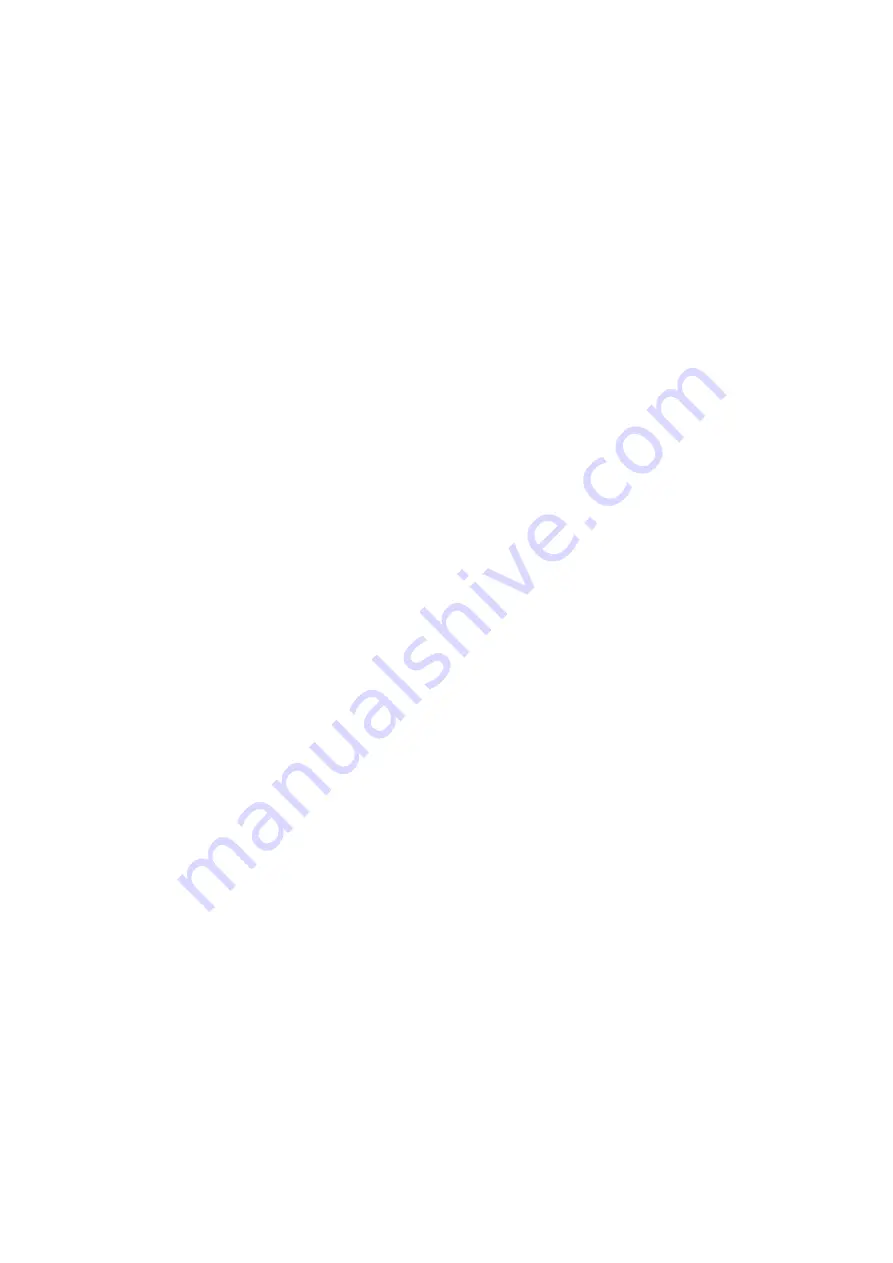
GENERAL INSTRUCTIONS FOR
GASBURNERS
Installation
1.
Follow standards and instructions applicable to the
installation of gas burners
2.
Ensure that the electric installation is made in
accordance with existing regulations
3.
Check that the fresh air intake of the boiler room is
sufficiently dimensioned
4.
Check by studying the data plate that the efficiency
of the burner is adapted to the boiler output
5.
Check that the burner is adapted to the gas quality
in question
6.
Check that the input pressure of the gas is correct
7.
Check that the dampers of the boiler are open
8.
Check that there is water in the system
9.
Check that thermostats etc. are correctly adjusted
10. Read the instructions and follow the directions
given for the burner as to starting-up and service
Maintenance
General instructions
1.
Keep the boiler room clean
2.
Ensure that the fresh air intake of the boiler room is
not restricted
3.
Switch off the current and shut off the gas supply if
the burner must be withdrawn from the boiler
4.
Do not use the boiler for burning paper and waste
if there is no special arrangement ( fire room ) for
this
If the burner has stopped
1.
Press the reset button of the relay
2.
Check that the max. thermostat has not cut out
3.
Check other thermostats for example room ther
mostat, if any
4.
Check that the gas pressure to the burner is
sufficient
5.
Check that the electric fuses have not blown
6.
Make a new attempt to start the burner and check
the counter of the gas meter to find out whether
the solenoid valve opens
7.
If the burner does not start in spite of repeated
starting attempts call the installer
Normal operation
1.
Ensure that the air supply to the burner is not
obstructed by dust and dirt
2.
Have the installer make a yearly overhaul of the
installation so that safety is not jeopardized
3.
Have the installer at the yearly overhaul also adjust
the burner to ensure optimal combustion economy
4.
Check periodically that there is water in the system
( fill up if necessary ) and that thermostats etc. are
normally adjusted
5.
Ensure that there is no water or dampness in
contact with the burner
Shut-Off
1.
Switch off the current with the main switch
2.
Shut-off the gas supply with the shut-off cock on
the burner
Warning
1.
Never keep your face in front of the fire room door
when starting up the burner
2.
Do not use naked flame when inspecting the fire
room
Authorized installer:
____________________________________________________________________________________________________
Address:_____________________________________________________________________________________________
Tel:_________________________________________________________________________________________________
170 025 05 2012-07-06
Summary of Contents for Bentone BG 450
Page 2: ......
Page 6: ...TECHNICAL DATA DIMENSIONSOFFLANGE 172 215 19 00 01 14 210 254 280 163...
Page 26: ......
Page 27: ......
Page 28: ...Enertech AB P O Box 309 SE 341 26 Ljungby www bentone se www bentone com...