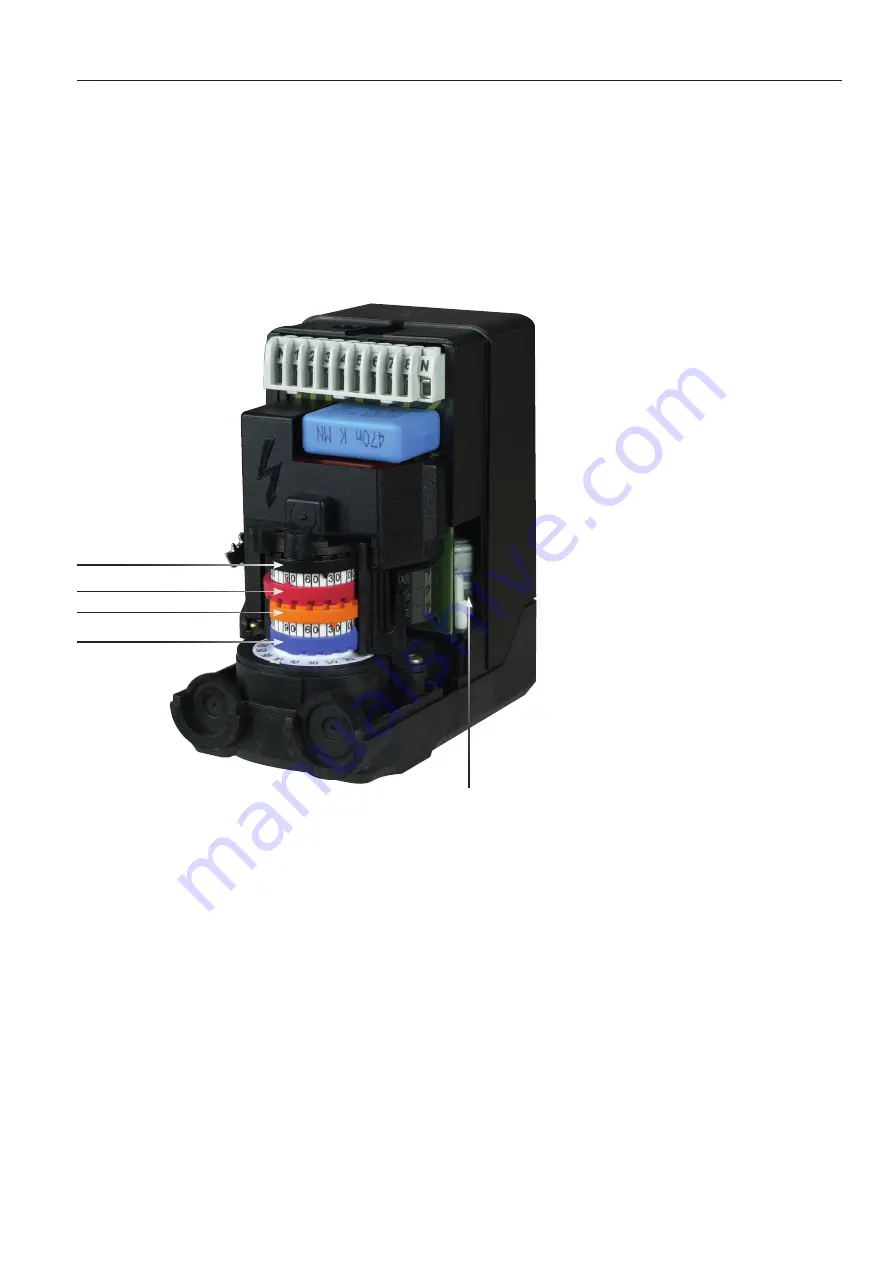
172 305 70 08-01
Air adjustment
The damper motor turns the damper
between three pre-set positions: fully
closed, low load, full load. These
positons are controlled in the motor
by cams of different colours. The
black cam controls the gas valve for
full load.
Low load:
Adjust the operating switch to full
load (ll).
*
Reduce the air volume:
Turn orange cam towards 0°
*
Increase the air volume:
Turn orange cam towards 90°
Adjust the operating switch back to
low load and check the air volume.
Full load
Adjust the operating switch to low
load (l).
*
Reduce the air volume:
Turn red cam towards 0°
*
Inrease the air volume:
Turn red cam towards 90°
If the red cam is moved, change the
black cam as much.
Adjust the operating switch to low
load and check that the correct air
volume has been obtained.
Note!
The blue cam is the limit position for
fully closed damper and it is normally
not necessary to change it.
Releasing button
By pressing the button and snapping
it down, the motor will be released
and the damper can easily be
turned. This function facilitates an
exchange of damper motor.
If the air volume needs changing:
Remove the cover of the damper
motor and change the position of the
cams by turning them with the tools
accompanying the burner.
FUNCTION, 2-STAGE DESIGN
Solenoid valve
High capacity (black)
High capacity (red)
Low capacity (orange)
Closed damper (blue))
Releasing button
N.B.
The upper
position is the
standard position