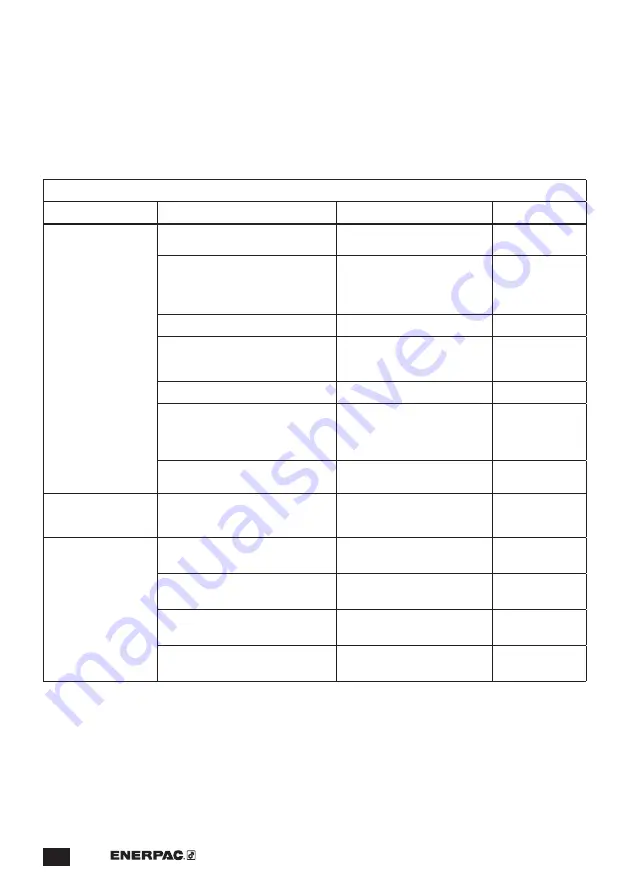
14
10.0 TROUBLESHOOTING
Refer to the Cutter Troubleshooting Chart (Table 2) for
a list of common hydraulic cutter symptoms, possible
causes and solutions.
For repair service, contact an Enerpac authorized service
center. Inspection and repairs should be performed
only by an Enerpac authorized service center or other
qualified hydraulic tool service facility.
Table 2 - Cutter Troubleshooting Chart
Symptom
Possible Cause
Solution
Maint. Level
1. Blades move
slowly and/or have
difficulty cutting
the material.
Excessive cutting debris on the
blades.
Clean out debris.
Operator
Blocked or restricted hydraulic oil
flow.
Check for incomplete
hydraulic connections,
blocked hydraulic hoses or
other similar problems.
Operator
Low hydraulic oil level.
Check oil level. Add oil if low.
Operator
Material being cut is outside of
acceptable specifications.
Material properties must not
exceed stated maximum
limits. Refer to Section 2.1.
Operator
Blade wear.
Replace blades.
Service Center
Low hydraulic oil pressure or flow.
Check pump relief valve
setting. Troubleshoot and
repair pump and solenoid
control valve (as required).
Service Center
Cutter seal wear and/or internal
damage.
Repair cutter as required.
Service Center
2. Cutter vibrates
during operation.
Loose or missing screws or bolts.
Verify screws and bolts are
properly tightened. Replace
any missing screws or bolts.
Operator
3. External oil leaks.
Loose hydraulic fittings.
Tighten loose fittings.
Operator
Damaged hydraulic hoses.
Replace hoses.
Operator
Damaged hydraulic couplers.
Replace couplers.
Service Center
Worn or damaged cutter
components.
Repair cutter as required.
Service Center
Summary of Contents for EDCH130
Page 15: ...Notes...
Page 16: ...WWW ENERPAC COM...