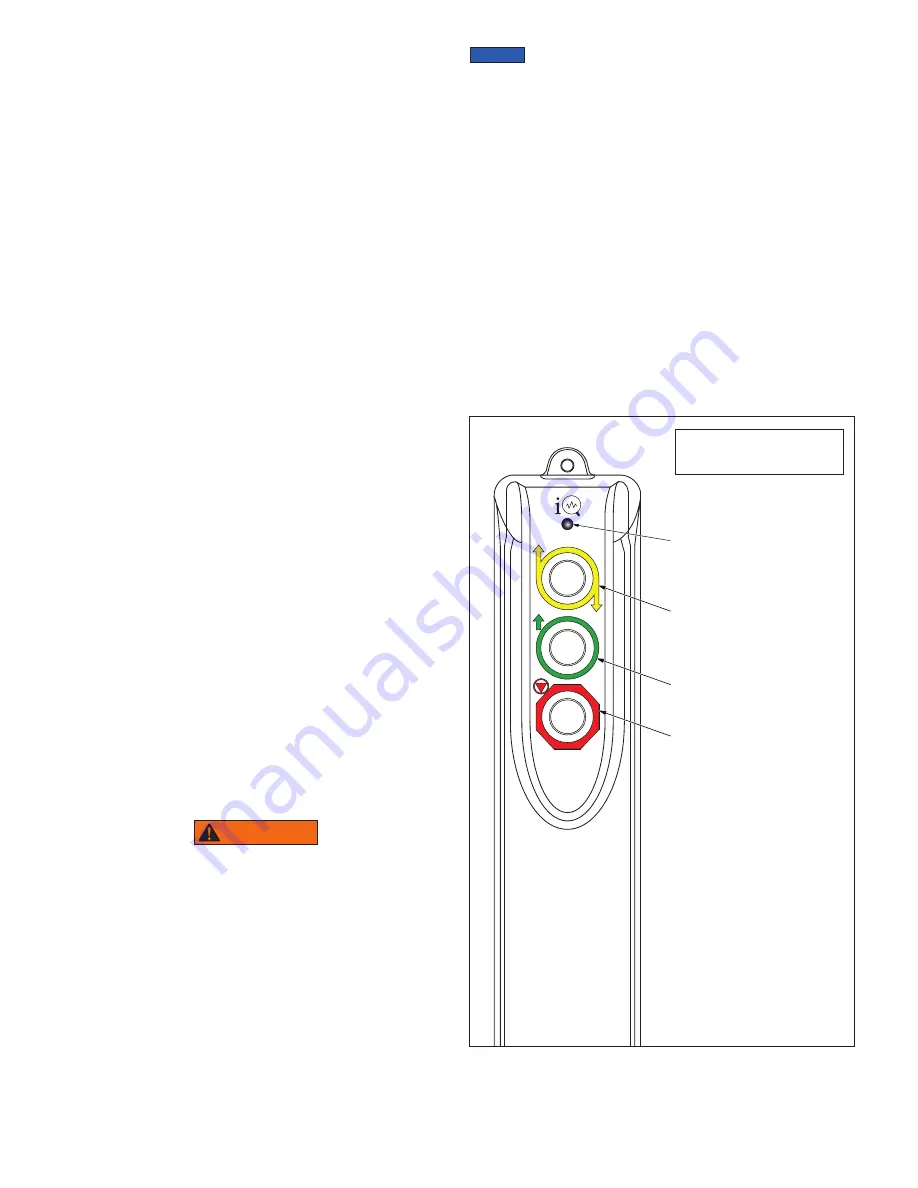
10
5.4 Hydraulic Reservoir
For most shipping destinations, the hydraulic reservoir is pre-
filled at the factory with Enerpac HF hydraulic oil.
However, as a precaution, always check the oil level before
starting the pump. The oil level indicator is located on the pump
front panel. Refer to Figure 8 for oil level diagram.
Verify that the oil level is up to the FULL mark. Refer to Section
11.2 for oil level checking procedure. If the oil level is low, add
additional oil as required as described in Section 11.3.
5.5 Hydraulic Reservoir Air Breather/Filter
The hydraulic reservoir air breather is located just above the
oil level indicator. It is composed of a porous stainless steel
filter disc and a pre-loaded two-way vent. The vent allows air
exchange while maintaining a small positive pressure or vacuum
in the reservoir.
Air breather components are factory pre-installed and require no
user assembly or adjustment.
An absorbent pad is affixed to the front of the air breather to help
prevent oil leakage during shipment. Remove this absorbent pad
before using the pump. Wipe off any residual oil with a clean rag.
Note that a small amount of oil may collect on the air breather
surface while the pump is being transported. This is normal.
However, to prevent possible oil leakage through the air breather,
avoid tilting the pump forward while the pump is being operated,
transported or stored.
5.6 Power Requirements
E-Series pumps are available in a choice of three different
electrical power configurations:
• Models EP3504TB and EP3504TB-M are designed to operate
at a nominal voltage of 100-120 VAC. These units contain a
USA style NEMA 5-15 power plug.
• Models EP3504TE and EP3504TE-M are designed to operate
at a nominal voltage of 200-250 VAC. These units contain a
USA style NEMA 6-15 power plug.
• Models EP3504TI and EP3504TI-M are designed to operate
at a nominal voltage of 200-250 VAC. These units contain a
European style “Schuko” power plug.
All configurations are single-phase, 50-60 Hz.
Before connecting electrical power to the pump, be certain that
the AC power supply is the proper voltage. Refer to the pump
data plate. Also refer to Section 1.3 for important electrical safety
information and precautions.
WARNING
Failure to follow the electrical safety precautions contained
in Section 1.3 of this manual could result in electric shock.
Death or serious personal injury could occur.
6.0 FEATURES AND CONTROLS
6.1 Carrying Handle
Always use the carrying handle when transporting the pump
to its desired location or when it is necessary to reposition the
pump while it is in use.
The top of the carrying handle contains a storage pocket for the
pendant. The base of the carrying handle contains a storage area
for the pendant cable.
A fault code reference diagram is located inside the pendant
storage pocket.
NOTICE
To prevent possible damage, never attempt to carry
or reposition the pump by dragging it by the hydraulic hoses,
power cord or pendant cable. Damage to the pump, pendant
and/or hoses may result.
6.2 Ventilation and Cooling System
Air intake and exhaust vents are located on the inside edges
of the pump front and rear covers. These vents function with
the pump's internal fan-forced heat exchanger to help maintain
allowable operating temperatures.
Cooling fins are also located on the pump sides.
Before start-up, check that the cooling fins and vents are not
covered by dirt or other obstructions.
6.3 Pendant
The pump includes a three-button corded pendant that operates
pump functions. It is connected to the pump with a 20 ft [6 m]
cable.
A multi-color LED indicator light communicates pump status.
See Figure 4. Pendant operation is described in detail in Sections
8.0 through 10.0 of this manual.
1
2
3
4
Figure 4, Pendant Controls
1. LED Indicator Light
(red, green or yellow
depending on pump
function and status)
2. Yellow Button
3. Green Button
4. Red Button
Note:
Refer to Figure 11
for quick reference guide.
Summary of Contents for E-Pulse E Series
Page 21: ...Notes 21...
Page 22: ...Notes 22...
Page 23: ...Notes 23...
Page 24: ...http www enerpac com...