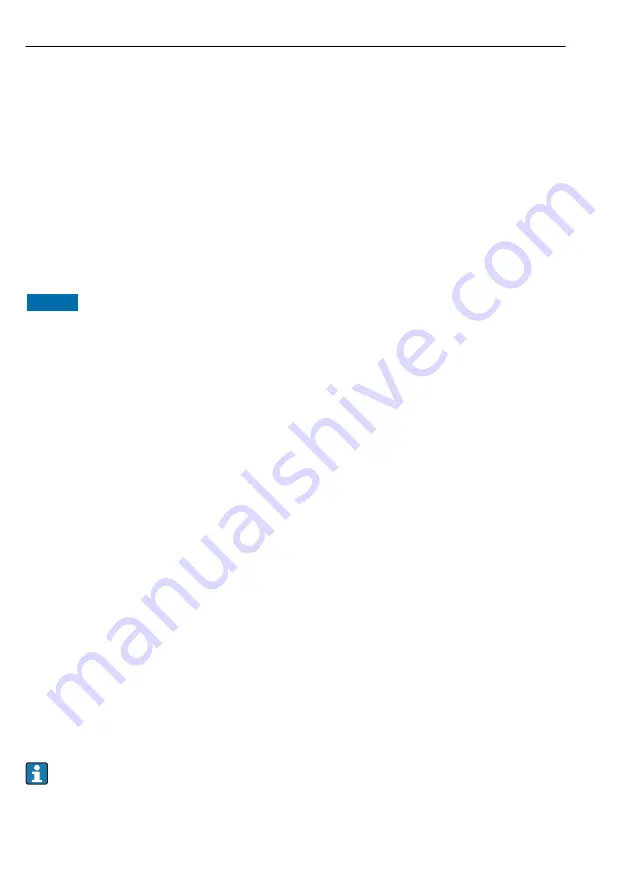
Incoming acceptance and product identification
Levelflex FMP50 PROFIBUS PA
6
Hauser
Hazardous area
To eliminate danger to persons or the installation when the device is used in the hazardous
area (e.g. explosion protection, pressure vessel safety):
‣
Check the nameplate to verify whether the ordered device can be put to its intended use in
the hazardous area.
‣
Observe the specifications in the separate supplementary documentation, which is an
integral part of this manual.
3.5
Product safety
This measuring device is designed in accordance with good engineering practice to meet state-
of-the-art safety requirements, has been tested, and left the factory in a condition in which it
is safe to operate. It meets the general safety standards and legal requirements.
NOTICE
Loss of degree of protection by opening of the device in humid environments
‣
If the device is opened in a humid environment, the degree of protection indicated on the
nameplate is no longer valid. This may also impair the safe operation of the device.
3.5.1
CE mark
The measuring system meets the legal requirements of the applicable EU directives. These are
listed in the corresponding EU Declaration of Conformity together with the standards applied.
The manufacturer confirms successful testing of the device by affixing to it the CE mark.
3.5.2
EAC conformity
The measuring system meets the legal requirements of the applicable EAC guidelines. These
are listed in the corresponding EAC Declaration of Conformity along with the standards
applied.
The manufacturer confirms successful testing of the device by affixing to it the EAC mark.
4
Incoming acceptance and product identification
4.1
Incoming acceptance
Check the following during incoming acceptance:
• Are the order codes on the delivery note and the product sticker identical?
• Are the goods undamaged?
• Do the nameplate data match the ordering information on the delivery note?
• If required (see nameplate): are the Safety Instructions (XA) provided?
If one of these conditions is not met, please contact your Hauser sales office.
Summary of Contents for PROFIBUS PA Levelflex FMP50
Page 27: ......