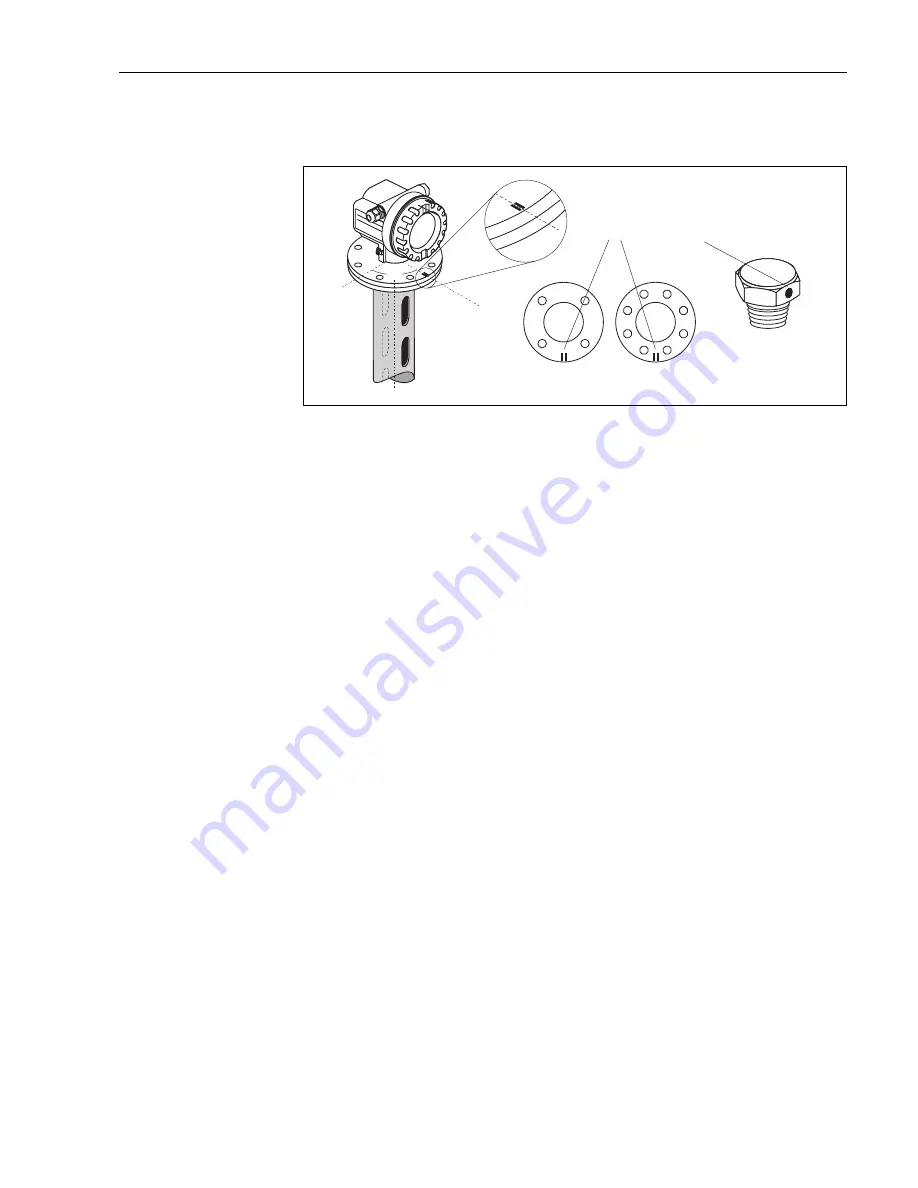
Micropilot M FMR 240 with PROFIBUS PA
Mounting
E Hauser
21
3.4.3
Installation in stilling well
Optimum mounting position
L00-FMR244xx-17-00-00-en-004
Standard installation
For installations in a stilling well, follow the engineering hints on Page 14 and note the
following points:
•
Marker is aligned toward slots.
•
The marker is always exactly in the middle between two bolt-holes in the flange.
•
After mounting, the housing can be turned 350° in order to simplify access to the
display and the terminal compartment.
•
Measurements can be performed through an open full bore ball valve without any
problems.
Recommendations for the stilling well
At the construction of a stilling well, please note the following points:
•
Metal (no enamel coating, plastic coating on request).
•
Constant diameter.
•
Weld seam as smooth as possible and on the same axis as the slots.
•
Slots offset 180° (not 90°).
•
Slot width respectively diameter of holes max. 1/10 of pipe diameter, de-burred.
Length and number do not have any influence on the measurement.
•
Select horn antenna as big as possible. For intermediate sizes (i.e. 90 mm) select next
larger antenna and adapt it mechanically.
•
At any transition (i.e. when using a ball valve or mending pipe segments), no gap may
be created exceeding 1 mm.
•
The stilling well must be smooth on the inside (average roughness Rz
≤
6.3
µ
m). Use
extruded or parallel welded stainless steel pipe. An extension of the pipe is possible
with welded flanges or pipe sleeves. Flange and pipe have to be properly aligned at
the inside.
•
Do not weld through the pipe wall. The inside of the stilling well must remain smooth.
In case of unintentional welding through the pipe, the weld seam and any unevenness
on the inside need to be carefully removed and smoothened. Otherwise, strong
interference echoes will be generated and material build-up will be promoted.
•
Particularly on smaller nominal widths it needs to be observed that flanges are welded
to the pipe such that they allow for a correct orientation (marker aligned toward slots).
90
°
DN80…150
ANSI 3…6”
DN50
ANSI 2”
BSPT (R 1½”),
G 1½" (FMR 244)
or
1½ NPT
1½”
marker at instrument flange
or threaded boss