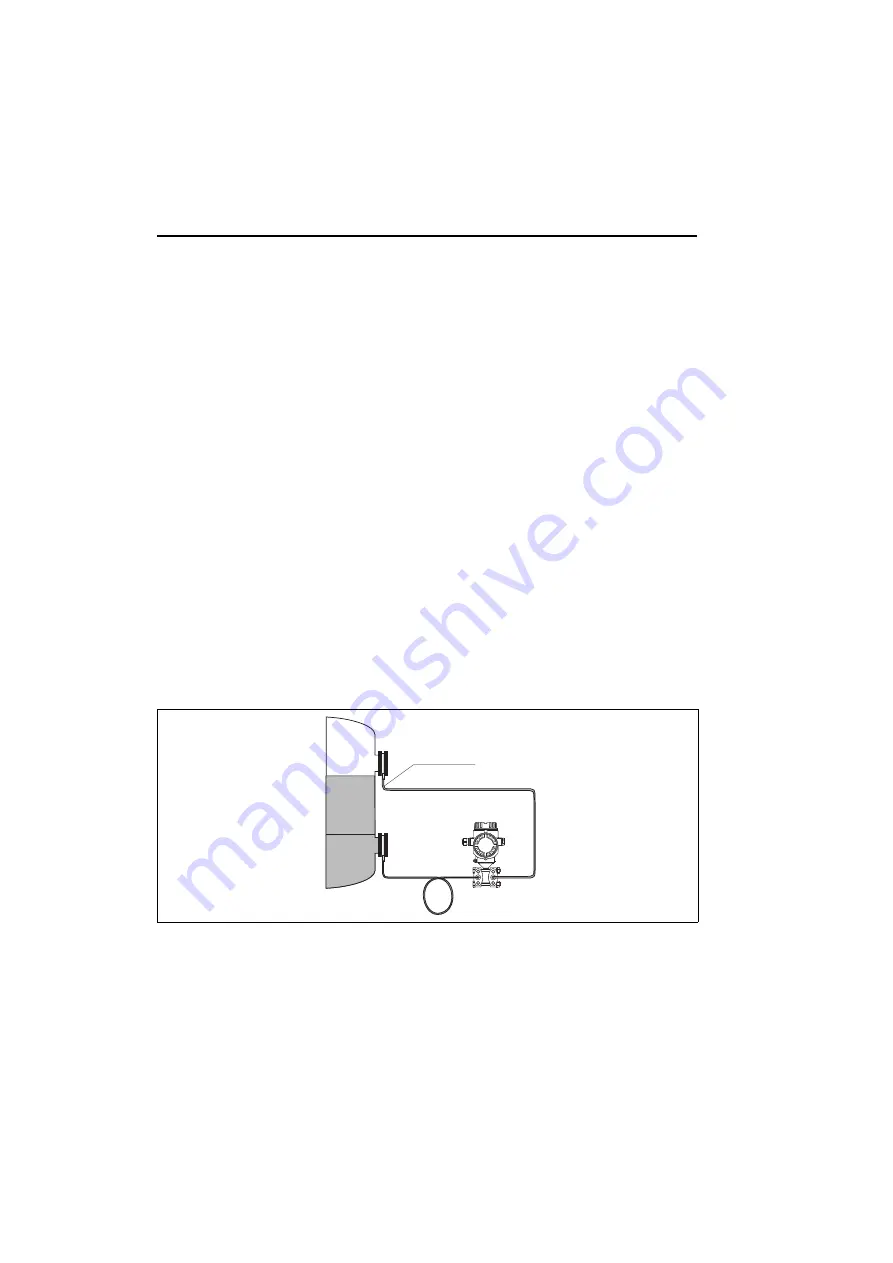
Installation
Deltabar S PROFIBUS PA
12
Hauser
4.4 Installation instructions for devices with diaphragm seals (FMD78)
• The diaphragm seal, together with the pressure transmitter, forms a closed, calibrated
system, which is filled through openings in the diaphragm seal and in the measurement
system of the pressure transmitter. These openings are sealed and must not be opened.
• Do not remove the protection of the process isolating diaphragm protection until shortly
before installation.
• When using a mounting bracket, sufficient strain relief must be ensured for the capillaries in
order to prevent the capillary bending down (bending radius
100 mm).
• Please note that the hydrostatic pressure of the liquid columns in the capillaries can cause
zero point shift. The zero point shift can be corrected.
See Page 20, 4.2.1 "Position of
operating elements", Page 21, Section 4.2.2 "Function of the operating elements" or Page 30,
Section 5.1 "Position adjustment".
• Please note the application limits of the diaphragm seal filling oil as detailed in the Technical
Information for Deltabar S TI00382P, Section "Planning instructions for diaphragm seal
systems" or at "www.endress.com/applicator".
In order to obtain more precise measurement results and to avoid a defect in the device, mount
the capillaries as follows:
• vibration-free (in order to avoid additional pressure fluctuations)
• not in the vicinity of heating or cooling lines
• insulate if the ambient temperature is below ore above the reference temperature
• with a bending radius of
100 mm.
• The ambient temperature and length of both capillaries should be the same when using
two-sided diaphragm seal systems.
• Two diaphragm seals which are the same (e.g. with regard to diameter, material, etc.) should
always be used for the negative and positive side (standard delivery).
P01-FMD78xxx-11-xx-xx-xx-005
Fig. 2: Mounting Deltabar S, FMD78 with diaphragm seals and capillary, recommended mounting for vacuum applications:
mount pressure transmitter below the lowest diaphragm seal!
+ –
+
–
≥
100 mm