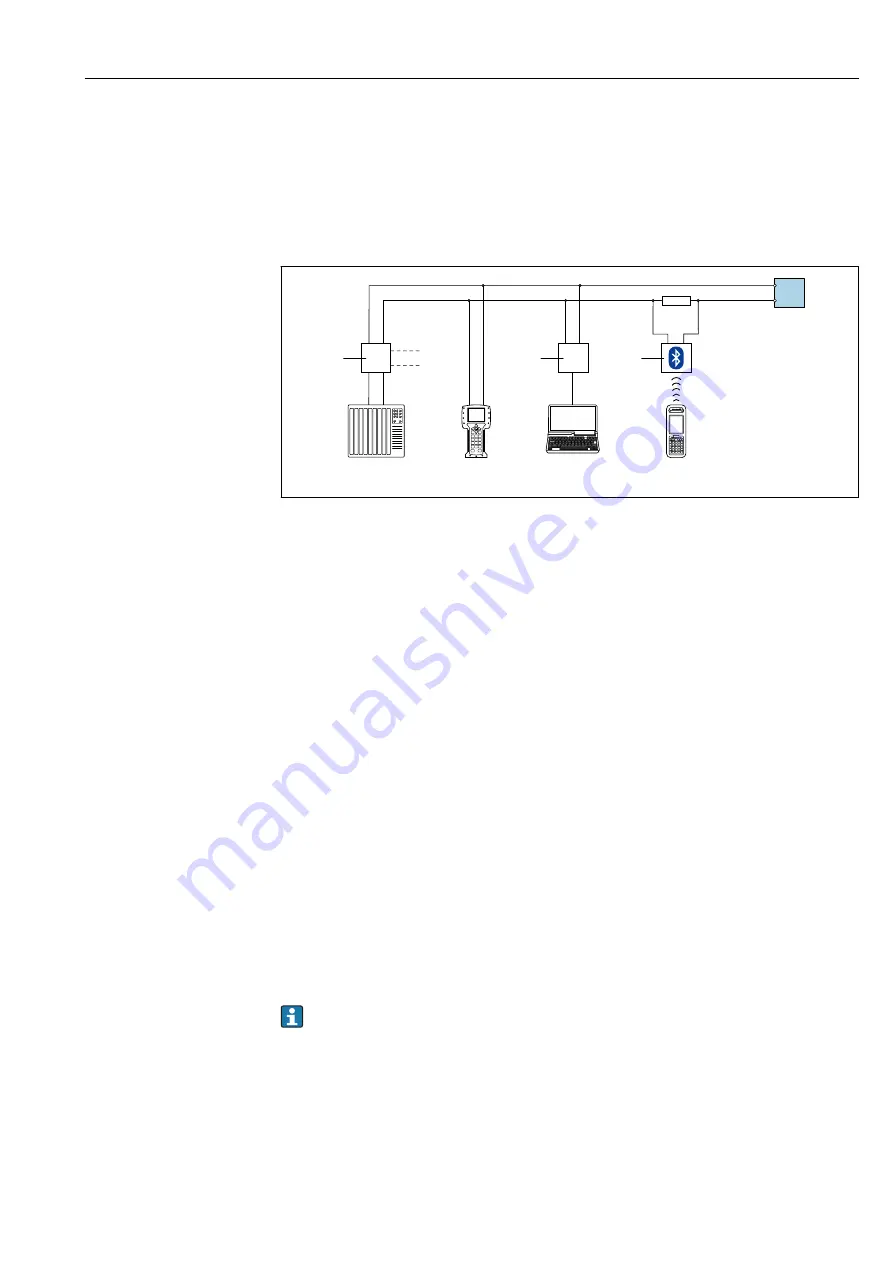
Cerabar S PMP71
Appendix
Hauser
35
8
Appendix
8.1
Structure of the measuring system
8.1.1
System components
1
4
5
7
9
6
8
2
3
A0028746
1
PLC (programmable logic controller)
2
2 transmitter power supply units, e.g. RN221N (with communication resistor)
3
Connection for Commubox FXA191, FXA195 and Field Communicator
4
HART handheld terminal, e.g. Field Communicator
5
Computer with operating tool
6
Commubox FXA191 (RS232) or FXA195 (USB), FXA291
7
Field Xpert
8
VIATOR Bluetooth modem with connecting cable
9
Transmitter
An analog signal (4 to 20 mA) that is in proportion to the pressure is generated in the
transmitter. This is sent to a downstream logic unit (e.g. PLC, limit signal transmitter, etc.)
where it is monitored to determine whether it is below or above a specified limit value.
For fault monitoring, the logic unit must be able to detect both HI alarms (≥ 21.0 mA) and
LO alarms (≤ 3.6 mA).
8.1.2
Description of use as a protective system
The pressure transmitter is used for the following measuring tasks:
• Absolute pressure and overpressure measurement in gases, vapors or liquids in all areas
of process engineering and process measurement technology
• Level, volume or mass measurements in liquids
8.1.3
Installation conditions
The installation conditions for various measurements are described in the Technical
Information for the device.
Correct installation is a prerequisite for safe operation of the device.
8.1.4
Measurement function
The measuring principle and the measurement functions are described in the Technical
Information for the device
Summary of Contents for Cerabar S PMC71
Page 6: ...Declaration of Conformity Cerabar S PMP71 6 Endress Hauser A0046542...
Page 7: ...Cerabar S PMP71 Declaration of Conformity Endress Hauser 7 A0046543...
Page 45: ......
Page 46: ......
Page 47: ......