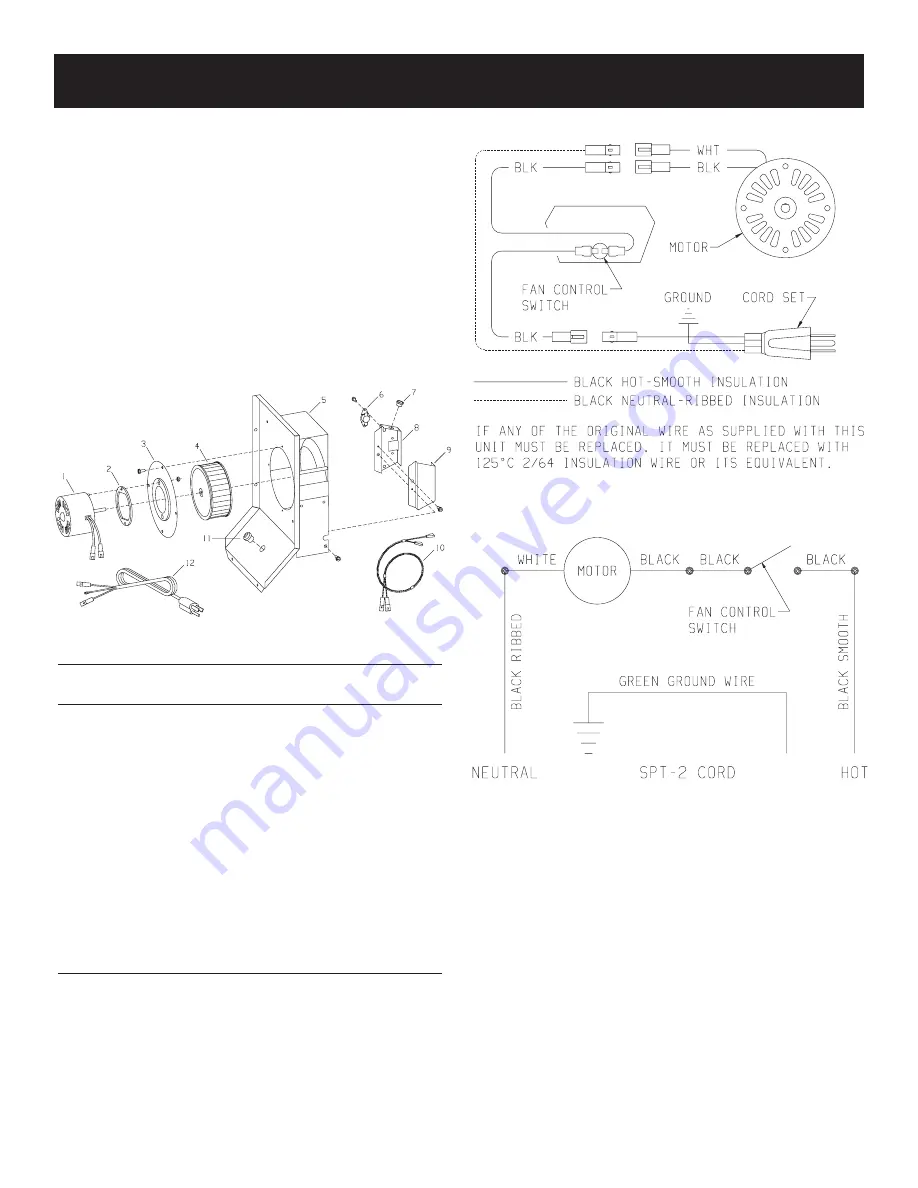
13117-10-0709
Page 18
Cleaning
The blower wheel will collect lint and could require cleaning once
a year. If the air output decreases or the noise level increases,
it indicates a dirty wheel. Complete removal of the wheel and
scrubbing it with a brush under flowing water is recommended.
Oiling
The blower motor has an oil hole located on each end of the motor.
Use #20 motor oil only. It is best to oil the motor several times
during the heating season using 2 or 3 drops each time. If the motor
fails to start and hums, it could be a tight bearing due to lack of
oil. This may be corrected by pouring kerosene in the oil holes,
allowing to stand for a few hours and then oiling properly.
PARTS LIST
Index
No.
Part
No.
Description
1
R-2090
Motor
2
632016
Motor Cushion
3
RH-036
Motor Support
4
642030
Blower Wheel
5
RH-710
Blower Housing assembly
6
9120106
Fan Control Switch
7
872087
Heyco Bushing
8
DV-806
Switch Box
9
DV-807
Switch Box Cover
10
R-2091
Wire Assembly 19" (483mm)
11
8720161
Heyco Bushing
12
R-2099
Cord Set 72" (1.83m)
OPTIONAL BLOWER INSTALLATION INSTRUCTIONS (continued)