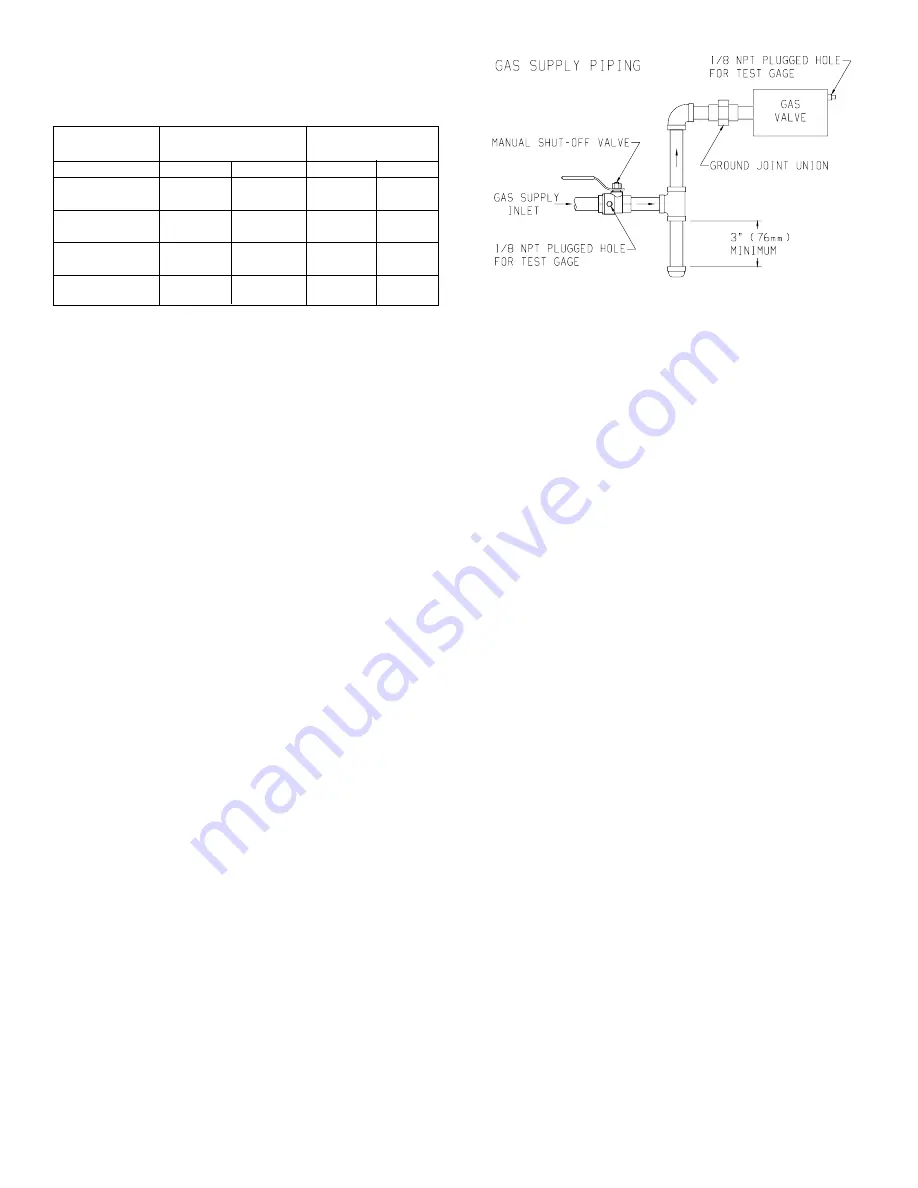
R-3450
Page 9
Gas Supply (Figure 11)
Check all local codes for requirements, especially for the size and type
of gas supply line required.
Recommended Gas Pipe Diameter
Pipe Length
Schedule 40 Pipe
Tubing, Type L
(Feet)
Inside Diameter
Outside Diameter
Nat.
L.P.
Nat.
L.P.
0-10
1/2"
3/8"
1/2"
3/8"
1.3 cm
1.0 cm
1.3 cm
1.0 cm
10-40
1/2"
1/2"
5/8"
1/2"
1.3 cm
1.3 cm
1.6 cm
1.3 cm
40-100
1/2"
1/2"
3/4"
1/2"
1.3 cm
1.3 cm
1.9 cm
1.3 cm
100-150
3/4"
1/2"
7/8"
3/4"
1.9 cm
1.3 cm
2.2 cm
1.9 cm
Note: Never use plastic pipe. Check to confirm whether your local codes
allow copper tubing or galvanized.
Note: Since some municipalities have additional local codes, it is
always best to consult your local authority and installation code.
The use of the following gas connectors is recommended:
—
ANS Z21.24 Appliance Connectors of Corrugated Metal Tubing
and Fittings
—
ANS Z21.45 Assembled Flexible Appliance Connectors of Other
Than All-Metal Construction
The above connectors may be used if acceptable by the authority having
jurisdiction.
Consult the current National Fuel Gas Code, ANSI Z223.1 CAN/CGA-
B149 (.1 or .2) installation code.
Installing a New Main Gas Cock
Each appliance should have its own manual gas cock.
A manual main gas cock should be located in the vicinity of the unit.
Where none exists, or where its size or location is not adequate, contact
your local authorized installer for installation or relocation.
Compounds used on threaded joints of gas piping shall be resistant to the
action of liquefied petroleum gases. The gas lines must be checked for
leaks by the installer. This should be done with a soap solution, watching
for bubbles on all exposed connections and, if unexposed, a pressure test
should be made.
Never Use an Exposed Flame to Check for Leaks.
Appliance must be disconnected from piping at inlet of control valve
and pipe capped or plugged for pressure test. Never Pressure Test
With Appliance Connected; Control Valve Will Sustain Damage!
A gas valve and ground joint union should be installed in the gas line
upstream of the gas control to aid in servicing. It is required by the
National Fuel Gas Code that a drip line be installed near the gas inlet.
This should consist of a vertical length of pipe, tee connected into the gas
line, that is capped on the bottom in which condensation and foreign
particles may collect.
Method of Installing A Tee Fitting Sediment Trap
Figure 11
Pressure Testing of the Gas Supply System
1. To check the inlet pressure to the gas valve, a 1/8" (3mm) N.P.T.
plugged tapping, accessible for the test gauge connection, must be
placed immediately upstream of the gas supply connection to the
appliance.
2. The appliance, and its individual shutoff valve, must be disconnected
from the gas supply piping system during any pressure testing of that
system at test pressures in excess of 1/2 psig (3.5kPa).
3. The appliance must be isolated from the gas supply piping system by
closing its individual manual shutoff valve during any pressure
testing of the gas supply piping system at test pressures equal to or less
than 1/2 psig (3.5kPa).
Attention! If one of the above procedures results in pressures in excess
of 1/2 psig (14" w.c.) (3.5kPa) on the appliance gas valve, it will result in
a hazardous condition.
Checking Manifold Pressure
Both Propane and Natural gas valves have a built-in pressure regulator in
the gas valve. Natural gas models will have a manifold pressure of
approximately 3.5" w.c. (.871kPa) for maximum input or 1.7" w.c.
(.423kPa) for minimum input at the valve outlet with the inlet pressure to
the valve from a minimum of 5.0" w.c. (1.245kPa) for the purpose of input
adjustment to a maximum of 10.5"w.c. (2.615kPa). Propane gas models
will have a manifold pressure approximately 10.0"w.c. (2.49kPa) for
maximum input or 5.9" w.c. (1.469kPa) for minimum input at the valve
outlet with the inlet pressure to the valve from a minimum of 11.0" w.c.
(2.739kPa) for the purpose of input adjustment to a maximum of 13.0"
w.c. (3.237kPa).
A 1/8" (3mm) N.P.T. plugged tapping, accessible for test gauge connection
is located on the outlet side of the gas control.
Liner and Insulated Liner
When you install a vented fireplace heater into a masonry chimney you
must follow these steps.
1. The chimney must be lined and sized properly. Most masonry
chimneys are over sized and absorb too much heat to be considered a
proper vent. If you have any doubts line the chimney with the right
size liner. If it's unlined you must line it.
2. Use an insulated liner when the chimney is on the outside, three sides
exposed to the weather, and there is no clay liner in the chimney. The
insulation will help keep the flue gases warmer.
Summary of Contents for CIBV-30-2
Page 17: ...R 3450 Page 17 ...
Page 19: ...R 3450 Page 19 ...