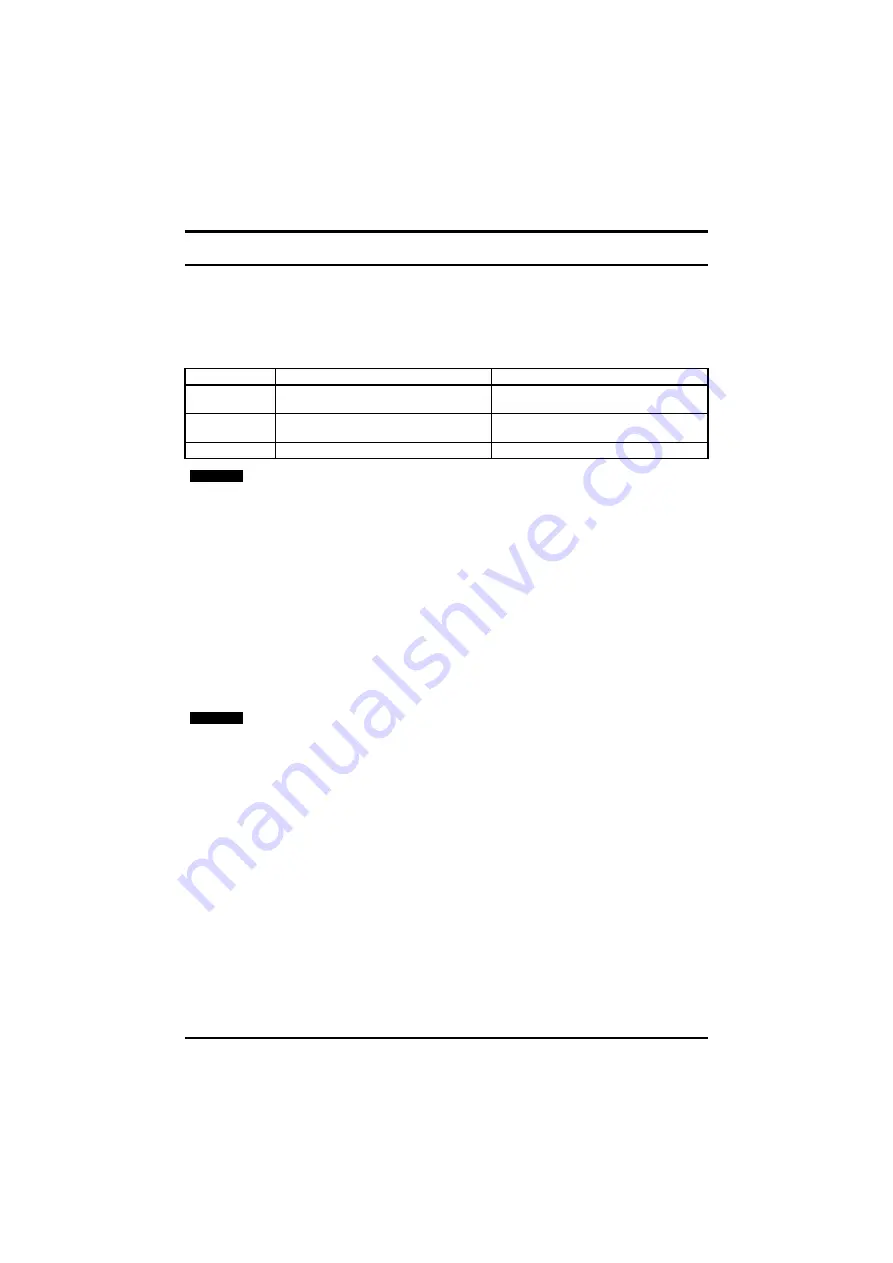
16
SI-EtherCAT User Guide
Issue Number: 2
5
Getting started
5.1
Quick start guide
This section is intended to provide a generic guide for setting up SI-EtherCAT with a master/
controller PLC. It will cover the basic steps required to get cyclic data communicating using the
CANopen over EtherCAT (CoE) protocol on the SI-EtherCAT module.
Table 5-1 PDO test mappings
Due to the large number of different masters that support CoE, details cannot be provided for a
specific master. Generic support is available through your supplier or local Control Techniques
Drive Centre. Before contacting your supplier or local Control Techniques Drive Centre for support
please ensure you have read
on page 94 of this manual and have checked
that the SDO/PDO configurations are correct.
5.1.1
SI-EtherCAT XML file
Control Techniques provides EtherCAT device description files (in the form of .xml files). These files
provide the master with information about the SI-EtherCAT module and drive configuration to aid
with its configuration. These files can be downloaded from the Control Techniques CTSupport.com
website or from your local Control Techniques Drive Centre or supplier. They should be placed in
the directory specified by the master e.g. when using TwinCAT this could be
C:\TwinCAT\Io\EtherCAT.
5.1.2
Configuring the SI-EtherCAT module for cyclic communications
Unlike other Control Techniques fieldbus communication protocols, CoE does not require that any
module parameters be changed in order to achieve communications. The baud rate of the network
is fixed and the module is automatically allocated an address.
To check that the ethernet cable connected to the SI-EtherCAT module on the drive is connected
correctly, look at the LED on the front of the SI-EtherCAT module relating to the connector being
used, if this light is a solid green color then a link is established with the master, if this light if off then
check the cabling and also check that the master has started communications.
In the master, scan the network ensuring that the SI-EtherCAT module is connected correctly to the
master. If the network is configured correctly the SI-EtherCAT node(s) should be visible in the PLC
master.
Decide on the input / output data you wish to send cyclically (objects and/or parameters).
Cyclic data is implemented on CoE networks by using "Process Data Objects" or PDOs. Separate
data objects are used for receiving (TxPDOs - from the slave to the master) and transmitting
(RxPDOs - from the master to the slave) data.
RxPDO1
TxPDO1
Mapping 1
0x6040 (
controlword
)
(16-bits)
0x6041 (
statusword
)
(16-bits)
Mapping 2
0x6042 (
vl_target_velocity
)
(16-bits)
0x6064 (
position_actual_value
)
(32-bits)
Mapping 3
Pr
20.021
(32-bits)
N/A
It is strongly recommended that the latest firmware be used where possible to ensure
that all features are supported.
The master may have to be re-started for the file to be loaded.
NOTE
NOTE
Summary of Contents for SI-EtherCAT
Page 1: ...User Guide SI EtherCAT Part Number 0478 0152 02 Issue Number 2 ...
Page 105: ......
Page 106: ...0471 0152 02 ...