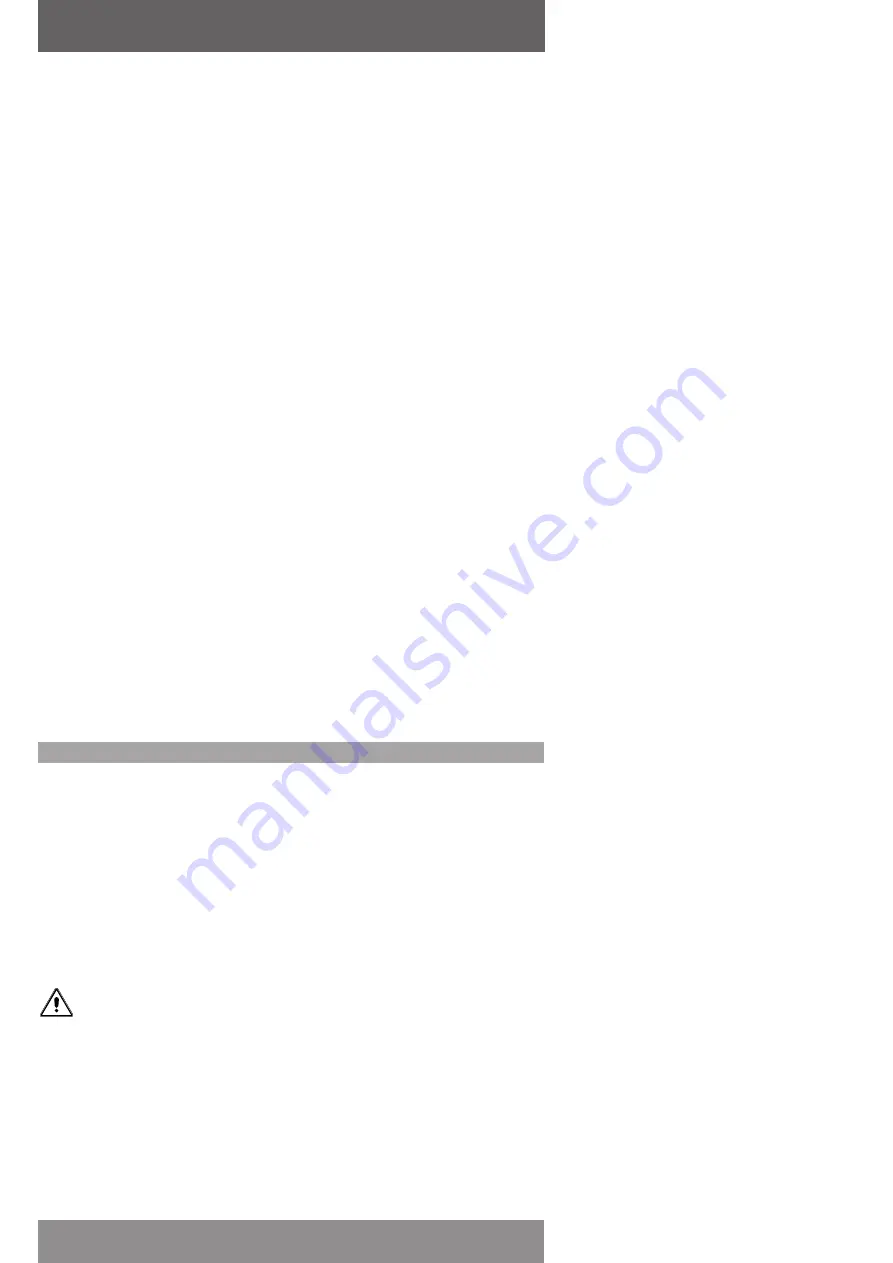
Sapag Safety Valves Series 8400/8500/8490/8590
Installation and Maintenance Instructions
Emerson reserves the right to change the contents without notice
page 16
• Distortion from Piping Strains
Valve bodies can be distorted by excessive piping loads causing seat leakage. Both inlet and
discharge piping must be properly supported and anchored so that high bending loads are not
transmitted to the valve body.
• Operating Pressure Too Close to Set Pressure
A carefully lapped metal-to-metal seated valve will be commercially tight at a pressure
approximately ten percent under the set pressure or 5 PSI, whichever is greater. Consequently,
this minimum pressure differential should be maintained between set and operating pressure to
avoid seat leakage problems.
• Chatter
Oversized valves, excessive pressure drop in the inlet lines, restrictions in the inlet line, too great
a build up of back pressure or pulsating inlet pressure will cause instability to the pressure relief
valve. In such installations, the pressure under the valve disc may be great enough to cause
the valve to open, but as soon as flow is established, the pressure drops allowing the valve to
immediately close. This cycle of opening and closing sometimes occurs at very high frequency
causing severe seat damage, sometimes beyond repair.
Proper valve selection and installation techniques are paramount to reliable valve performance.
• Incorrectly Adjusting Lifting Gear
A space of 1/16 inch minimum should always be provided between the lifting device and the
spindle lift nut. Failure to provide sufficient clearance may result in inadvertent contact causing a
slight shift in the opening pressure.
• Other Causes of Seat Leakage
Improper alignment of the spindle, too much clearance between the valve spring and the spring
washers, or improper bearing contact between the adjusting bolt and the spring washers, spindle
and disc holder or spindle and lower spring washer may cause seat leakage problems. Spindles
should be checked for straightness and springs and spring washers should be properly fitted and
kept together as a spring assembly.
• Corrosion
Corrosion may result in pitting of valve parts, failure of various valve parts, build up of corrosive
products and general deterioration of the valve materials.
Corrosive attack is generally controlled through selection of suitable materials or by employing
a bellows seal to isolate the valve spring, adjusting bolt, spindle and guiding surfaces from the
corrosive attack of the process fluid.
Environmental corrosion attacks all exposed surfaces, including studs and nuts. In general, the
materials required for a particular service are dictated by the temperature, pressure and the degree
of corrosion resistance required.
11. Emerson Valves & Controls field service and repair programs field service
Emerson Valves & Controls Field Service provides on-site, in line testing and repair capability for all
types of pressure relief devices.
• Parts
Emerson Valves & Controls will help you establish the right mix of on-site spares with Emerson Valves
& Controls’ own distribution and manufacturing support.
• Training
Emerson offers intensive factory or on-site seminars to improve maintenance and application skills.
• Testing
Emerson Valves & Controls has the capability to evaluate pressure relief valve operability either in
the field or at various Emerson Valves & Controls facilities. Special qualifications programs may also
be conducted in our laboratories.
• Contract Management
Emerson Valves & Controls will combine a group of services to satisfy your special maintenance
needs.
WARNING
The Product is a safety related component intended for use in critical applications. The improper
application, installation or maintenance of the Product or the use of parts or components not
manufactured by
Emerson
may result in failure of the Product. The advice of a qualified engineer
should be sought prior to any use of the Product.
Any installation, maintenance, adjustment, repair or test performed on the Product must be done
in accordance with the requirements of all applicable Codes and Standards.
The information, specifications and technical data (the “Specifications”) contained in this
document are subject to change without notice.
Emerson
does not warrant that the
Specifications are current and assumes no responsibility for the use or misuse thereof.
The Purchaser should verify that there have been no changes to the Specifications prior to use.