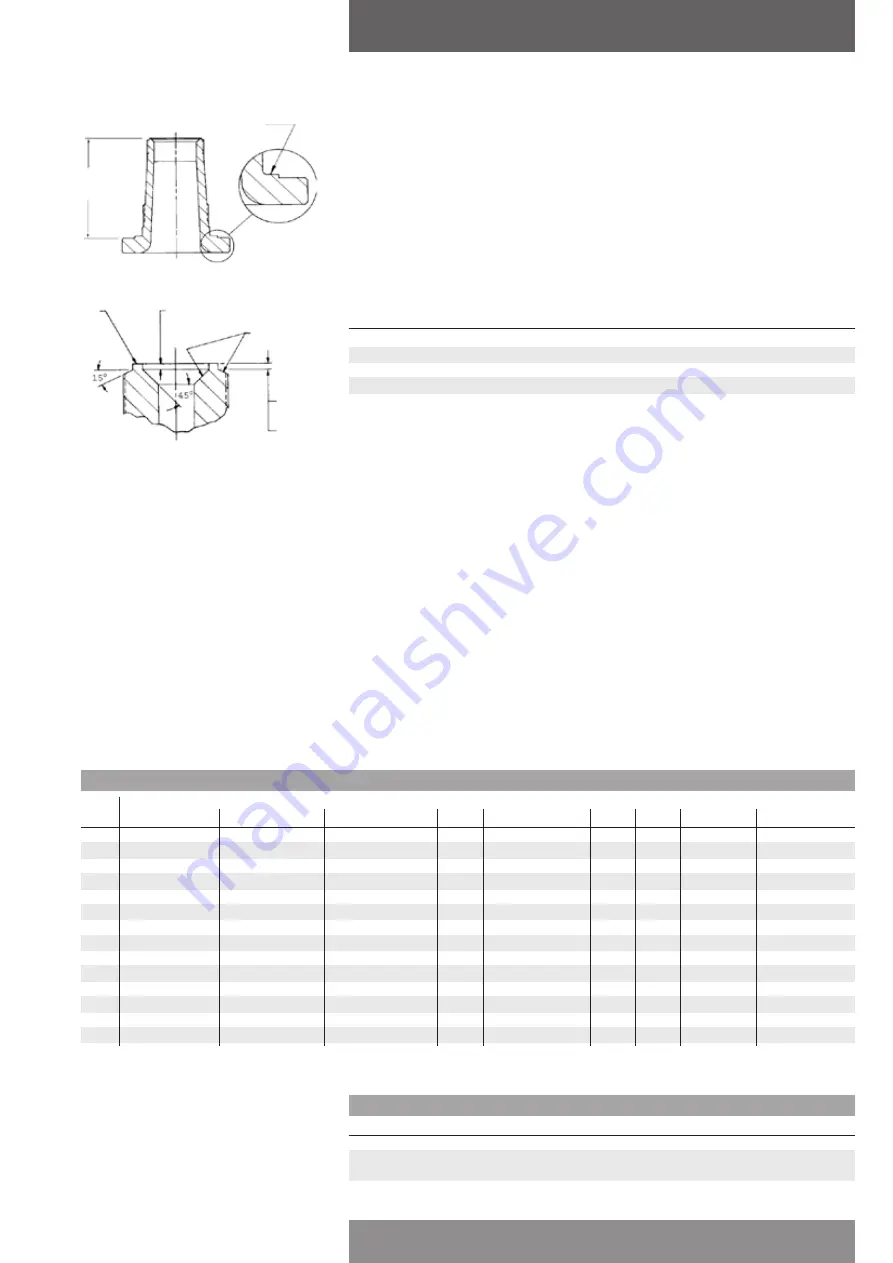
D
3,465
3,465
3,465
3,465 3,465
3,687 3,687 3,687
4,808
E
3,465
3,465
3,465
3,465 3,465
3,687 3,687 3,687
4,808
F
4,027
4,027
4,027
4,027 4,027
4,027 4,027 4,027
4,647
G
3,777
3,777
3,777
3,777 3,777
3,777 3,777 4,777
4,777
H
3,903
3,903
3,903
3,903
4,840
4,840
4,840
4,840
-
J
4,340
4,340
4,340
4,340
5,121
5,121
6,455
6,455
-
K
4,715
4,715
4,715
4,715
5,840
5,840
7,027
7,027
-
L
5.059
5.059
5,277
5,277
5,277
6,250
6,250
6,250
-
M
5,59
5,59
5,59
5,59
5,59
6,403
6,403
-
-
N
6,121
6,121
6,121
6,121
6,121
-
-
-
-
P
5,871
5,871
7,621
7,621
7,621
-
-
-
-
Q
7,746
7,746
7,746
7,746
7,746
-
-
-
-
R
8,121
8,121
8,121
8,121
8,121
-
-
-
-
T
9,59
9,59
9,59
-
9.590 (*)
-
-
-
-
“A”
0,332 0,370 0,369 0,398 0,429 0,531 0,546 0,605 0,632 0,692 0,783 0,781 0,839
“B”
0.021 0.025 0.030 0.036 0.044 0.051 0.063 0.070 0.076 0.091 0.118 0.139 0.176
0.023 0.027 0.032 0.038 0.046 0.053 0.065 0.072 0.078 0.093 0.120 0.141 0.178
Sapag Safety Valves Series 8400/8500/8490/8590
Installation and Maintenance Instructions
Emerson reserves the right to change the contents without notice
page 11
• Lapping Blocks
Lapping blocks are made of a special grade of annealed cast iron. There is a block for each orifice
size. Each block has two perfectly flat working sides and it is essential that they retain this high
degree of flatness to produce a truly flat seating surface on either the disc insert or the nozzle.
Before a lapping block is used, it should be checked for flatness and reconditioned after use on
a lapping plate. The block should be lapped in a figure eight motion, applying uniform pressure
while rotating the lapping block against the plate as shown in Figure 9.
• Lapping Compounds
Experience has proven that medium coarse, medium fine, and polish lapping compounds will
properly condition any damaged pressure relief valve seat except where the damage requires
remachining. The following lapping compounds, or their commercial equivalents are suggested:
Grit Compound No.
Description
320
Medium Coarse
400 Medium
600 Fine
900 Polish
• Machining of Nozzle Seats
If machining of the nozzle seat or other major repairs are necessary it is recommended that the
valve be returned to a Emerson Valves & Controls facility for repair. All parts must be accurately
machined per Sapag specifications. No pressure relief valve will be tight, nor will it operate
properly unless all parts are correctly machined. The most satisfactory way to machine a nozzle is
to remove it from the valve body. However, it may also be machined while assembled within the
valve body.
In any event it is vitally important that the seating surfaces run absolutely true before machining.
Machining dimensions for Sapag Series 8000 valves with metal-to-metal nozzle seats are shown in
Figure 10 and Table 8. Remove only enough metal to restore the surface to its original condition.
Turning to the smoothest possible finish will facilitate lapping.
The nozzle must be replaced when minimum face to seat dimension is reached. This critical
dimension is shown in Table 8.
• Machining of Disc Insert Seats
When the damage to the disc insert seat is too severe to be removed by lapping, the disc insert
may be machined and lapped provided that minimum seat height is maintained (Figure 11 and
table 9).
Table 8 - Minimum nozzle face to seat dimensions (See Figure 10)
Valve Type
Orifice 12, 13, 14, 15,16
22, 23, 24, 25, 26
32, 33, 34, 35, 36, 37 47
42, 43, 44, 45, 46
57
55, 56
65, 66, 67
75, 76, 77
* Type 42,43,44 not available
Raised seal face
Minimum face
to seat dim,
refer to Table 8
Seat
.004 after lapping
.010-.014
machined
.008 min
after
lapping
Figure 10 - Nozzle seat critical
dimensions
related
surfaces
Table 9 - Disc insert minimum seat heights
Orifice D & E
F
G
H
J
K
L
M
N
P
Q
R
T