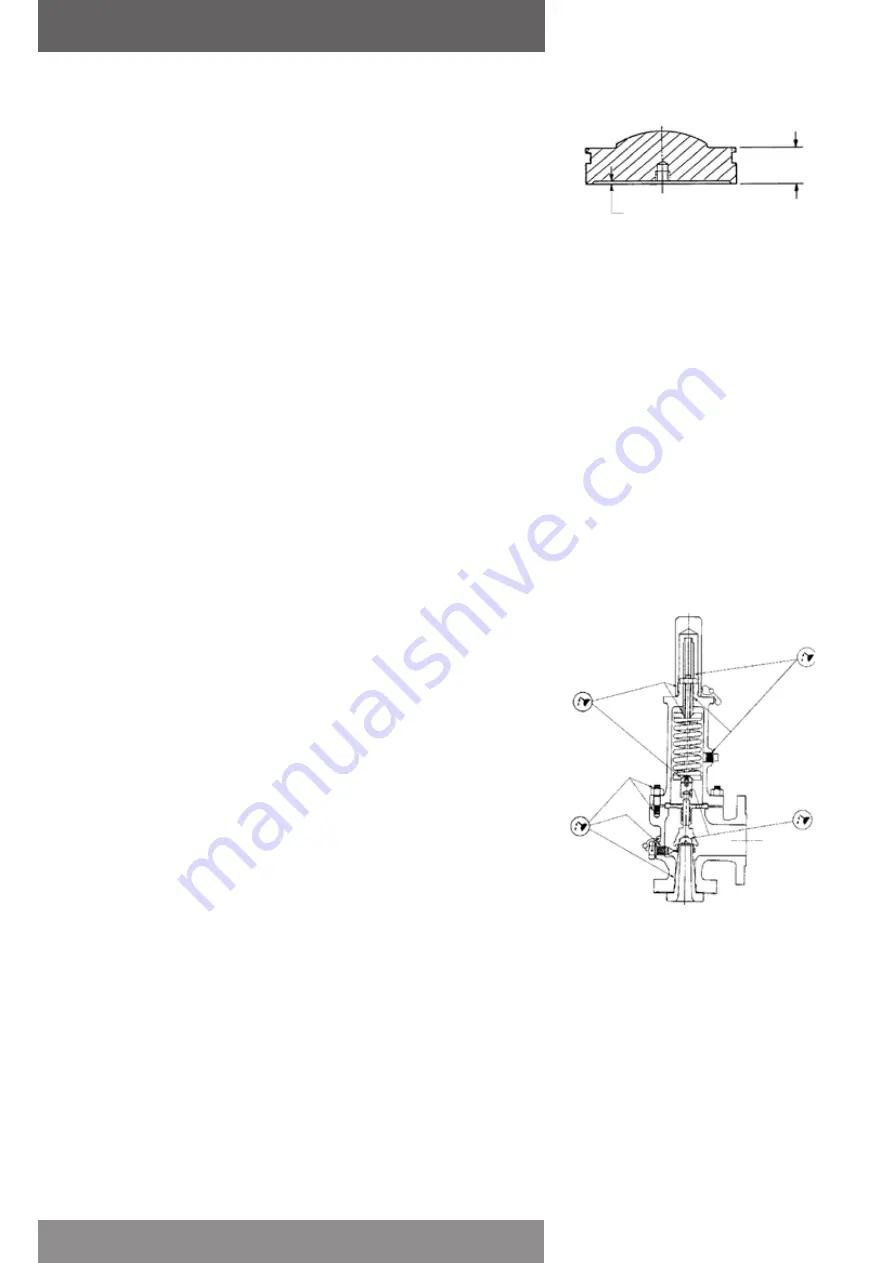
Sapag Safety Valves Series 8400/8500/8490/8590
Installation and Maintenance Instructions
Emerson reserves the right to change the contents without notice
page 12
Figure 12 - Recommended lubrication
points
Assembly
All components should be clean. Before assembling the following parts, lubricate with pure nickel
“Never-Seez”.
• Nozzle and body threads
• Nozzle and body sealing surface
• All studs and nut threads
• Spindle and threads
• Set screw threads
• Spring washer bevels
• Adjusting bolt and bonnet threads
• Bonnet pipe plug
• Cap threads
• Dog shaft bearing threads
• Disc holder threads (bellows valves only)
Lubricate the spindle point thrust bearing and disc insert bearing with pure nickel “Never-Seez”.
Special attention should be given to the guiding surfaces, bearing surfaces and gasket surfaces to
ensure that they are clean, undamaged and ready for assembly. (Figure 12)
For parts identification, refer to Figure 1.
a. Before installing the nozzle (2) apply lubricant to the flange surface in contact with the valve
body (1) and on the body to nozzle threads. Screw the nozzle (2) into the valve body (1) and
tighten with a nozzle wrench.
b. Screw the nozzle ring (3) onto the nozzle (2).
Note:
The top of the nozzle ring should be above the nozzle seating surface. For P, Q, R and T
Orifice Style 8500/8590, position the nozzle ring per table 2.
c. For bellows valves only, place the disc holder in a vise (larger sizes may require a 3 jaw vise) as
shown in Figure 8. Install the tailpiece gasket (29).
Screw the bellows assembly onto the disc holder. Tighten with a suitable wrench.
d. Assemble the disc insert (8) and the disc holder (5).
(See page 15 for O-ring soft seat assembly)
Install the disc insert retention clip (9) onto the disc insert.
Install the disc insert into the disc holder. The disc insert should snap into place using hand
force only.
Safety precautions should be followed whenever heavy parts are being lifted or transported.
Dropping disc holder assembly may dislodge the insert.
e. Assemble the disc holder (5) and guide (15) by sliding the guide over the disc holder.
Note:
The guide for D and E orifice valves protrudes up into the valve bonnet.
f. Install the two guide gaskets (28), one above and one below the guide.
Note:
When assembling bellows valves, the bellows flange eliminates the need for a bottom
guide gasket.
g. While holding the top of the disc holder, install the guide into the body. Align the hole of the
guide with the body outlet. Once the guide is seated, the disc holder and disc insert can be
lowered onto the nozzle.
Note:
Lower the nozzle ring below the seats so that it moves freely.
h. Place the spring (18) and washers (19) onto the spindle (16) and assemble the spindle to the disc
holder (5) with the spindle cotter pins.
Note:
No cotter pins are required in D through K orifice sizes all other orifice sizes use two
cotter pins.
i. Lower the bonnet (20) over the spindle and spring assembly onto the bonnet studs (21) in the
body. Position the bonnet counter bore on the O.D. of the guide and lower the bonnet onto the
guide.
j. Screw the bonnet nuts (22) onto the bonnet studs and tighten down evenly to prevent
unnecessary strain and possible misalignment.
k. Screw the adjusting bolt (24) and nut (25) into the top of the bonnet to apply force on the
spring. (The original set pressure can be approximated by screwing the adjusting bolt down to
the predetermined measurement.)
l. Move the nozzle ring up until it touches the disc holder, then lower it two notches. This is a test
stand setting only.
m. Place the set screw gasket (27) onto the set screw (4) and screw the set screw into the body
engaging the nozzle ring. The nozzle ring should move back and forth slightly after the set
screw is tightened.
n. The valve is now ready for testing.
After testing, the following measures should be taken:
• Be sure that adjusting bolt nut (25) is locked.
• Return the nozzle ring to either the original recorded position or to the recommended position
shown in Table 1.
• Install the cap or lifting device. See Figure 13 for lifting lever assembly.
• Seal the cap or lifting lever device and nozzle ring set screw to prevent tampering.
“A” min.
after lapping
“B” mach.
Figure 11 - Disc Insert Minimum Seat
Height (Table 9)