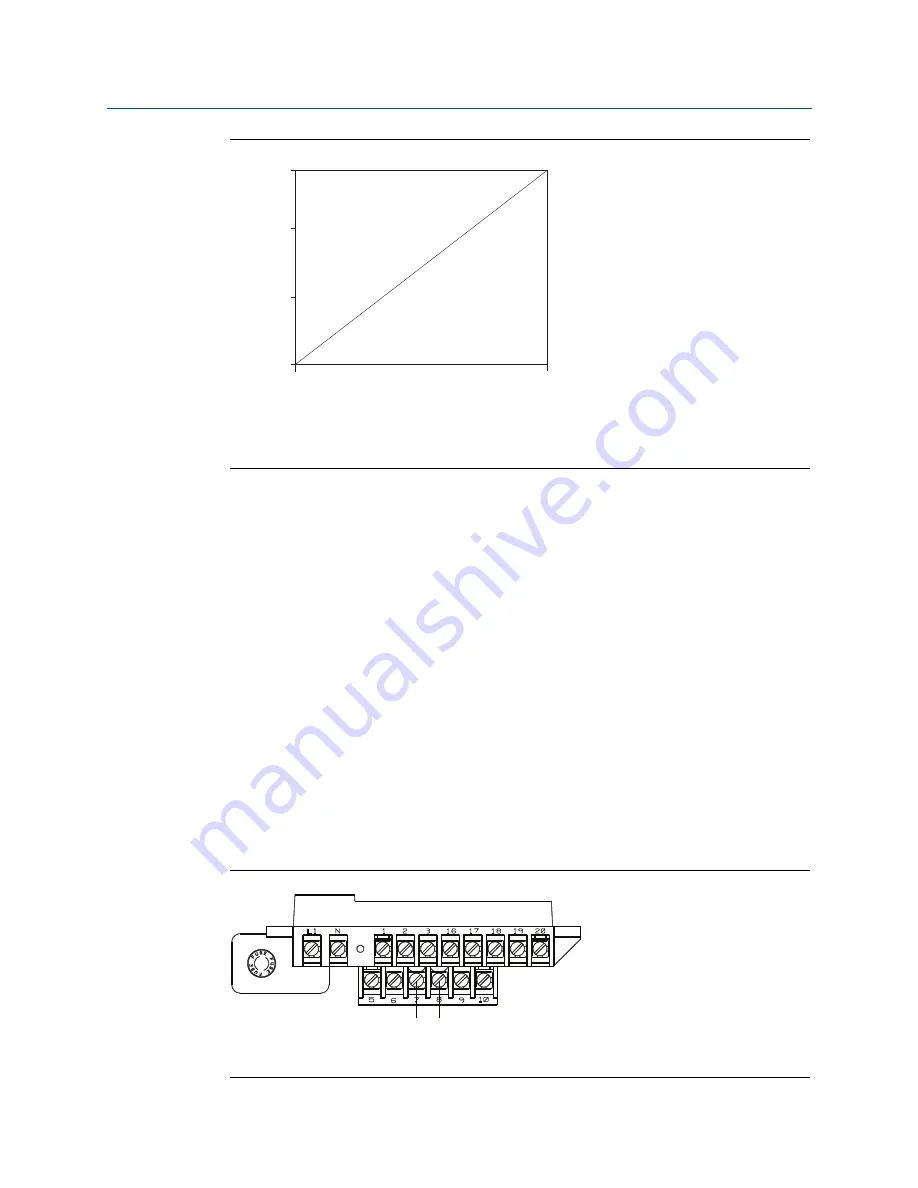
27
Reference Manual
00809-0300-4750, Rev CA
Quick Installation and Start-Up
March 2016
Quick Installation and Start-Up
Figure 2-27. Field Mount Transmitter Analog Loop Load Limitations
R
max
= 31.25 (V
ps
— 10.8)
V
ps
= Power supply voltage (Volts)
R
max
= Maximum loop resistance (Ohms)
Wall mount transmitter
The analog output signal is a 4—20mA current loop. The loop can be powered internally or
externally via a hardware switch. The switch is set to internal power when shipped from the
factory.
For HART Communication a minimum resistance of 250 ohms is required. It is
recommended to use individually shielded twisted pair cable. The minimum conductor size
is 0.51 mm diameter (number 24 AWG) for cable runs less than 5,000 ft. (1,500 m) and
0.81 mm diameter (number 20 AWG) for longer distances.
Internal power
The 4—20mA analog signal is a 24 VDC active output.
Maximum allowable loop resistance is 500 ohms.
External power
The 4—20 mA analog signal is powered from an external power source. HART multidrop
installations require a 10—30 VDC external analog power source.
Figure 2-28. Wall Mount Transmitter Analog Wiring
A. +4–20 mA
B. -4–20 mA
600
400
200
0
10.8
30
Operating
region
Power supply (Volts)
Load (Ohms)
A B
Summary of Contents for Rosemount 8750W
Page 2: ......
Page 96: ...84 Reference Manual 00809 0300 4750 Rev CA Operation March 2016 Operation ...
Page 168: ...156 Reference Manual 00809 0300 4750 Rev CA Maintenance March 2016 Maintenance ...
Page 214: ...Wiring Diagrams March 2016 Reference Manual 00809 0300 4750 Rev CA 202 Wiring Diagrams ...
Page 218: ...Wiring Diagrams March 2016 Reference Manual 00809 0300 4750 Rev CA 206 Wiring Diagrams ...
Page 219: ...Wiring Diagrams March 2016 Reference Manual 00809 0300 4750 Rev CA 207 Wiring Diagrams ...
Page 220: ...Wiring Diagrams March 2016 Reference Manual 00809 0300 4750 Rev CA 208 Wiring Diagrams ...
Page 222: ...Wiring Diagrams March 2016 Reference Manual 00809 0300 4750 Rev CA 210 Wiring Diagrams ...
Page 223: ...Wiring Diagrams March 2016 Reference Manual 00809 0300 4750 Rev CA 211 Wiring Diagrams ...
Page 224: ...Wiring Diagrams March 2016 Reference Manual 00809 0300 4750 Rev CA 212 Wiring Diagrams ...
Page 225: ...Wiring Diagrams March 2016 Reference Manual 00809 0300 4750 Rev CA 213 Wiring Diagrams ...
Page 227: ...Wiring Diagrams March 2016 Reference Manual 00809 0300 4750 Rev CA 215 Wiring Diagrams ...
Page 228: ...Wiring Diagrams March 2016 Reference Manual 00809 0300 4750 Rev CA 216 Wiring Diagrams ...
Page 229: ...Wiring Diagrams March 2016 Reference Manual 00809 0300 4750 Rev CA 217 Wiring Diagrams ...
Page 263: ......