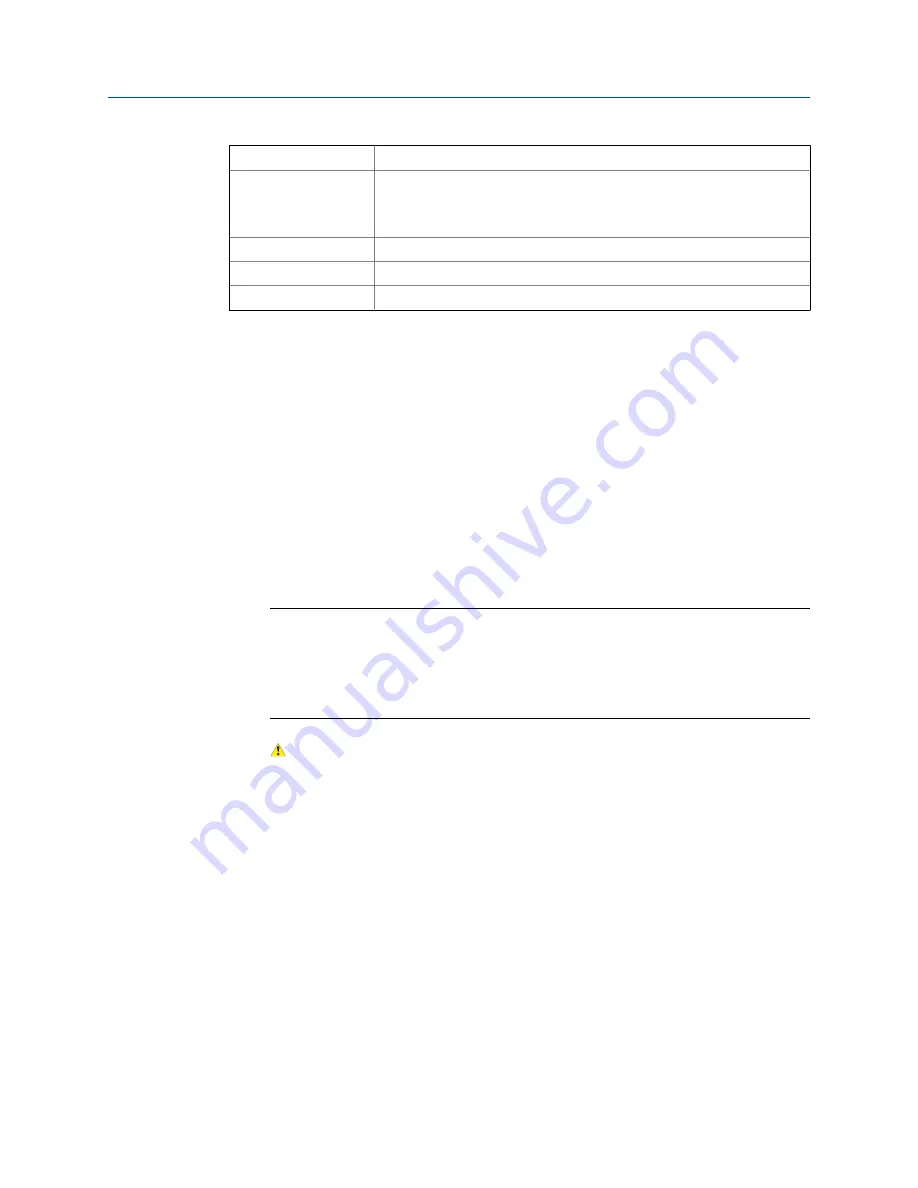
Temperature
–50 °C to 200 °C (–58 °F to 392 °F)
Flow
40 to 330 l/min
2.5 to 20 m3/hr
11 to 87 US gal/min
Viscosity
Up to 100 cSt
Pressure
As defined by process flanges
Calibration boundary
2.5 in Schedule 40
Procedure
1.
Check that the isolation valves are fully closed.
2.
Remove insulation and allow the equipment to cool to a safe level.
Cooling reduces retained pressure.
3.
If you have a drain or a pressure-relieving valve, depressurize the system.
4.
Slacken the lock nut 1
½
to 2 turns so that you can rock the sensor.
If necessary, use your hand to jolt the meter loose from the amplifier housing. This
breaks the seal between the sensor and the chamber retrofit kit. Do not slacken the
lock nut further unless the seal is broken and the sensor is obviously loose in the
fitting.
Note
If the system is still pressurized, you'll be able to lift and hold the meter against the retaining
nut. Rocking and alternately pushing the sensor in and out of the pocket within the limits
allowed by the slackened nut breaks the seal and allows oil under pressure to seep past the
lock nut. If this leakage is excessive, re-tighten the lock nut and take further action to
depressurize the system.
5.
CAUTION!
Keep all parts of your body away from the direction in which you'll remove the sensor.
Pressure caused by a valve failure or a poorly placed lock nut can eject the instrument
from the flow chamber and cause serious injury.
Remove the lock nut if you can rock the meter in the flow chamber, and there is no
serious or continuous escape of oil.
6.
Retrofit the meter per the following diagram.
Mounting
16
Micro Motion Heavy Fuel Viscosity Meter