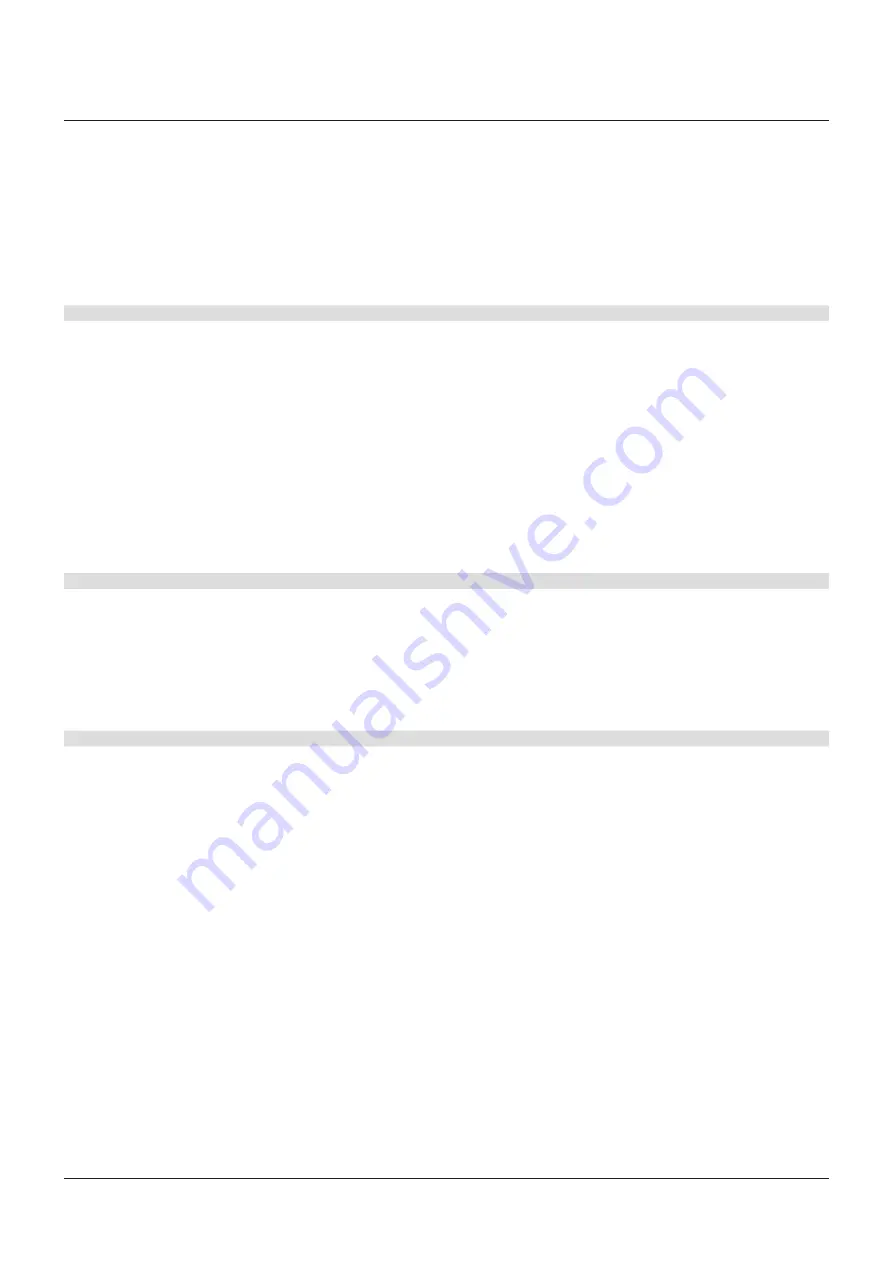
11
8.2.1 Positioning algorithm
a positioning algorithm (position closed loop control) is implemented on the DeviceNet interface module.
the positioning function consists of comparing the position, received from the base card, with the position request received from bus. If the
difference between ‘position request and present position’ is greater than ‘Dead Band’ an Open or a close command is send to base card. the
dead Band is configurable via bus from 0.3 to 2.0%.
8.3 fail safe data
the fail Safe data parameter defines the behavior of the actuator in case of network communication failure. the fail Safe data parameter can be
modified via DeviceNet network.
Indication
description
direction
data type
range
default
e.u.
parameter 1: class 100; Instance 1; attribute 100
Safety action
the action to execute in case of loss of bus communication.
0 = No action
1 = close
2 = Open
3 = Stop
4 = go to predefined position
r/W
Integer
0-4
0
-
parameter 2: class 100; Instance 1; attribute 101
Predef. safety position
Safe predefined position
r/W
Integer
0-100
50
%
parameter 3: class 100; Instance 1; attribute 102
Delay on bus fail
Delay before to initiate the safety action
r/W
Integer
0-10
4
sec
8.4 dead band configuration
the Dead Band indicates the maximum allowed deviation from the valve position and the requested position. If the deviation is bigger, an open or
close control command will be generated.
Indication
description
direction
data type
range
default
e.u.
parameter 4: class 100; Instance 1; attribute 103
Dead band
this parameter defines the Dead Band of the positioning function
available on the modulating actuator (in tenth of %).
the movement is inhibited until the difference between current position
and requested position (position error) is lower than Dead Band.
r/W
Integer
3-20
15
0.1%
8.5 user defined data
the User defined data is stored in the EPI2 actuator and is available on the DeviceNet network for asset Management information.
Indication
description
direction
data type
range
default
e.u.
parameter 5: class 100; Instance 1; attribute 104
actuator serial number
actuator serial number
Only read Short string
12 bytes
-
-
parameter 6: class 100; Instance 1; attribute 105
actuator type
actuator type
Only read Short string
12 bytes
-
-
parameter 7: class 100; Instance 1; attribute 106
valve tag
valve tag
Only read Short string
12 bytes
-
-
Keystone
OM11 - EPI2 DEvIcENEt INtErfacE
InstallatIon and maIntenance InstructIons