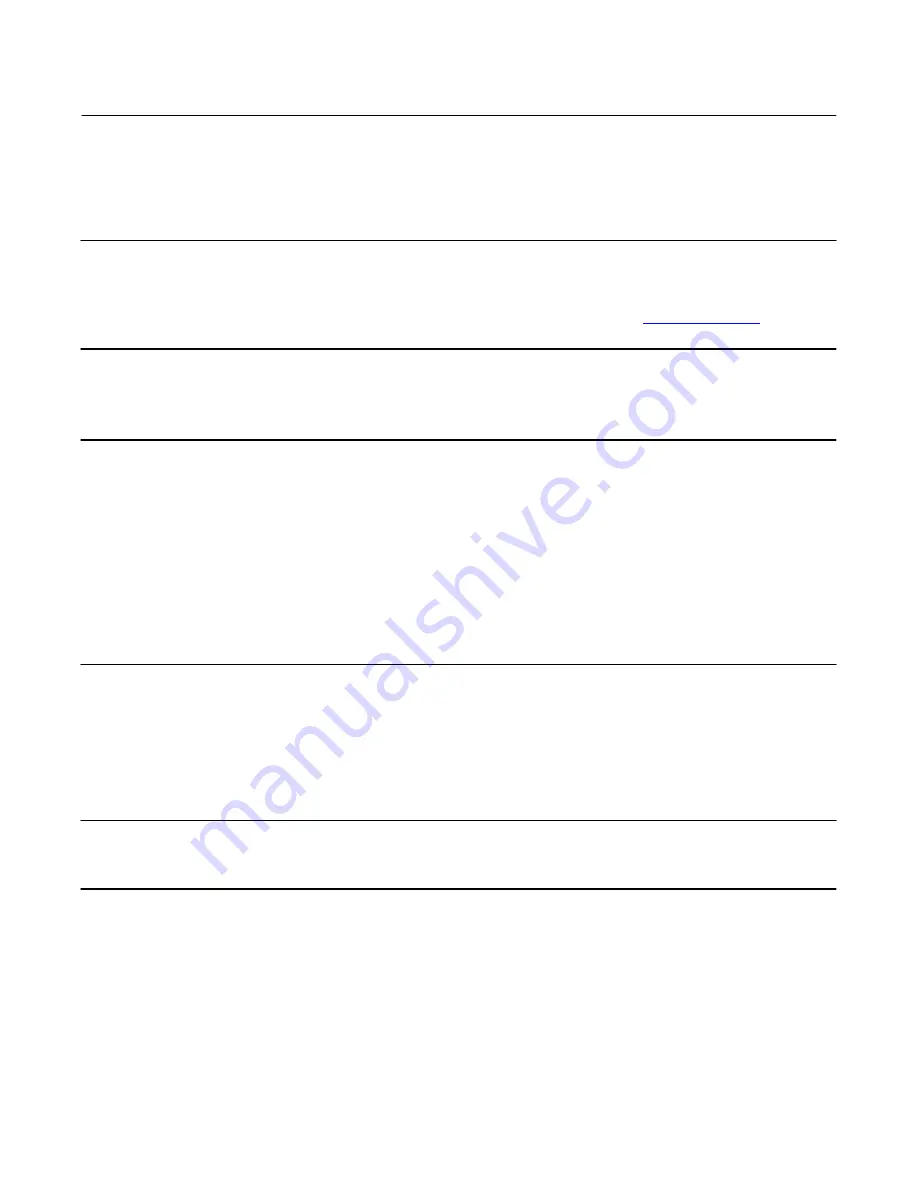
Instruction Manual
D500242X012
A31A Cryogenic-Rotary Valve
February 2019
17
2. Secure the valve in an upright position. Rotate the disk (key 3) 180 degrees counterclockwise from the fully closed
position by manually turning the drive shaft.
Note
Class 150 and 300 3‐ through 24‐inch valve sizes have a bearing stop pressed into the bearing bore of the valve body below the
extension housing.
Do not attempt to remove the bearing stop. If the bearing stop needs replacement, contact your
for more
information.
4. Remove the packing from around the drive shaft.
Note
Different valves require slightly different procedures because different valve sizes/ pressure classes have different methods of
connecting the disk and shaft(s). To identify the proper procedures, refer to the list below.
D
Class 150, 3‐ through 8‐inch sizes: One‐piece shaft with 1 taper key.
D
Class 150, 10‐ and 12‐inch sizes: Two‐piece shaft. 1 taper key in the drive shaft; 1 disk pin in the follower shaft.
D
Class 300, 3‐ through 6‐inch sizes: One‐piece shaft with 1 taper key.
D
Class 300, 8‐ and 10‐inch sizes: Two‐piece shaft. 1 taper key in the drive shaft; 1 disk pin in the follower shaft.
D
Class 300, 12‐inch size: Two‐piece shaft with 2 tangential pins in the drive shaft; 1 disk pin in the follower shaft.
D
Class 150 and 300, 14‐ through 24‐inch sizes: Two‐piece shaft with 2 tangential pins in the drive shaft; 1 disk pin in the
follower shaft.
5. Proceed as appropriate, using the following instructions.
For valves with taper key(s),
locate the taper key(s) (key 6) which runs through the drive shaft boss on the back of the
valve disk. Using a pin punch on the smaller end of the key, drive it out of the disk and shaft. Driving a taper key in the
wrong direction will tighten it.
Note
Certain valve sizes may have a taper key that is arc spot welded in place. To remove the key, use a punch on the smaller end of the
taper key and drive it out of the disk and shaft, breaking the weld.
For valves with tangential pins and/or disk pins,
locate the tangential pins (key 6) in the drive shaft (key 4) and the disk
pin (key 6) in the follower shaft (key 5).
a. If a maintenance kit is available, use the pin extractor to remove the disk pins. Select the correct size pin extractor
tip with screws of proper thread size to match the thread size in the disk pins. If a maintenance kit is not
available, see steps c and d below.
b. Screw the pin extractor tip into the pin as far as possible. With an upward, straight sliding motion, pull out the
pin. Repeat the same procedure for the other pins.