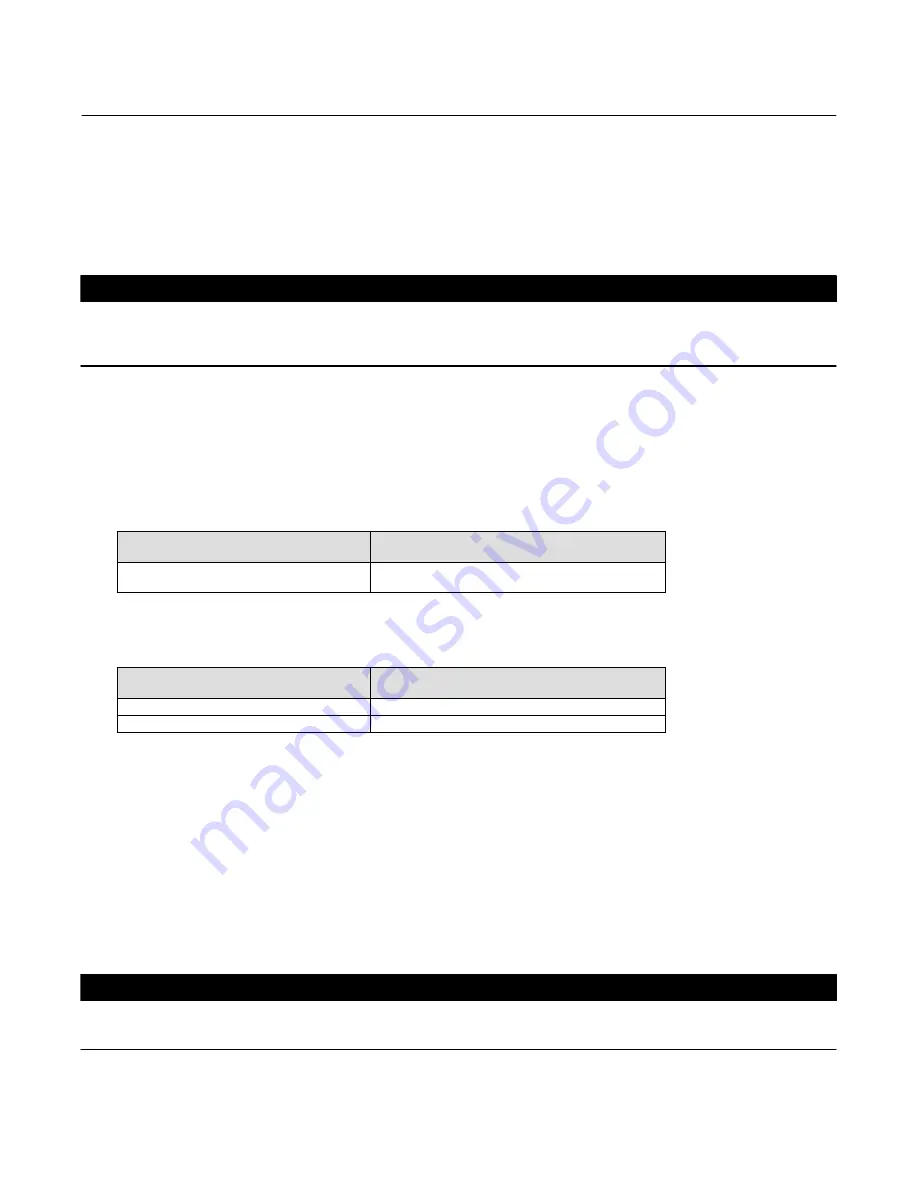
Instruction Manual
D500242X012
A31A Cryogenic-Rotary Valve
February 2019
19
5. Insert the outboard journal bearing (key 10) into the bore on top of the extension housing.
6. Install the valve disk by placing the disk into the valve body bore so the curved side of the disk passes through the
end of the valve body that does not contain the T‐slot. Align the shaft bore in the disk with the bearing bores.
7. Insert the drive shaft end opposite the double D or keyed end into the valve body through the packing box. Push the
shaft through the bearing stop. Taking care not to dislodge the journal bearing, push the shaft through the journal
bearing and the valve disk and into the bore on the opposite side of the valve body.
CAUTION
To avoid damage to the taper key, tangential pins, disk pins, valve disk, or shaft(s) resulting from the application of
excessive force, use appropriate care when driving the key or pins into the disk hub and shaft(s). Use the right tool. Do not
use excessive force.
8. Be sure the taper key disk shaft joint is free of oil or grease. If necessary, remove any excess welding material from
the taper key.
9. Align the taper key hole in the shaft with the holes in the shaft boss on the disk. Insert the taper key. Use a flat‐end
punch to drive the taper key until solid contact is felt. Measure the depth of the taper key head for a reference
during the following steps.
a. Drive the taper key in farther as follows:
Valve Size, Inches
Minimum Depth to Drive Taper key
After Initial Solid Contact, mm (Inches)
ANSI Class 150 and 300, size 3, 4, 6‐inch valves,
and 8‐inch ANSI Class 150 valves
5 (0.188)
b. The disk, shaft, and taper key assembly must be inspected to verify that the taper key spans the entire shaft flat
width. If so, this procedure is complete. If not, the taper key must be driven in farther until this condition is
satisfied. However, do not exceed the following depth limits:
Valve Size, Inches
Maximum Allowable Depth to Drive Taper key
After Initial Solid Contact, mm (Inches)
3, and 4‐inch ANSI Class 150/300
7 (0.281)
6‐inch ANSI Class 300, and 8‐inch ANSI Class 150
8 (0.312)
10. After driving the taper key in place, arc spot weld the head of the taper key to the disk. For valve sizes 3‐, 4‐, and
6‐inch, use an arc spot weld bead of 1/8‐inch diameter. For valve sizes 8‐, 10‐, and 12‐inch sizes, use an arc spot
weld bead of 3/16‐inch diameter.
11. Install the packing as described in the Packing Replacement section.
Installing a Two‐Piece Shaft
Unless otherwise indicated, key numbers and part names are listed in figures 7 and 8.
1. Secure the valve in an upright position. Allow for easy access to the valve body bore. Allow for easy access to the
drive shaft bearing bore and the follower shaft bearing bore.
2. Inspect all parts removed from the valve for wear or damage. Replace any worn or damaged parts. Clean the valve
body and all parts to be installed with an appropriate solvent or degreaser.
CAUTION
Premature valve failure and loss of process control may result if bearings are improperly installed or are damaged during
installation.