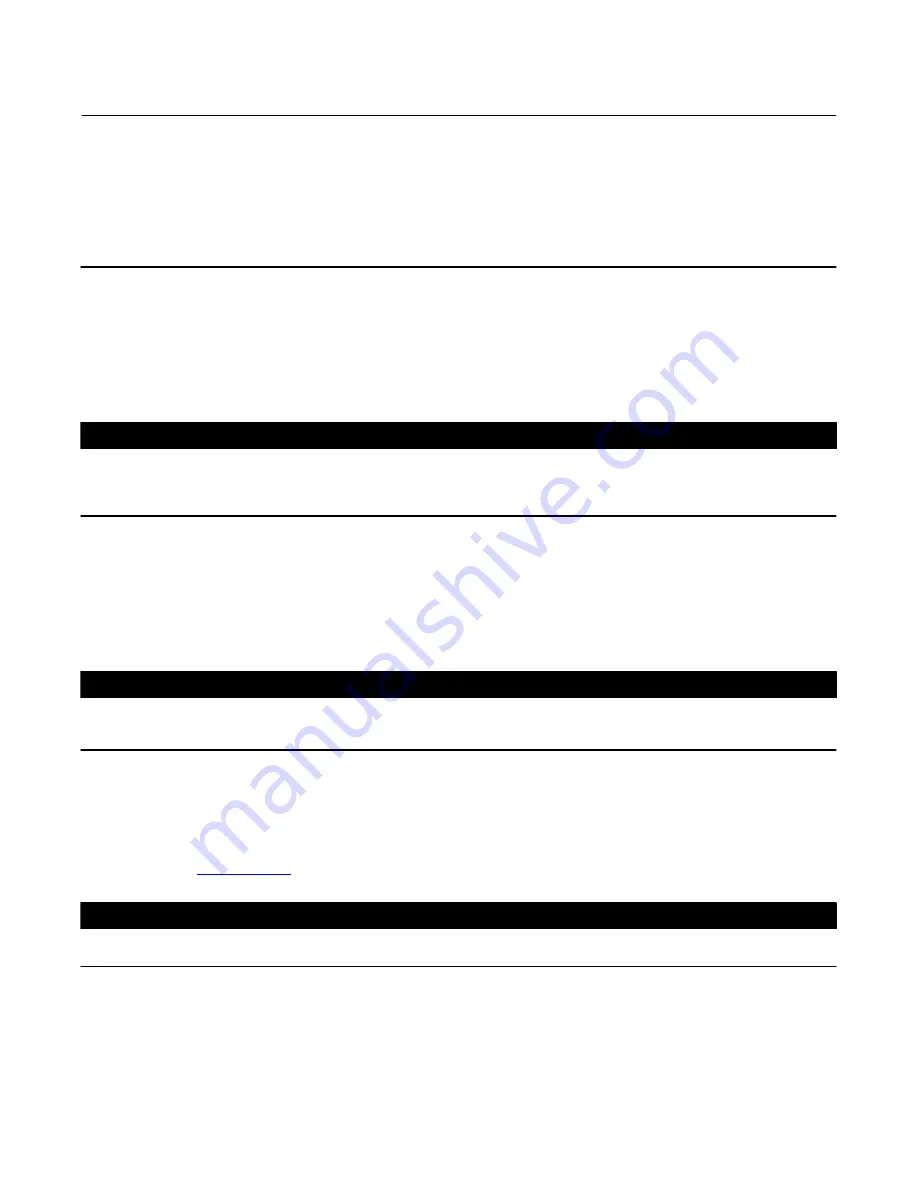
Instruction Manual
D101550X012
8532 Valve
June 2017
12
D
Vent the power actuator loading pressure.
D
Use lockout procedures to be sure that the above measures stay in effect while you work on the equipment.
D
The valve packing box may contain process fluids that are pressurized,
even when the valve has been removed from the
pipeline.
Process fluids may spray out under pressure when removing the packing hardware or packing rings, or when
loosening the packing box pipe plug.
D
Check with your process or safety engineer for any other hazards that may be present from exposure to process media.
Removing and Replacing the Actuator
Refer to the appropriate actuator instruction manual for actuator removal and replacement procedures. The actuator
stops or travel stops must limit the rotation of the valve shaft. See the
CAUTION
below.
CAUTION
When using an actuator, the actuator travel stop (or actuator travel, for actuators without adjustable stops) must be
adjusted so the disk stop in the valve does not absorb the output of the actuator. Failure to limit the actuator travel can
result in damage to the valve, shaft(s), or other valve components.
Packing Maintenance
The 8532 control valve is designed so the packing can be replaced without removing the valve from the process
pipeline.
CAUTION
For non‐ENVIRO‐SEAL packing: Tighten the packing follower nuts only enough to prevent shaft leakage. Excessive
tightening will accelerate wear of the packing and could produce higher friction loads on the valve stem.
Usually, packing leakage can be eliminated by merely tightening the hex nuts (key 15) located above the packing
follower (key 11) while the valve is in the pipeline. However, if leakage continues, the packing must be replaced.
For PTFE ENVIRO‐SEAL packing systems, refer to the separate instruction manual,Fisher ENVIRO‐SEAL Packing System
for Rotary Valves (
D101643X012
)
(see figure 11).
CAUTION
Never use a wrench or pliers on the splined (upper) shaft (key 3). A damaged shaft could cut the packing and allow leakage.
1. Before loosening any parts on the valve, release the pressure from the pipeline. Then, remove the hex nuts (key 15)
and lift off the packing follower (key 11).
2. Remove the hex jam nuts (key 17) and the anti‐blowout flange (key 10). Remove the packing follower (key 12).
Refer to figure 7 for details of the anti‐blowout design parts.