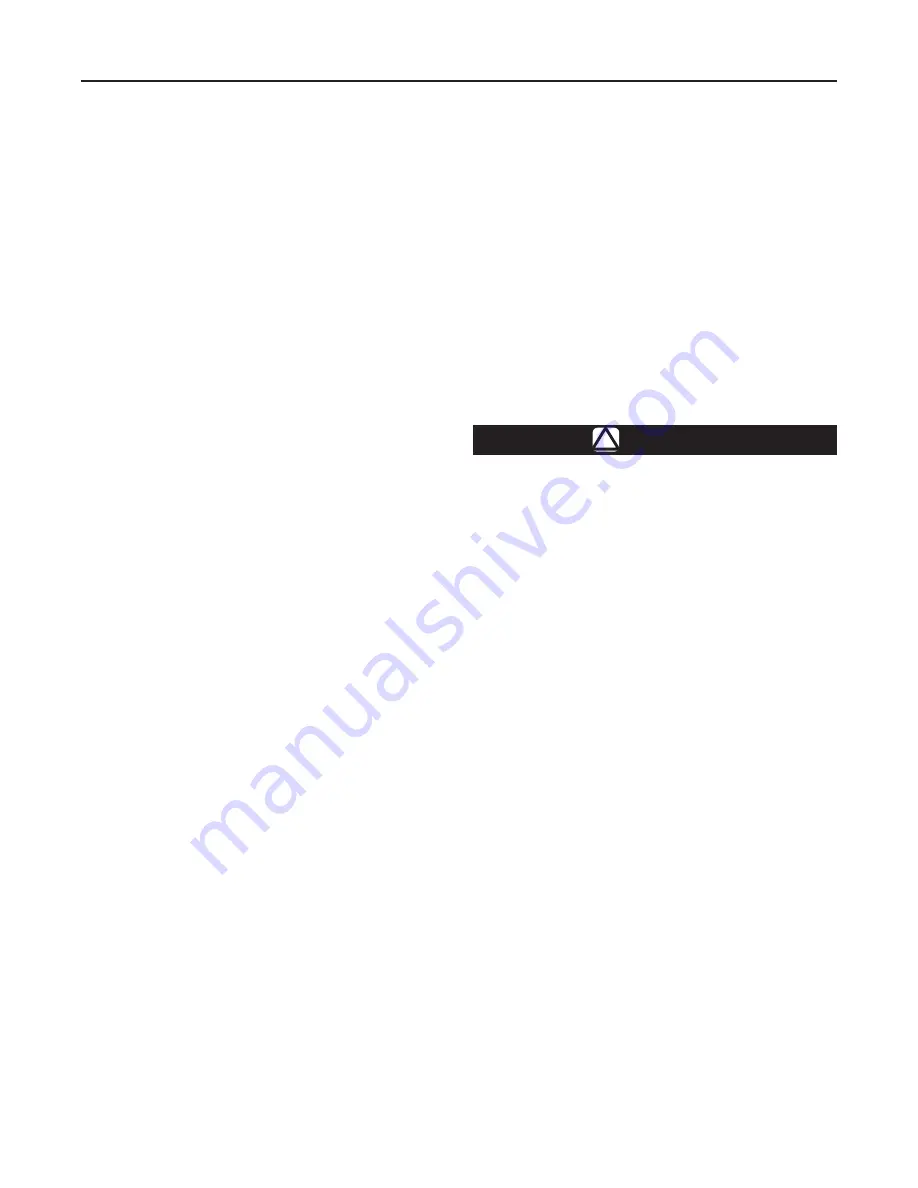
!
1. If using pipe, apply a good grade of pipe
compound to the external pipe threads before
making the connection. Install tubing or piping into
the appropriate pilot connection.
2.
Set pressure is defined as the pressure at which
the pilot starts to discharge. The set pressure
of a unit is adjusted by changing the control
spring compression on the pilot, by using the
adjusting screw.
3. Each pilot is factory set for the relief set pressure
specified on the order. If no setting is specified, set
pressure is factory set at the midrange of the pilot
control spring.
Startup and Adjustment
Key numbers are referenced in Figures 4, 5 and 6
unless otherwise indicated.
1. With proper installation and adjustment completed,
slowly open the upstream shutoff valve while using
gauges to monitor pressure. On backpressure or
bypass applications using an isolating bypass,
also open the downstream shutoff valve and close
the bypass valve.
2. If set pressure adjustment is necessary,
monitor inlet pressure with a gauge during the
adjustment procedure.
Pilot Adjustment
Adjust the set pressure by loosening the pilot jam nut
(key 17) and turning the pilot adjusting screw (key 15)
clockwise to increase or counterclockwise to decrease
the set pressure. When the required set pressure is
maintained for several minutes, tighten the jam nut to
lock the adjusting screw in position.
Shutdown
Relief Installations
Slowly close the upstream shutoff valve. Release all
pressure from the main valve and pilot by opening the
upstream vent valve.
Backpressure or Bypass Installations
Slowly close the upstream shutoff valve while opening
the bypass valve if an isolating bypass is used. Then
close the downstream shutoff valve and open both
vent valves to release all pressure from the main valve
and pilot.
WARNING
Maintenance
Relief valve and backpressure regulator parts are
subject to normal wear and must be inspected and
replaced as necessary. The frequency of inspection
and replacement of parts depends upon the severity
of service conditions or the requirements of local, state
and federal regulations. Due to the care Emerson
takes in meeting all manufacturing requirements
(heat treating, dimensional tolerances, etc.), use
only replacement parts manufactured or furnished by
Emerson. All O-rings, gaskets and seals should be
lightly lubricated with a good grade of general purpose
grease and installed gently rather than forced into
position. Be certain that the nameplates are updated
to accurately indicate any field changes in equipment,
materials, service conditions or pressure settings.
To avoid personal injury and
equipment damage, isolate the valve
from all pressure. Cautiously release
pressure from the valve before
attempting disassembly.
Type 63EG Main Valve
Replacing Trim Parts
Perform this procedure if inspecting, cleaning or
replacing individual parts in the trim package.
Key numbers for the Type 63EG main valve are
referenced in Figures 4 and 5.
Note
Access to the spring (key 9) or flange
O-ring (key 21) in step 1 can be gained
without removing the body flange (key 2).
1. Remove the pilot and pilot pipe nipple from the valve
body. Remove the body flange plug (key 27) and the
spring (key 9) and attached parts. Proceed to step 5 if
only performing maintenance on these parts.
2. Remove the cap screws (key 3) and pry the body
flange (key 2) loose from the valve body (key 1).
3. The valve body (key 1) can be used as a holding
fixture by flipping the body flange over and anchor
it on the valve body as shown in Figure 3.
4. To gain access to the port seal (key 12), upper seal
(key 15) or valve plug parts, unscrew the seat ring
(key 13) from the cage (key 11) and the cage from
the body flange (key 2). For leverage, a wrench
5
Type 63EG-98HM