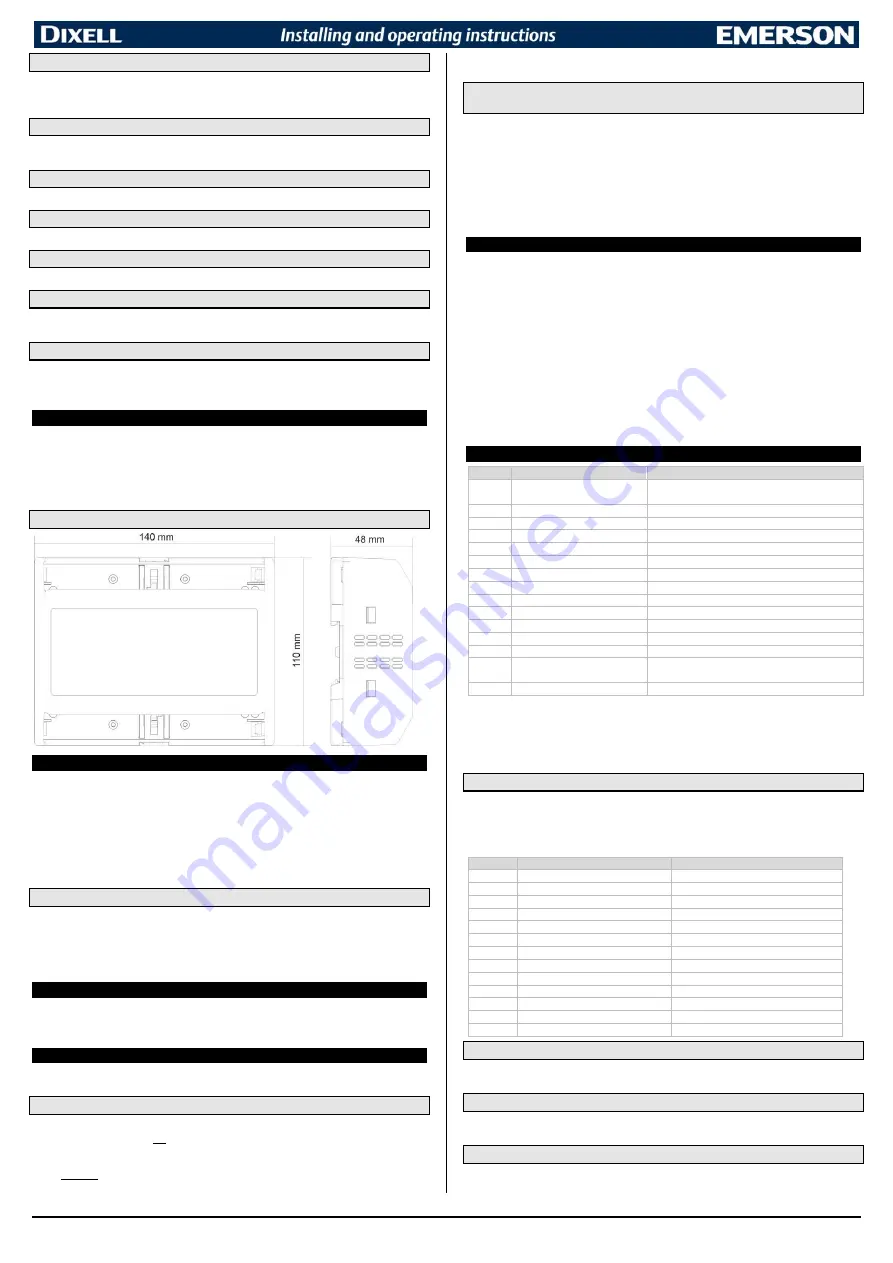
1592026601 XWi70K STD FULL EN r1.6 2022.07.29.docx
XWi70K
8/15
16.6
DEFROST CONTROL (dEF)
It starts a defrost if there are the right conditions. After the defrost is finished, the normal regulation will
restart only if the digital input is disabled otherwise the instrument will wait until the
MdF
safety time is
expired.
16.7
ENERGY SAVING (ES)
The Energy Saving function allows to change the set point value as the result of the
SET+HES
(parameter) sum. This function is enabled until the digital input is activated.
16.8
HOLIDAY MODE (HdF)
Holiday mode activation.
16.9
REMOTE LIGHT CONTROL (LIG)
To manage the light activation from remote.
16.10
REMOTE ON OFF (onF)
To issue a remote ON/OFF command.
16.11
PARAMETER MAP CHANGE (Lnt)
To change the used parameter map from
nt
(first configuration or “normal temperature”) to
Lt
(second
configuration or “low temperature”) and vice
-versa.
16.12
DIGITAL INPUTS POLARITY
The digital input polarity depends on the
i1P
or
i2P
parameters:
i1P or i2P=CL:
the input is activated by closing the contact.
i1P or i2P=OP:
the input is activated by opening the contact
17
HOW TO INSTALL AND MOUNT
The controller
XWi70K
shall be mounted in a din rail and in a horizontal position or with the relay output
on the bottom side (IEC/60730).
It must be connected to the keyboard by using a 2-wire cable (
1mm). The temperature range allowed
for correct operation is 0 to 60°C. Avoid places subject to strong vibrations, corrosive gases, excessive
dirt or humidity. The same recommendations apply to probes. Let the air free to circulate by the aeration
holes.
17.1
XWi70K
–
8 DIN CASE - DIMENSIONS
18
ELECTRICAL CONNECTIONS
XWi70K
is provided with screw terminal blocks to connect cables with a cross section up to 2.5 mm
2
for
the RS485 (optional) and the keyboard. To connect the other inputs, power supply and relays,
XWi70K
is provided with Plug-in connections (6.3mm). Heat-resistant cables must be used. Before connecting
cables make sure the power supply complies with the instrument’s requirements. Separate the probe
cables from the power supply cables, from the outputs and the power connections. Do not exceed the
maximum current allowed, in case of heavier loads use a suitable external relay.
NOTE:
-
The maximum current allowed for the common line of the relays is 14A (IEC/60730)
-
The maximum current allowed for insulated relay (oA5) is 3A (IEC/60730)
18.1
PROBE CONNECTIONS
The probes shall be mounted with the bulb upwards to prevent damages due to liquid infiltration. It is
recommended to place the thermostat probe away from air streams to correctly measure the average
room temperature. Place the defrost termination probe among the evaporator fins in the coldest place,
where most ice is formed, far from heaters or from the warmest place during defrost, to prevent
premature defrost termination.
19
TTL/RS485 SERIAL LINE
The TTL connector allows, by means of the external module TTL/RS485
(XJ485CX)
, to connect the unit
to a network line
ModBUS-RTU
compatible as the
Dixell
monitoring system. The same TTL connector
is used to upload and download the parameter list of the “
HOT-KEY
”.
20
HOW TO
USE OF THE “HOT KEY”
NOTE: the XWi controllers need a 64KB HOT KEY (Dixell code:
DK00000300
). Standard Hot Key is not
supported.
20.1
PROGRAM A HOT-KEY FROM AN INSTRUMENT (UPLOAD)
1.
Program one controller with the front keypad.
2.
When the controller is ON
, insert the “
HOT-KEY
” and push
UP
button; t
he “
uPL
”
message
appears followed a by a flashing “
End
” label.
3.
Push
SET
button and the “
End
” will stop flashing.
4.
Turn OFF
the instrument, remove the “
HOT-KEY
” and
then turn it ON again.
NOTE
: the “
Err
” message appears in case of a failed programming opera
tion. In this case push again
button if you want to restart the upload again or remove the “
HOT-KEY
” to abort the operation.
20.2
HOT TO CHANGE PARAMETER MAP BY USING AN HOT-KEY
(DOWNLOAD)
1.
Turn OFF the instrument.
2.
Insert a
pre-programmed
“
HOT-KEY
”
into the 5-PIN port
and then turn the Controller ON.
3.
The parameter list of the “
HOT-KEY
” will be automatically downloaded into the Controller
memory. The “
doL
” message will blink followed a by a flashing “
End
” label.
4.
After 10 seconds the instrument will restart working with the new parameters.
5.
Remove the “
HOT-KEY
”.
NOTE:
the message “
Err
” is displayed for failed programming. In this case turn the unit off and then on
if you want to restart the download again or remov
e the “
HOT-KEY
” to abort the operation.
21
INTERNAL MEMORY
The controller has an internal memory where are stored:
-
Parameter maps
nt
and
Lt
-
Factory default configurations for both
nt
and
Lt
parameters map
The controller is always shipped with:
-
Parameter map
nt
= factory default configuration “
nt
”
-
Parameter map
Lt
= factory default configuration “
Lt
”
Any modification to parameter map
nt
or
Lt
does not change factory values.
It will be possible to restore factory defaults values for
nt
or
Lt
parameters map by using
UP2=CC
function.
NOTES:
-
If controller is using
nt
parameter map, the factory default configuration
nt
will be reloaded
overwriting
nt
parameter map. The same for parameter map
Lt
.
-
The factory default configurations are read only (it is not possible to modify them on the field).
22
ALARM SIGNALS
Message Cause
Outputs
P1
Thermostat probe failure
Alarm output ON; Compressor output according to
parameters
Con
and
CoF
P2
Second probe failure
Alarm output ON; Other outputs unchanged
P3
Third probe failure
Alarm output ON; Other outputs unchanged
P4
Fourth probe failure
Alarm output ON; Other outputs unchanged
HA
Maximum temperature alarm
Alarm output ON; Other outputs unchanged
LA
Minimum temperature alarm
Alarm output ON; Other outputs unchanged
HA2
Condenser high temperature
It depends on the
AC2
parameter
LA2
Condenser low temperature
It depends on the
bLL
parameter
dA
Door open
Compressor and fans restarts
EA
Warning
Output unchanged
CA
Lock alarm (i1F=bAL)
All outputs OFF
CA
Pressure switch alarm (i1F=PAL) All outputs OFF
EE
Data or memory failure
Alarm output ON; Other outputs unchanged
noL
No communication between base
and keyboard
Unchanged
EC1
VSC communication error
Unchanged
The alarm message is displayed until the alarm condition is recovery.
All the alarm messages are showed alternating with the room temperature except for the “P1” which is
flashing.
To reset the “EE” alarm and restart the normal functioning press any key, the “
rSt
” message is displayed
for about 3 sec.
22.1
SERIAL COMPRESSOR AND MODBUS FAN MANAGEMENT
The following table shows the managed alarms and errors when the serial compressor or the serial fan
control is used.
-
EMB1 or 2:
indication valid for Embraco compressor 1 or 2
-
SCP1 or 2:
indication valid for SECOP compressor 1 or 2
Message
Cause
Outputs
EC1
EMB1 or 2: communication error
Regulation stopped, retry function active
CP1, CP2
EMB1 or 2: compressor stopped
Regulation stopped, retry function active
HP1, HP2
EMB1 or 2: start fail
Regulation stopped, retry function active
E11, E21
EMB1 or 2: overload
Regulation stopped, retry function active
E12, E22
EMB1 or 2: under speed
Regulation stopped, retry function active
E13, E23
EMB1 or 2: wrong rotor position
Regulation stopped, power off required
E14, E24
EMB1 or 2: short circuit
Regulation stopped, power off required
HT1, HT2
EMB1 or 2: high temperature
Regulation stopped, retry function active
EC2
SCP1 or 2: communication error
Regulation stopped, retry function active
EV1, EV2
SCP1 or 2: voltage error
Regulation stopped, retry function active
EM1, EM2
SCP1 or 2: motor error
Regulation stopped, retry function active
ET1, ET2
SCP1 or 2: internal temperature error Regulation stopped, retry function active
CSr
Condenser fan maintenance
Unchanged, warning reset required
22.2
BUZZER MUTING
Once the alarm signal is detected the buzzer can be silenced by pressing any key. Buzzer is mounted
in the keyboard and it is an option.
22.3
“EE” ALARM
The
Dixell
instruments are provided with an internal check for the data integrity. The “EE” alarm flashes
when a failure in the memory data occurs. In such cases the alarm output is enabled.
22.4
ALARM RECOVERY
Probe
alarms: “
P1
” (probe1 faulty), “
P2
”, “
P3
” and “
P4
”; they automatically stop 10 sec after the probe
restarts normal operation. Check connections before replacing the probe.