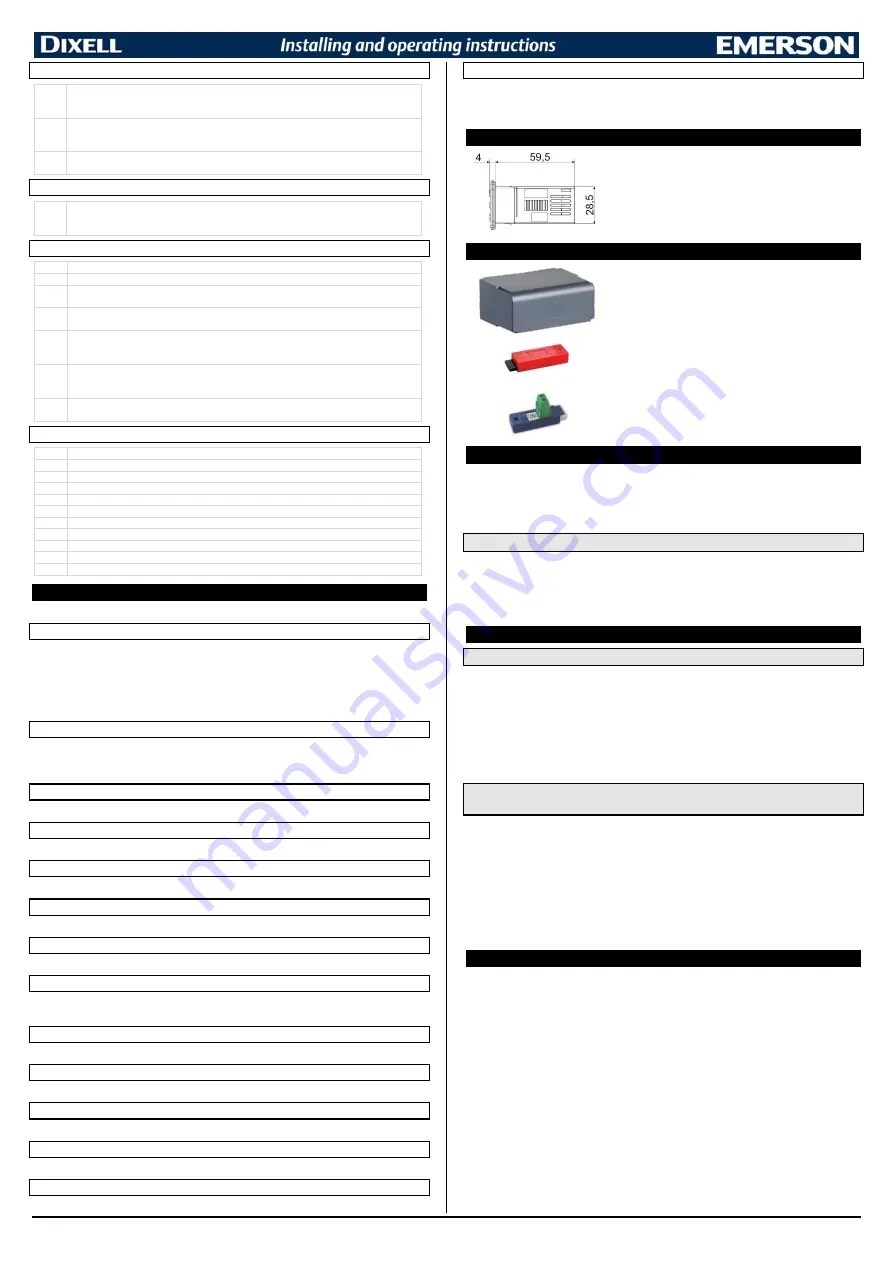
1592033070 XR70CHC EN r1.0 2019.01.30
XR70CHC
5/6
BLUETOOTH - bLE
btM
Bluetooth Mode:
(0; 1; 2) define the pairing&bonding method:
-
0
=6-digit PIN is required for pairing&bonding
-
1,2
=no PIN required (just works mode)
rPS
Reset owner password:
(n;Y) select and confirm YES to come back to default factory
configuration. NOTE: remember to cancel the device also from the Cloud database (click on
“Delete” link present on the right of the appliance card present on the “Permissions” webpage.
rLi
Reset whitelist:
(n;Y) select and confirm YES for reset the device whitelist and come back to
default factory configuration.
EEPROM
–
E2
rSC
Reset Daily Counters:
used to reset the daily counters memory. Please note that after
selecting rSC=Y the device will take some time to complete the operation. During the reset
phase, the display will show some blinking lines.
OTHER - oth
Adr
Serial address:
(1 to 247) device address for Modbus communication
bAU
Baudrate:
(9.6; 19.2; 38.4; 57.6) select the correct baudrate for serial communication
brd
Keyboard lock type:
(nu; SEL; ALL)
UnL
=keyboard unlocked;
SEL
=only SET and DEF/AUX
button enabled when locked;
ALL
=keyboard unlocked after
tLC
.
tLC
Keyboard lock timeout:
(0 to 255 sec) timeout after power-on and before activating the
keyboard lock
LGC
Light button configuration (left upper side): nu
=not used;
LiG
=light output control;
AUS
=auxiliary output control;
dEF
=defrost control;
Pb2
=probe 2 value visualization;
ES
=change working mode from normal to energy saving mode and vice-versa;
LG2
Light button timed (3sec) configuration (left upper side): nu
=not used;
LiG
=light output
control;
AUS
=auxiliary output control;
dEF
=defrost control;
CC
=change configuration between
NT and LT map;
ES
=change working mode from normal to energy saving mode and vice-versa;
UP2
Up button timed (3sec) configuration:
nu
=not used;
Std
=standard function;
LdC
=load
default configuration (factory values);
Pdn
=pull down activation
VISUALIZATION - ViS
d1
Probe P1 value visualization
d2
Probe P2 value visualization
d3
Probe P3 value visualization
d4
Probe P4 value visualization
rSE
Real Set point
FdY
Firmware release date: day
FMt
Firmware release date: month
FYr
Firmware release date: year
rEL
Firmware release: progressive number
Sub
Firmware sub release: progressive number
Ptb
Parameter code table
13
DIGITAL INPUTS
The free voltage digital input is programmable in different configurations by the
i1F
and
i2F
.
DOOR SWITCH (ixF=dor)
It signals the door status and the corresponding relay output status through the
odC
parameter:
no
= normal (any change);
FAn
= Fan OFF;
CPr
= Compressor OFF;
F-C
= Compressor and fan OFF.
Since the door is opened, after the delay time set through parameter
did
, the door alarm is enabled,
the display shows the message
“
dA
”
and
the regulation restarts if rrd = Y.
The alarm stops as soon
as the external digital input is disabled again. With the door open, the high and low temperature alarms
are disabled.
START DEFROST (ixF=dEF)
It starts a defrost if there are the right conditions. After finishing any defrost, the normal regulation will
restart only if the digital input is disabled, otherwise the instrument will wait until the
MdF
safety time is
expired.
ENERGY SAVING (ixF=ES)
The energy saving mode will be enabled / disabled with the digital input.
MOTION SENSOR (ixF=EMt)
It counts the motion sensor detections.
AUXILIARY OUTPUT (ixF=AUS)
The AUX output (if present and configured) will be enabled / disabled with the digital input.
EXTERNAL WARNING ALARM (ixF=EAL)
It is used to detect an external alarm. It does not lock the regulation.
EXTERNAL LOCK ALARM (ixF=bAL)
It is used to detect any critical external alarm. It locks immediately the regulation.
EXTERNAL PRESSURE ALARM (ixF=PAL)
It is used to detect any pressure external alarm. This signal locks the regulation after
nPS
events in
dxd
interval od time.
EVAPORATOR FAN MODE (ixF=FAn)
It is used to control the evaporator fan.
REMOTE HOLYDAY MODE (ixF=HdF)
It is used to force the holyday mode.
REMOTE ONOFF (ixF=onF)
It is used to switch ON and OFF the device remotely.
LIGHT OUTPUT (ixF=LiG)
It is used to control the light output.
CHANGE CONFIGURATION (ixF=CC)
It is used to change the controller configuration.
MOTION SENSOR DETECTOR (ixF=EMt)
To use the X-MOD motion sensor. Please note that motion sensor can be connected only to the
HOTKEY port, so it needs digital input 2 properly configurated.
14
INSTALLATION AND MOUNTING
Instrument
XR70CHC
shall be mounted on vertical panel, in a
29x71 mm hole, and fixed using the special bracket supplied.
The temperature range allowed for correct operation is 0 to 60°C.
Avoid places subject to strong vibrations, corrosive gases,
excessive dirt or humidity. The same recommendations apply to
probes. Let air circulate by the cooling holes.
15
OPTIONAL FEATURES
The
MDP/CX
rear cover can be used to increase the protection
from water and dust.
The
HOT-KEY
is used for a quick and easy upload (from device
to
HOT-KEY
) or download (from
HOT-KEY
to device) the
parameter map.
The
XJ485LE
serial interface converts the TTL output into an
RS485 signal that can be used to connect the unit to the
controlling and supervising system. Please note that other
version of this converter does not work with XR-CHC devices.
16
ELECTRICAL CONNECTIONS
The instrument is provided with screw terminal block to connect cables with a cross section up to
2.5mm
2
. Before connecting cables make sure the power supply complies with the instrument’s
requirements. Separate the probe cables from the power supply cables, from the outputs and the
power connections. Do not exceed the maximum current allowed on each relay, in case of heavier
loads use a suitable external relay.
16.1
PROBES
The probes shall be mounted with the bulb upwards to prevent damages due to casual liquid
infiltration. It is recommended to place the thermostat probe away from air streams to correctly
measure the average room temperature. Place the defrost termination probe among the evaporator
fins in the coldest place, where most ice is formed, far from heaters or from the warmest place during
defrost, to prevent premature defrost termination.
17
USE THE HOT-KEY
17.1
SAVE PARAMETERS IN A HOT-KEY (UPLOAD FROM INSTRUMENT)
1.
Program one controller with the front keypad.
2.
When the controller is ON, insert the “
HOT-KEY
” an
d push
UP
button; the
“
UP
”
message
appears followed a by flashing “
End
”
3.
Push “
SET
” key and the “
End
”
will stop flashing.
4.
Turn OFF the instrument
and then remove the “
HOT-KEY
”.
At the end turn the instrument ON
again.
NOTE:
the “
Err
” message appears in case of a failed programming operation. In this case push again
the
UP
button if you want to restart the upload again or remove the “
HOT-KEY
” to abort the operation
.
17.2
COPY PARAMETERS FROM A HOT-KEY (DOWNLOAD PARAMETER
VALUES)
1.
Turn OFF the instrument.
2.
Insert a
programmed “
HOT-KEY
” into the 5
-PIN port
and then turn the Controller ON.
3.
T
he parameter list of the “
HOT-KEY
” is
automatically copied into the controller memory. During
this operation
the “
do
” message
will blink
4.
A flashing
“
End
” l
abel will inform that the operation was successful
5.
Remove the “
HOT-KEY
”.
6.
After some seconds the instrument will restart, using with the new parameters.
NOTE:
the message “
Err
” is displayed for failed programming. In this case turn the unit off and then
on
if you want to restart the download again or remove the “
HOT-KEY
” to abort the operation
.
18
INTERNAL MEMORY
The controller has an internal memory where are stored:
-
Two different parameter maps identified as
C1
and
C2
-
Factory default configurations for both
C1
and
C2
parameters map
The controller is always shipped with:
-
Parameter map
C1
= factory default configuration
C1
-
Parameter map
C2
= factory default configuration
C2
Any modification to parameter map
C1
or
C2
does not change the default factory values.
It is possible to change parameter map between
C1
and
C2
by using a digital input or a button properly
configurated (
ixF
or
LG2=CC
).
It is possible to restore factory defaults values for both
C1
or
C2
parameters map by using
UP2=LdC
(Load
default configuration) function.
NOTES:
-
If controller is using
C1
parameter map, the factory default configuration
C1
will be reloaded
overwriting
C1
parameter map. The same for parameter map
C2
.
-
The factory default configurations are read only (it is not possible to modify them on the field).