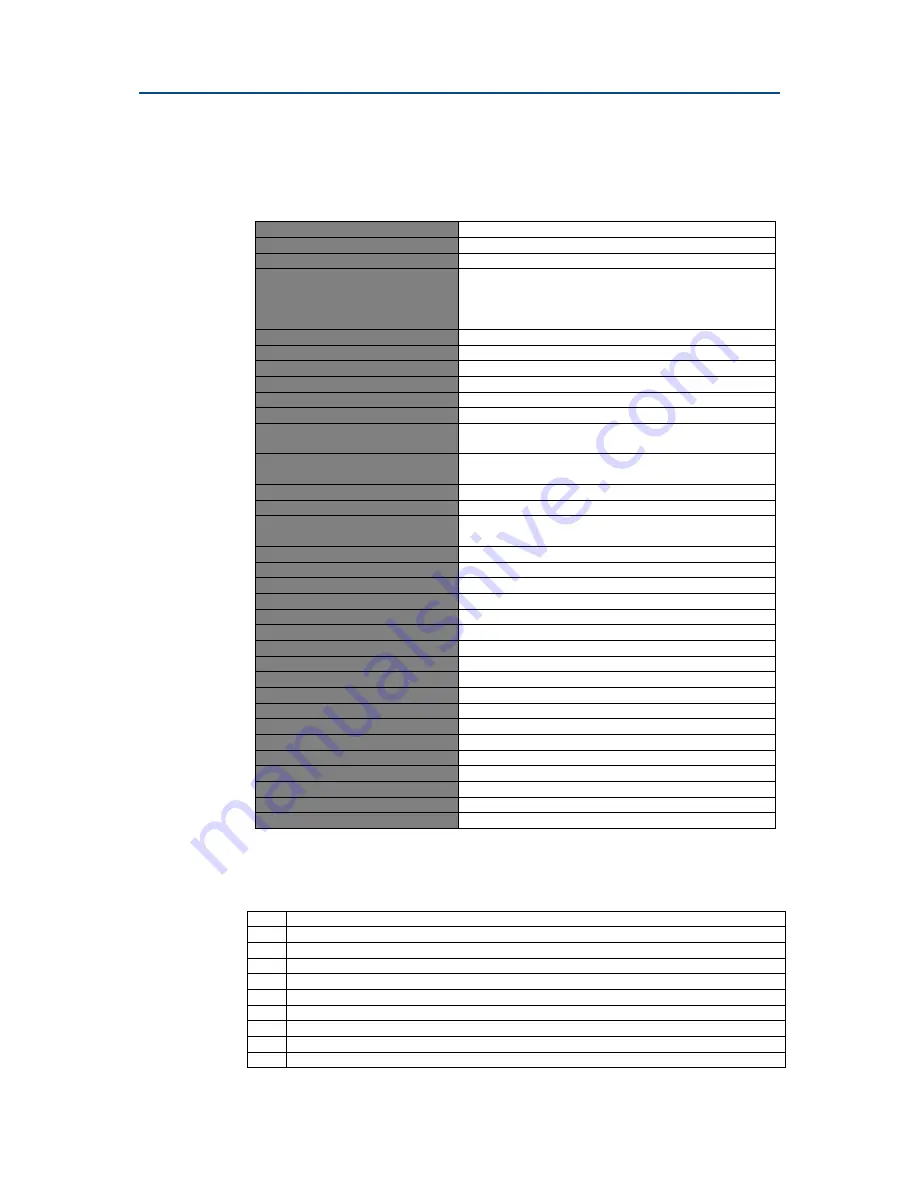
User Manual
Introduction
QCL-MAN -CT2211-Aerosol-Leak-Detection-System-Rev F
October 2015
Introduction
7
1.6
Detailed system specification
The following table shows the general characteristics of the leak detection system.
Table 1-1 Leak detection system specifications
Application
Leak detection system
Measurement technique
IR absorption spectroscopy
IR source
Quantum cascade laser
Laser classification
Class1
BS EN 60825-1:2007 Safety of laser products
Equipment classification and requirements (identical to
IEC 60825-1 2007)
Sensitivity
2 X 10
-3
mbar.L
-1
Line speed
Up to 500 cpm
Can dimensions
Up to 350 mm (H) by 80 mm (D)
Response time
20 ms
Temperature range
10 — 30 °C (50 — 86 °F)
Sample gas temperature range
Room temperature
Leak detector humidity range
10 to 95 % relative humidity (non-condensing) at 35 °C
(95 °F)
ATEX Approvals (in zone sensor)
Zone 2 Ex II 2G Ex nR II T6 (10 °C
≤
T
amb
≤
30 °C)
(50 °F
≤
T
amb
≤
86 °F)
Leak detection system
CE approved
Protection class
IP65
Hazardous area classification
Ex II 3G Ex nR II T6 (10 ° C
≤
T
amb
≤
30° C)
(50 °F
≤
T
amb
≤
86 °F)
Analog signal out
n/a
Analog signal in
n/a
Digital signal out
3 X normally closed contact
Digital signal in
10/100 Base T ethernet
Inlet gas port connector
¾ in. BSPT
Exhaust gas port connector
¾ in. BSPT
Power supply
120 VAC 60 Hz/240 VAC 50 Hz 200 W/A
Control console size
1,200 x 600 x 560 mm (H x W x D)
Control console weight
70 kg
Sensor head size
590 x 330 x 330 mm (H x W x D) sensor only
Sensor head weight
20 kg (sensor only)
Installation
On production line
System operating voltage
110 — 240 V AC 50 -60 Hz, specify on order
System power consumption
600 W maximum power requirement
Max factory air consumption
25 L/min approximately on regular usage
Factory compressed air pressure
8-10 bar, clean, dry, and oil free
Line space requirement
1.2 m straight free line (maximum)
Air filter particulate filter
2 um, inline filter/regulator required
1.7
Operators’ system pre startup checklist
Remove hose from air line.
Check and bleed air line.
Check filter condition and color before switching on system.
Change filter if more than 60% discolored.
Ensure that there are no cans between the input and output gates.
Power on system.
Power on conveyor; do not let cans though.
Clear any error messages, e.g., encoder.
Purge air in chamber
Let cans through to commence normal working activity.