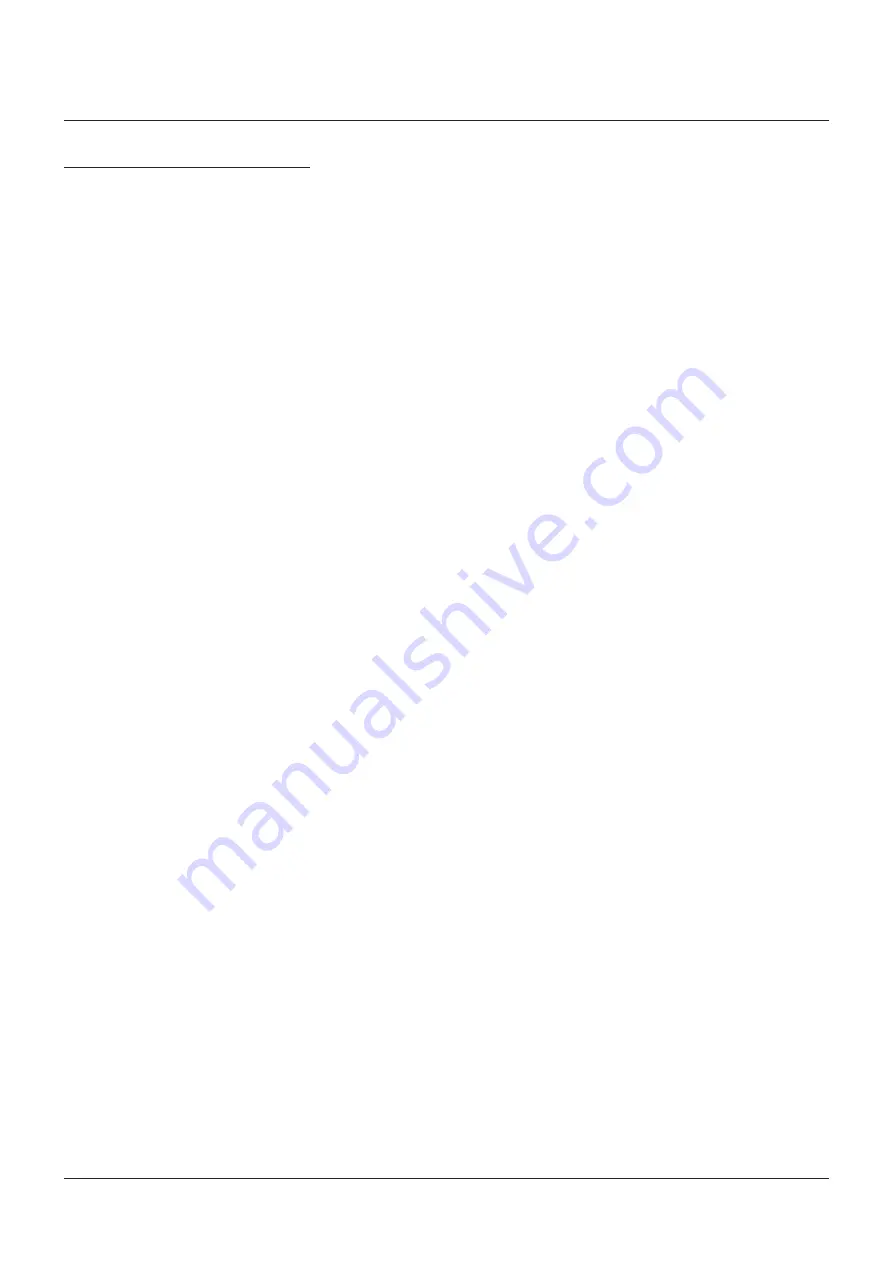
10
Install the gags as follows (refer to Figure 5):
• Remove the lever (27), forked lever (30),
cap (25) and spindle nut (23).
• Lubricate the threads and pointed end
of the gag screw.
• Install the gag in place, being careful that the
legs fit uniformly. Contacts on both legs of the
gag should seat evenly on the underside of
the bonnet (13) top.
• Tighten the gag finger-tight.
Raise the system pressure until the safety
valve pops.
Record the popping and reseating
pressures (pressure at which the safety
valve closes sharply).
CROSBY
®
STYLES HC AND HCA ISOFLEX™ SAFETY VALVES
INSTALLATION, MAINTENANCE AND ADJUSTMENT INSTRUCTIONS
CAUTION
All safety valves on the system except the
valve that is to be popped should be gagged.
System pressure should be 70% of valve set
pressure before gagging to prevent added loads
from being applied to the valve spindle due to
thermal expansion.
Gagging must be done with care not to overload
the spindle since considerable damage may occur
to the spindle and other valve internals. However,
a minimum torque should be applied to the gag
by hand to ensure that the valve will not open.
8 TESTING
Set pressure testing and valve adjustments
The set pressure of a safety valve may be
checked without removing the valve from
the system by two methods described in the
following paragraphs:
• Set pressure lift assist device
The first method of set pressure testing is
with the use of a set pressure lift device.
This allows set pressure testing of the safety
valves on the system at pressures below
normal system operating pressures.
Two devices are available for use on
Crosby Style HC/HCA safety valves: the air
set pressure device and the hydraulic set
pressure device. Refer to test procedure
T-1652 for detailed instructions in the use of
the air set pressure device and instruction
I-11288 for detailed instructions in the use of
the hydraulic set pressure device.
• System pressure
The second method of set pressure testing is
by raising the system pressure and popping
the safety valve. Set pressure testing using
this method will determine the safety valve
set and closing pressure (blowdown).
Setting the safety valve with the set pressure
lift device is recommended before raising
the system pressure for popping pressure
testing. This allows the set point to be
established without raising and lowering
system pressure several times to determine
the safety valve set pressure.
Before set pressure testing and raising the
system pressure, the following items should
be checked:
- A pressure gauge with known accuracy
should be located on the system
being tested.
- Outlet piping should be anchored sufficiently
to prevent any vibrations while the safety
valve is discharging. The outlet piping
should be direct and there should be no
obstructions to restrict the safety valve
discharging.
WARNING
Never strike a valve which is under pressure.
Premature actuation can result.
WARNING
Hearing and eye protection should be used when
working on a valve which is under pressure. Never
stand in front of the discharge of a safety valve
which is under pressure.
- Set screws should be tight and lock
wired. The tapped holes in the body for
drains should be connected to the drain
or plugged.
- Lifting gear should be fastened securely to
the safety valve to assist personnel testing
the valve. A rope may be attached through
the hole provided in the lever should
mechanical lifting be necessary.
• Communications should be set up between
the control room and personnel in the
test area.