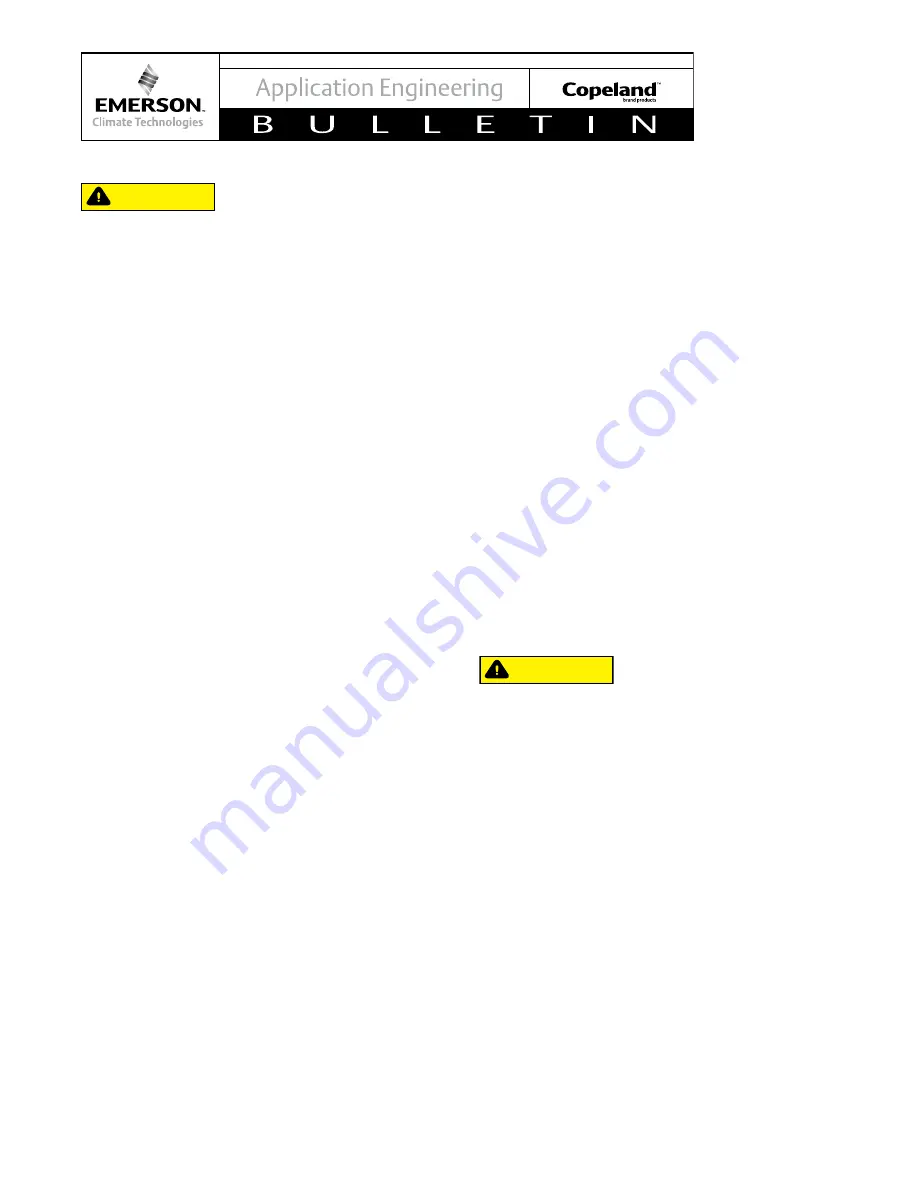
5
© 2015 Emerson Climate Technologies, Inc.
AE4-1365 R4
Discharge Temperature Protection
CAUTION
Compressor top cap temperatures can be very
hot. Care must be taken to ensure that wiring or
other materials which could be damaged by these
temperatures do not come into contact with these
potentially hot areas.
Protection against abnormally high discharge
temperature is accomplished through one of the two
folowing methods:
The Therm-O-Disc
™
or TOD is a temperature-sensitive
snap disc device located between the high and low
pressure side of the scroll. It is designed to open
and route excessively hot discharge gas back to the
internal motor overload when the internal discharge
gas exceeds 290°F (144°C). When the internal motor
overload is subjected to hot discharge gas the overload
will reach its opening temperature and take the
compressor off-line. ZP91 and smaller compressors in
this family use this method of temperature protection.
The second type of discharge temperature protection is
referred to as Advanced Scroll Temperature Protection
(ASTP). During a high discharge temperature event,
a temperature-sensitive snap disk located in the
intermediate cavity of the scroll will open and vent
the intermediate cavity. This will result in the scrolls
separating and not pumping. The motor will continue
to run until the internal overload opens from a lack of
refrigerant flow/cooling. The temperature-sensitive disk
has a shorter reset time than the internal motor overload,
so when the internal overload resets and brings the
compressor back on line the compressor will run and
pump. Compressors that have ASTP are identified with
the ASTP label shown in
Figure 3
.
Heat Pump Protection
A low pressure control is highly recommended for
loss of charge protection and other system fault
conditions that may result in very low evaporating
temperatures. Even though these compressors have
internal discharge temperature protection, loss of
system charge will result in overheating and recycling
of the motor overload protector. Prolonged operation in
this manner could result in oil pump out and eventual
bearing failure. A cut out setting no lower than 20 psig
(1.4 bar) is recommended.
Discharge Line Thermostat
Some systems, such as air-to-air heat pumps, may not
work with the above low pressure control arrangement.
A discharge line thermostat set to shut the compressor
off before the discharge temperature exceeds 260°F
(125°C) may have to be used to achieve the same
protection. Mount the discharge thermostat as close
as possible to the compressor discharge fitting and
insulate well. See
Table 4
for recommended Emerson
Climate Technologies part numbers.
Air Conditioning Unit Protection
Air-conditioning-only units can be protected against
high discharge temperatures through a low pressure
control in the suction line. Testing has shown that a
cut out setting of not lower than 55 psig (3.8 bar) will
adequately protect the compressor against overheating
from loss of charge, blower failure in a TXV system,
etc. A higher level of protection is achieved if the low
pressure control is set to cut out around 95 psig (6.7
bar) to prevent evaporator coil icing. The cut in setting
can be as high as 180 psig (12.5 bar) to prevent rapid
recycling in case of refrigerant loss. If an electronic
controller is used, the system can be locked out after
repeated low pressure trips.
High Pressure Control
CAUTION
The ZP91KC through ZP143KC compressors do
not have an internal pressure relief valve. A high
pressure control with a maximum cut out setting
of 650 psig (45 bar) is required for all ZP91KC
through ZP143KC applications.
All other compressors in this family have an internal
pressure relief valve and the necessity of a high pressure
control switch is dependent on the working pressure
of the system components. The high pressure control
should have a manual reset feature for the highest level
of system protection.
It is not recommended to use
the compressor to test the high pressure switch
function during the assembly line test.
Discharge Check Valve
The ZP91K and smaller displacements in this
compressor family utilize a low mass, disk type check
valve in the discharge fitting of the compressor to
prevent the high side, high pressure discharge gas
from flowing rapidly back through the compressor after
shutdown. The ZP104 through ZP143KC compressors