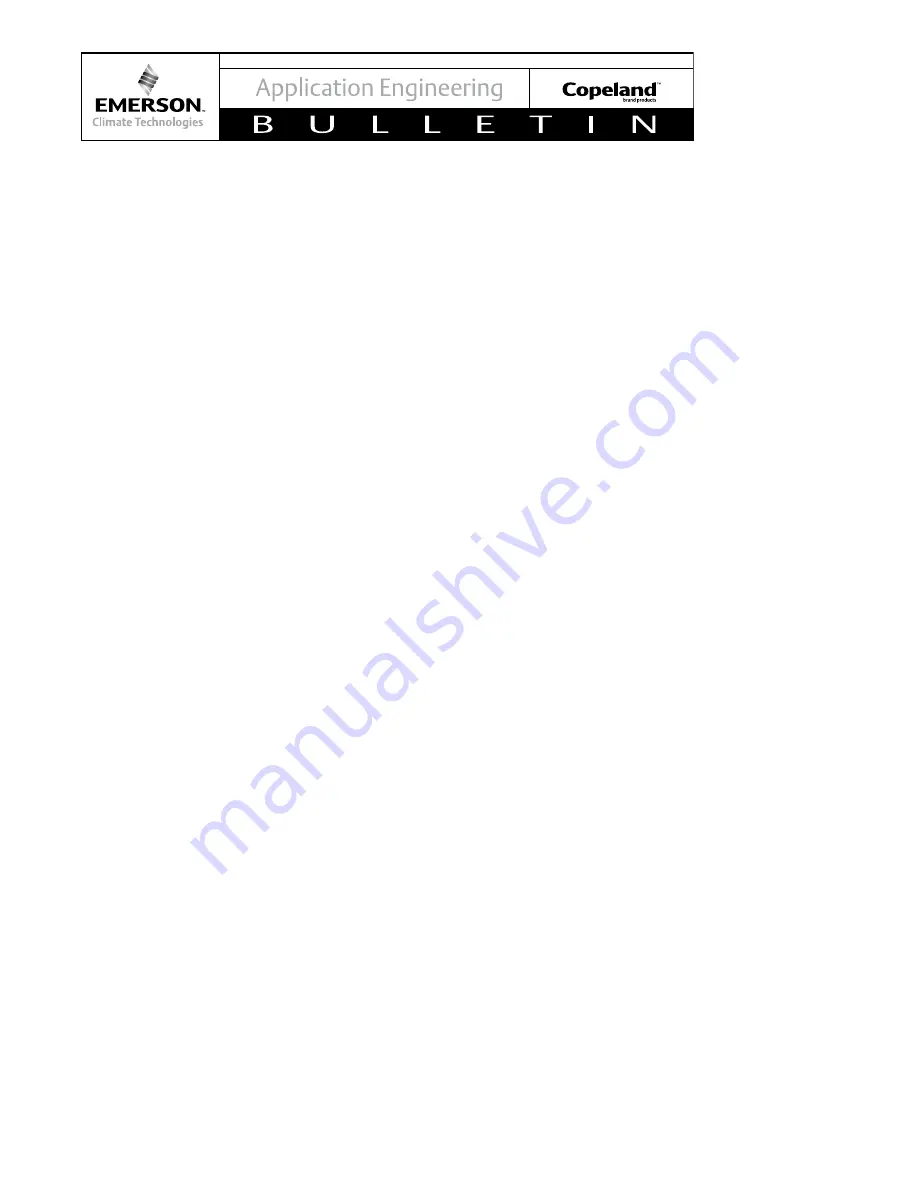
11
© 2015 Emerson Climate Technologies, Inc.
AE4-1365 R4
with compressors of unequal capacity, check with
application engineering or on-line product information
for availability. Tandem ready compressors are
designated with a -4XX bill of material number at the
end of the model number (e.g. ZP61KCE-TFD-420).
See
Figure 5
for a picture of an assembled tandem
showing the hardware and parts required for assembly.
Drawings of tandem tubing assemblies are available
from Emerson Climate Technologies by contacting
your Application Engineer.
Tandem Applications
Tandem compressors follow the same application
guidelines as single compressors outlined in this
bulletin. The refrigerant charge limit for tandem
compressors is shown in
Table 3
. Crankcase heaters
must
be installed on each compressor in the tandem
set when the system charge amount exceeds the
tandem charge limit.
The compressors in a tandem set can be started/
stopped in any desired sequence. To help reduce
the probability of light dimming and to reduce inrush
current, starting the compressors individually is
recommended. Should a compressor fail in the tandem
set the complete tandem should be removed from the
unit and replaced with a new tandem set. Replacing
individual compressors is discouraged because of
the care that must be used when installing the oil
equalization tube and the availability of manifolds to
the aftermarket.
APPLICATION TESTS
Application Test Summary
There are a number of tests the system designer
will want to run to ensure the system operates as
designed. These tests should be performed during
system development and are dependent on the
system type and amount of refrigerant charge. These
application tests are to help identify gross errors in
system design that may produce conditions that could
lead to compressor failure. The Continuous Floodback
Test and Field Application Test, both outlined below, are
two tests to run to help verify the design. When to run
these tests can be summarized as follows:
Continuous Floodback:
Required on all heatpumps.
Field Application Test:
Required for any unit where both the design system
charge is higher than the compressor refrigerant
charge limit listed in
Table 3
; and a capillary tube,
fixed orifice, or bleed-type TXV is used on either
the indoor or the outdoor coil of the unit.
Continuous Floodback Test
It is expected that the design would not flood during
standard air conditioning operation. Running a partially
blocked indoor air filter or loss of evaporator air flow test
and comparing the sump temperature results to
Figure
2
is recommended. The use of a TXV in heating does
not guarantee operation without flood back in the lower
end of the unit/TXV operating range.
To test for excessive continuous liquid refrigerant flood
back, it is necessary to operate the system in a test
room at conditions where steady state flood back may
occur (low ambient heating operation). Thermocouples
should be attached with glue or solder to the center of
the bottom shell and to the suction and discharge lines
approximately 6 inches (15 cm) from the shell. These
thermocouples should be insulated from the ambient air
with Permagum® or other thermal insulation to be able
to record true shell and line temperatures. If the system
is designed to be field charged, it should be overcharged
by 15% in this test to simulate overcharging often found
in field installations.
The system should be operated at an indoor temperature
of 70°F (21°C) and outdoor temperature extremes of
10°F (-12°C) or lower in heating to produce flood back
conditions. The compressor suction and discharge
pressures and temperatures as well as the sump
temperature should be recorded. The system should
be allowed to frost up for several hours (disabling the
defrost control and spraying water on the outdoor coil
may be necessary) to cause the saturated suction
temperature to fall below 0°F (-18°C). The compressor
sump temperature must remain above the sump
temperature shown in
Figure 2
or design changes
must be made to reduce the amount of flood back. If an
accumulator is used, this test can be used to test the
effectiveness of the accumulator. Increasing indoor coil
volume, increasing outdoor air flow, reducing refrigerant
charge, decreasing capillary or orifice diameter, and
adding a charge compensator can also be used to reduce
excessive continuous liquid refrigerant flood back.