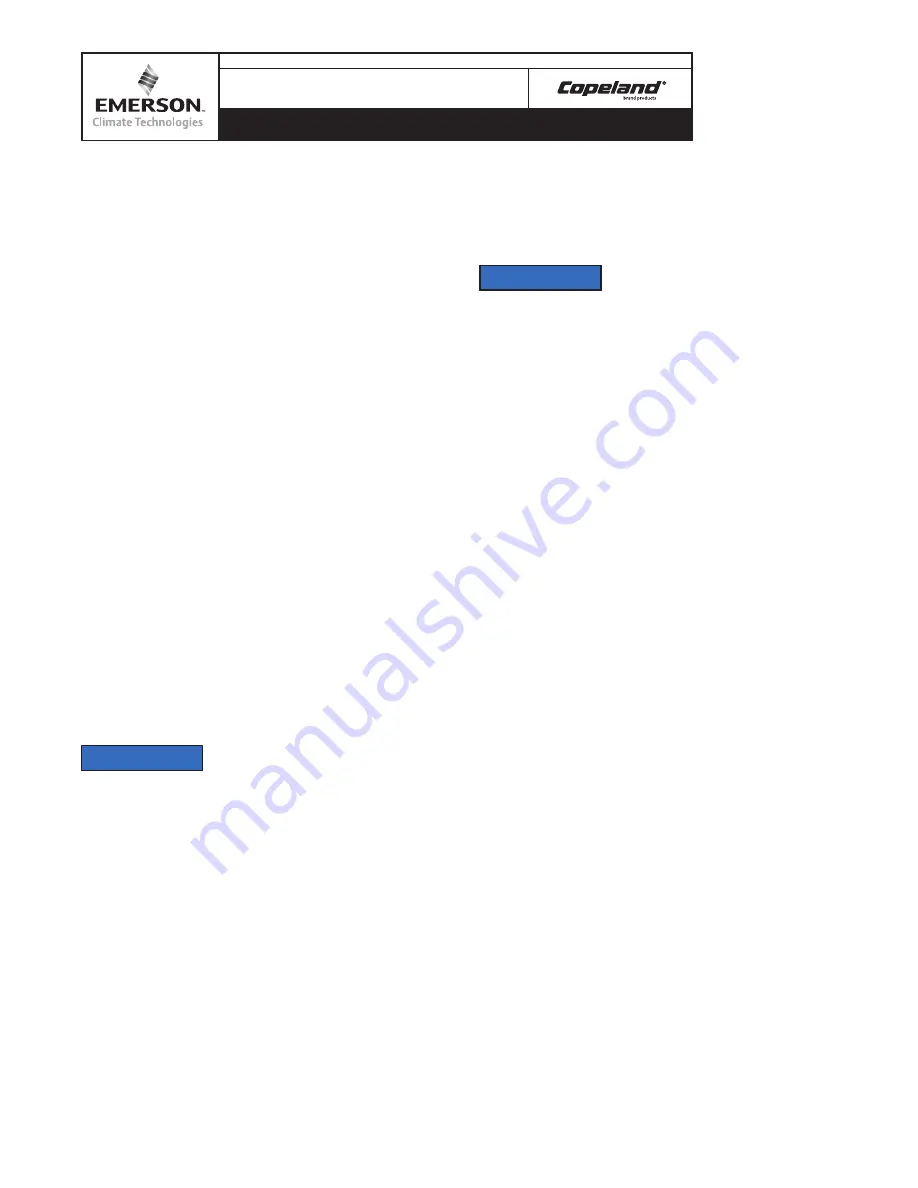
5
© 2014 Emerson Climate Technologies, Inc.
Printed in the U.S.A.
AE4-1317 R10
Application Engineering
B
U
L
L
E
T
I
N
If the system is designed where operation with in these
guidelines cannot be guaranteed, then the discharge line
thermostat is required in the compressor control circuit.
The thermostats have a cut out setting that will insure
discharge line temperatures below the 260°F maximum
limit. It should be installed approximately 7 inches from
the discharge tube outlet. If a service valve is installed
at the discharge tube, the thermostat should be located
5 inches from the valve braze.
Kits have been set up to include the thermostat, retainer,
and installation instructions. These thermostats must
be used with ½” O.D. discharge lines to ensure proper
thermal transfer and temperature control. They work with
either 120 or 240-volt control circuits and are available
with or without an alarm circuit capability. See
Table 4
for a list of discharge line thermostat kit numbers.
Pressure Controls
Both high and low-pressure controls are required on the
following models, (1.3-2 HP) ZB10-14KCE. Only low-
pressure controls are required on the following models,
(2-7.5 HP) ZB15-57KC/E. See
Table 5
for set points.
Application Note: There are exceptions to the pressure
settings listed in
Table 5
. Certain OEMs are approved
for LPC settings below our standard recommendations.
Pump Down Recommendations
Table 6
identi
fi
es the “ZB” models that incorporate
the low-leak check valve suitable for pump-down
applications. The standard disc is not intended for use
with a pump down.
NOTICE
Typically, the compressors that use the low-leak
discharge check valve are suitable for pump down
applications. This valve prevents system pressures
from equalizing and pump down can be achieved.
However, during laboratory testing, we have observed
a potential short cycling condition on the ZB15 through
ZB29 models. This phenomenon can be attributed to
several factors:
1. Location of low-pressure control sensor. If it is
located right at the suction inlet of the compressor,
it will be more sensitive to pressure spikes.
2. Actual low-pressure setting. Refer to our
recommended setting in
Table 5.
If the differential
pressure setting is too close, this will increase the
possibility of short cycling.
3. Type of Low-pressure control can have an effect
on cycling. The encapsulated non-adjustable type
is more susceptible to causing excessive cycling
due to tolerances.
4. If short cycling cannot be avoided, using a 3-minute
time delay will limit the cycling of the compressor
to an acceptable level.
NOTICE
The ZB10 through ZB14 models will require the following
recommendations for pump down applications:
1. Install an external check-valve in the discharge
line to prevent back-
fl
ow from the high side to low
side. Install check-valve as close to the compressor
discharge
fi
tting as possible to minimize discharge
gas volume.
2. Set low pressure to recommended settings in
Table 5
.
3. Since these models are single-phase only, add
a time delay relay to prevent reverse rotation.
Refer to “Brief Power Interruptions” section of this
bulletin for additional information.
IPR Valve
Refrigeration scroll compressors (2-7.5 HP) ZB15-
57KC/E have internal pressure relief valves, which
open at a discharge to suction differential pressure of
375 to 450 psi. This action will trip the motor protector
and remove the motor from the line. The ZB10-14KCE
models DO require a high pressure control in addition
to a low pressure control, since these models do not
have an IPR valve.
Internal Temperature Protection
Refrigeration Scroll compressors (1.3-7.5 HP)
ZB10-57KC/E incorporate a thermo disc which is a
temperature-sensitive snap disc device located at the
scroll discharge port. It is designed to open and route
hot discharge gas back to the motor protector thus
removing the compressor from the line.
Motor Protection
Conventional inherent internal line break motor protection
is provided.
Oil Types
Polyol ester lubricants must be provided if the scroll
compressor is to be used with HFC refrigerants. ZBKC
compressors are intended for use with R22 and are
supplied with mineral oil. See
Form 93-11
for a complete
list of all Emerson approved lubricants.