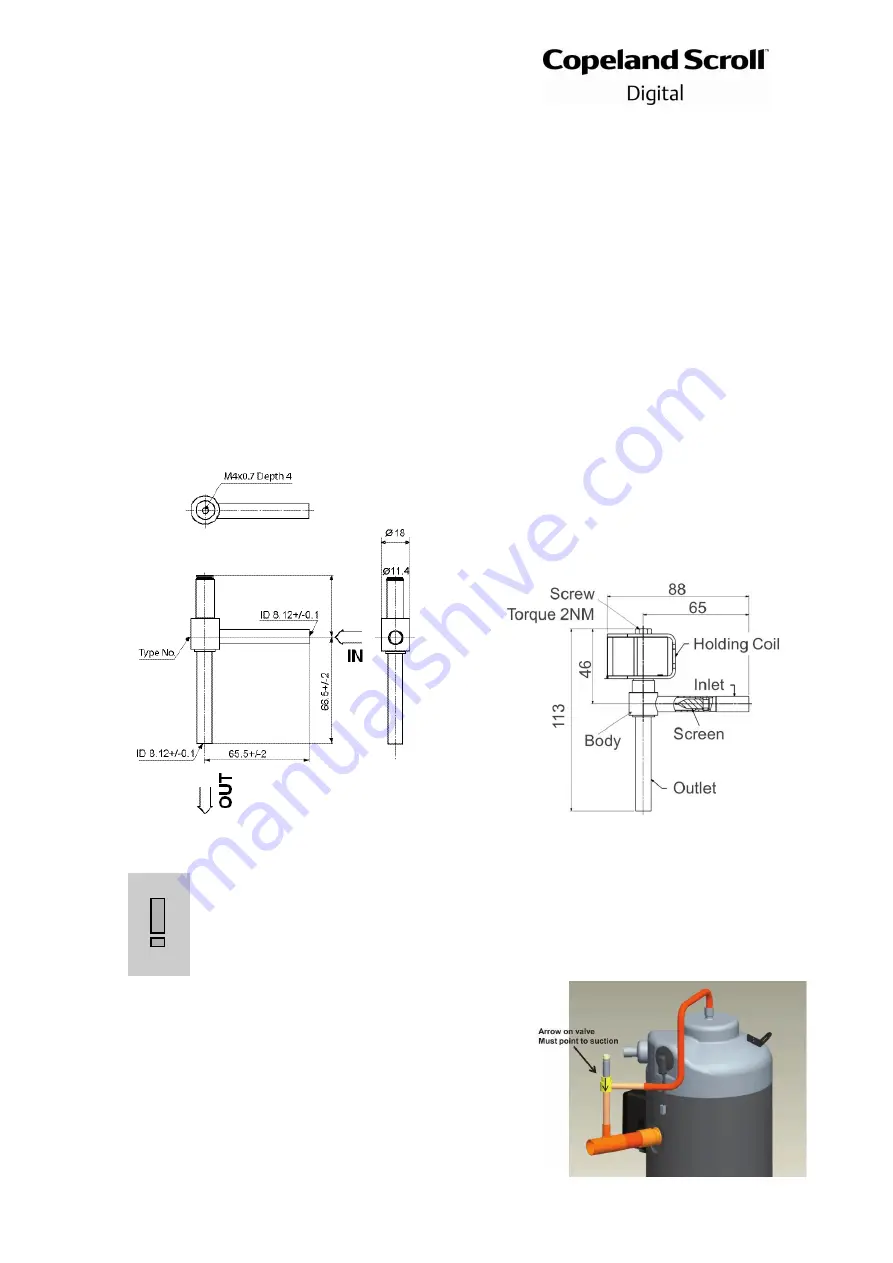
C6.2.44/0219/E
9
3.2.1 Solenoid valve installation
– General recommendations
▪
The solenoid must be mounted vertically, within ± 15° of vertical. Horizontal mounting is not
permitted.
▪
If a suction Rotalock fitting is used, the threaded shipping plug in the Rotalock fitting must be
removed prior to brazing in the vertical solenoid line.
▪
The valve operation is directional. See
Figure 6
below for inlet and outlet locations.
▪
Do not restrict the line size coming from or leaving the solenoid. Use 3/8" soft drawn copper.
▪
Mount the solenoid valve to the suction line. The tube from the solenoid to the suction should
be as short as possible, less than 3" (76 mm).
▪
From the top cap to the solenoid a series of bends and/or shock loops are required to dampen
vibrations and resonance frequencies the assemblies might see during operation and start-
up. Solenoid tubing mounting kits including solenoid valves are available from Emerson.
▪
The valve body contains a small filter mesh, to avoid large particles entering the inside (see
Figure 7
), which could lead to a defect and blockage. The filter is part of the valve delivery
and already crimped inside; it cannot be changed. This is different from previous valve body
versions, where the filter was delivered loose to the valve body and could be exchanged.
▪
The recommended tightening torque for the screw to fix the coil on the solenoid valve is
2 Nm.
Figure 6: Control valve without coil
Figure 7: Control valve with coil
3.2.2 Solenoid valve installation
– Tubing recommendations
IMPORTANT
This tube has been tested and qualified at 50 and 60 Hz operation for running
stresses and resonance in a single compressor lab environment. However, in
some compressor applications such as racks and transport applications, the
OEM is strongly advised to re-confirm the acceptability of the tube when the
compressor is subject to additional vibration inputs.
The tube from the solenoid to the suction, marked "A",
should be as short as possible (less than 7.5 cm).
Dimensions for a typical tube going from the top of the
compressor are shown in
Figures 8 & 9
.
Figure 8: Recommended piping